Industrial Chemical Reactor
Your Trusted Manufacturer and Supplier of Industrial Chemical Reactor
An Industrial Chemical Reactor is a crucial piece of equipment used in the chemical, pharmaceutical, petrochemical, and various other industries for carrying out chemical reactions on a large scale. These reactors are designed to facilitate controlled chemical transformations, ensuring efficiency, safety, and product quality. The role of an Industrial Chemical Reactor is vital in industries that require precise control over reaction conditions such as temperature, pressure, and mixing to achieve desired chemical products.
At SV Industries, we specialize in manufacturing high-quality Industrial Chemical Reactors that cater to the specific needs of our clients. Our reactors are engineered with advanced technology to ensure seamless operation, durability, and high performance. Whether it is batch reactors, continuous reactors, or specialized reactors, we offer customized solutions to match diverse industrial requirements.
The design and selection of an Industrial Chemical Reactor depend on various factors, including the type of chemical reaction, operating conditions, material of construction, and desired output. Key considerations such as heat transfer, reaction kinetics, and mixing efficiency play a significant role in achieving optimal performance.
In this detailed guide, we will explore everything about Industrial Chemical Reactors, including their types, working principles, design considerations, advantages, and applications. Whether you are an industry professional, a researcher, or someone interested in learning about reactors, this comprehensive guide will provide valuable insights into the world of Industrial Chemical Reactors.
What is a industrial chemical reactor?
An Industrial Chemical Reactor is a vital processing unit used in industries such as pharmaceuticals, petrochemicals, food production, and chemical manufacturing to carry out chemical reactions on a large scale. These reactors are specifically designed to control reaction conditions like temperature, pressure, and mixing, ensuring maximum efficiency, safety, and product quality. At SV Industries, we specialize in manufacturing high-performance Industrial Chemical Reactors tailored to meet the diverse needs of various industries.
The primary function of an Industrial Chemical Reactor is to provide a controlled environment where raw materials undergo chemical transformation into desired products. These reactors are built to handle different types of reactions, including polymerization, oxidation, hydrogenation, and synthesis processes. Depending on the type of reaction and operational requirements, Industrial Chemical Reactors come in various designs, such as batch reactors, continuous reactors, and specialized reactors.
At SV Industries, we manufacture Industrial Chemical Reactors using high-grade materials like stainless steel and carbon steel, ensuring durability and corrosion resistance. Our reactors are designed with advanced technology to meet industry standards, providing clients with reliable and long-lasting solutions. Whether for small-scale production or large industrial plants, our reactors are built to enhance productivity and safety.
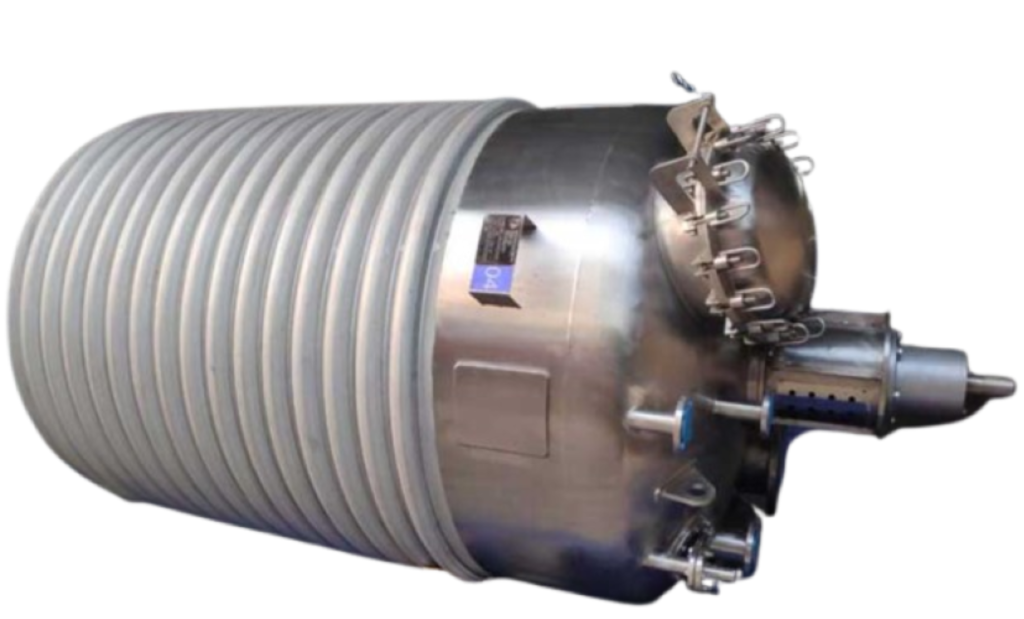
how does Industrial Chemical Reactor work?
An Industrial Chemical Reactor functions as a controlled environment where chemical reactions take place under precisely managed conditions. These reactors are designed to regulate temperature, pressure, mixing, and heat transfer to achieve the desired chemical transformation efficiently. At SV Industries, we manufacture high-performance Industrial Chemical Reactors that ensure optimal reaction control, high yield, and safety in various industrial processes.
Step-by-Step Working of an Industrial Chemical Reactor
Raw Material Feeding
The Industrial Chemical Reactor is fed with raw materials (reactants) in precise proportions. This can be done in batch mode, where all reactants are added at once, or continuous mode, where reactants are continuously introduced over time. Proper measurement and control of raw material input are essential for a successful reaction process.
Mixing and Agitation
Efficient mixing is necessary to ensure a homogeneous reaction. Many Industrial Chemical Reactors are equipped with agitators, impellers, or mechanical stirrers that help distribute reactants evenly and prevent localized overheating or unwanted side reactions.
Temperature and Pressure Control
Controlling temperature and pressure is critical in an Industrial Chemical Reactor. Some reactions require high temperatures, while others need cooling mechanisms to avoid overheating. Heat exchangers, jacketed vessels, and cooling coils are used to regulate the reactor’s internal conditions. Similarly, pressure control systems ensure that high-pressure reactions occur safely and efficiently.
Reaction Process
Once the reactants are properly mixed and reaction conditions are optimized, the chemical reaction takes place. The process could be exothermic (releasing heat) or endothermic (absorbing heat). The design of an Industrial Chemical Reactor ensures that the reaction progresses in a controlled manner, maximizing product yield while minimizing by-products and waste.
Heat and Mass Transfer
Efficient heat transfer ensures that the reaction occurs at a stable rate without overheating or undercooling. Additionally, proper mass transfer allows reactants to interact effectively, increasing reaction efficiency. This is particularly important in multiphase reactors, where liquids, gases, or solids must interact efficiently.
Separation and Product Removal
Once the reaction is complete, the Industrial Chemical Reactor facilitates product separation. Depending on the process, the final chemical product may be separated through filtration, distillation, or phase separation techniques. Any unreacted materials or by-products can be recycled or removed safely.
Safety Mechanisms and Monitoring
To ensure safe operation, an Industrial Chemical Reactor is equipped with automated control systems, pressure relief valves, emergency shut-off mechanisms, and real-time monitoring sensors. These safety features help prevent hazardous situations such as overheating, over-pressurization, or unexpected chemical reactions.
Customization Options for Industrial Chemical Reactor
At SV Industries, we understand that different industries have unique requirements when it comes to Industrial Chemical Reactors. That’s why we offer fully customizable solutions to meet specific process needs, production capacities, and safety standards. Our expertise in designing tailor-made Industrial Chemical Reactors ensures high efficiency, durability, and optimal performance for your chemical processing applications.
Key Customization Options for Industrial Chemical Reactors
Reactor Type and Design
We manufacture various types of Industrial Chemical Reactors, customized based on process requirements:
- Batch Reactors – Ideal for small-scale production and reactions that require flexibility.
- Continuous Reactors – Best for high-volume production with consistent output.
- Semi-Batch Reactors – Suitable for processes that require controlled addition of reactants.
- Plug Flow Reactors (PFR) – Designed for high-efficiency chemical processing in continuous operations.
- CSTR (Continuous Stirred Tank Reactors) – Used for homogeneous liquid-phase reactions with controlled mixing.
Material of Construction
The material of an Industrial Chemical Reactor is crucial for ensuring durability, corrosion resistance, and safety. We offer:
- Stainless Steel (SS 304, SS 316, SS 316L) – Excellent corrosion resistance and ideal for pharmaceutical, food, and chemical industries.
- Carbon Steel – Cost-effective and suitable for general chemical processing applications.
- Glass-Lined Reactors – Ideal for highly corrosive reactions involving acids or other aggressive chemicals.
- Hastelloy, Titanium, Inconel, and Other Alloys – Custom materials for extreme chemical resistance and high-temperature operations.
Capacity and Size
We design Industrial Chemical Reactors in various capacities, from small-scale lab reactors (100L-500L) to large industrial reactors (up to 20,000L or more). Custom dimensions and volumes can be tailored based on your production requirements.
Reaction Process
Once the reactants are properly mixed and reaction conditions are optimized, the chemical reaction takes place. The process could be exothermic (releasing heat) or endothermic (absorbing heat). The design of an Industrial Chemical Reactor ensures that the reaction progresses in a controlled manner, maximizing product yield while minimizing by-products and waste.
Pressure and Temperature Ratings
Our Industrial Chemical Reactors are built to withstand customized pressure and temperature conditions, including:
- Low-Pressure Reactors – Suitable for ambient pressure reactions.
- High-Pressure Reactors – Designed for hydrogenation, polymerization, and catalytic reactions.
- Cryogenic Reactors – Built for low-temperature reactions.
- High-Temperature Reactors – Suitable for exothermic reactions and thermal processing.
Heating and Cooling Systems
To maintain precise temperature control, we provide:
- Jacketed Reactors – Ideal for heating and cooling using steam, hot oil, or chilled water.
- Limpet Coil Reactors – Suitable for high-pressure and high-temperature reactions.
- External Heat Exchangers – Integrated for rapid cooling or heating based on process needs.
Agitation and Mixing Mechanisms
Efficient mixing and agitation are essential for reaction uniformity and process efficiency. We offer:
- Anchor Type Agitators – For high-viscosity fluids and pastes.
- Propeller Agitators – Ideal for low-viscosity liquid mixing.
- Turbine Agitators – Used in medium to high-viscosity chemical reactions.
- Magnetic Drive Agitators – Designed for leak-proof, contamination-free applications.
Automation and Control Systems
We integrate advanced automation into our Industrial Chemical Reactors for precise process control:
- PLC-Based Automated Control Systems – Ensures real-time monitoring and automation.
- SCADA Integration – Allows remote control and data logging.
- Temperature, Pressure, and pH Sensors – For real-time process optimization.
Coating and Lining Options
For handling corrosive chemicals, we offer:
- Glass-Lined Coating – For acidic and highly corrosive substances.
- PTFE / Teflon Coating – Suitable for chemical inertness.
- Rubber Lining – Used in alkaline or acidic reaction environments.
At SV Industries, we provide end-to-end solutions for Industrial Chemical Reactors, ensuring that our clients receive the most efficient, reliable, and cost-effective reactor systems for their chemical processing needs. Whether you need a small-scale batch reactor or a high-capacity continuous processing unit, we have the expertise to deliver customized solutions that meet your production demands.
Major Industrial Applications of Industrial Chemical Reactors
Chemical and Petrochemical Industry
- Used for the production of organic and inorganic chemicals, including acids, alkalis, and solvents.
- Essential in cracking, reforming, alkylation, and hydrogenation reactions in petroleum refining.
- Enables the production of synthetic resins, plastics, and rubbers through polymerization reactions.
Pharmaceutical Industry
- Industrial Chemical Reactors play a key role in drug synthesis, formulation, and active pharmaceutical ingredient (API) production.
- Used for fermentation and crystallization processes in antibiotic and vaccine production.
- Essential in the manufacturing of biopharmaceuticals, vitamins, and complex organic compounds.
Food and Beverage Industry
- Used in the production of flavors, preservatives, and food additives through controlled chemical reactions.
- Applied in fermentation processes for the production of alcoholic beverages, dairy products, and probiotic foods.
- Helps in the hydrogenation of oils and fats, ensuring improved texture and shelf life of food products.
Polymer and Plastic Industry
- Crucial in the production of polymers such as polyethylene (PE), polypropylene (PP), and polystyrene (PS) through polymerization reactions.
- Used in the manufacturing of synthetic rubbers, adhesives, and resins for various industrial applications.
- Supports recycling processes where waste plastics are chemically broken down into reusable materials.
Oil and Gas Industry
- Used in hydrocracking, catalytic reforming, and desulfurization processes to refine crude oil into fuel products.
- Essential for the synthesis of petrochemicals, including ethylene, propylene, and benzene.
- Helps in the production of lubricants, greases, and specialty chemicals.
Agrochemical Industry (Fertilizers and Pesticides)
- Industrial Chemical Reactors are used in the synthesis of fertilizers, pesticides, herbicides, and fungicides.
- Plays a role in chemical processing for crop protection products.
- Helps in the development of biodegradable and environmentally friendly agrochemicals.
Textile and Dye Industry
- Used in the synthesis of dyes, pigments, and textile chemicals to enhance fabric properties.
- Applied in bleaching and finishing processes to improve the color fastness and durability of textiles.
- Helps in the production of synthetic fibers like nylon, polyester, and rayon.
Water Treatment and Environmental Industry
- Used in wastewater treatment plants for the synthesis of chemical coagulants and disinfectants.
- Supports advanced oxidation processes (AOPs) for breaking down organic pollutants.
- Helps in the production of activated carbon and adsorbents for water purification.
Biochemical and Biotechnology Industry
For handling corrosive chemicals, we offer:
- Glass-Lined Coating – For acidic and highly corrosive substances.
- PTFE / Teflon Coating – Suitable for chemical inertness.
- Rubber Lining – Used in alkaline or acidic reaction environments.
No matter your industry, our Industrial Chemical Reactors ensure precision, reliability, and cost-effectiveness in every application. Contact SV Industries today for the best reactor solutions tailored to your industrial needs!
SV Industries: Leading Manufacturer of Industrial Chemical Reactors
At SV Industries, we specialize in the design, manufacturing, and supply of high-quality Industrial Chemical Reactors for various industries, including pharmaceuticals, chemicals, petrochemicals, food processing, and biotechnology. With a commitment to innovation, quality, and customer satisfaction, we provide customized reactor solutions that ensure high efficiency, durability, and safety for all types of chemical processes.
Why Choose SV Industries for Industrial Chemical Reactors?
Advanced Engineering & Precision Manufacturing
At SV Industries, we use cutting-edge technology and advanced engineering to design Industrial Chemical Reactors that meet high-performance standards. Our reactors are built to handle complex chemical reactions while ensuring maximum productivity and safety.
High-Quality Materials & Robust Construction
We manufacture Industrial Chemical Reactors using premium-grade materials, ensuring durability and corrosion resistance. Our reactors are available in:
- Stainless Steel (SS 304, SS 316, SS 316L) for corrosion resistance
- Carbon Steel for high-strength applications
- Glass-Lined Reactors for acidic and highly corrosive reactions
- Hastelloy, Titanium, Inconel for extreme chemical environments
Customization & Tailored Solutions
We offer fully customizable Industrial Chemical Reactors, tailored to meet specific process requirements, reaction types, capacity needs, and automation levels. Our customization options include:
✔ Reactor Type – Batch, Continuous, Semi-Batch, CSTR, Plug Flow
✔ Capacity Range – From 100L to 20,000L
✔ Pressure & Temperature Ratings – High-pressure, high-temperature, cryogenic options
✔ Agitation & Mixing – Anchor, propeller, turbine, magnetic agitators
✔ Heating & Cooling Systems – Jacketed, limpet coil, external heat exchangers
✔ Automation & Control Systems – PLC, SCADA, real-time monitoring
Industry-Specific Applications
Our Industrial Chemical Reactors are designed to serve a wide range of industries:
- Pharmaceutical & Biotech – API synthesis, fermentation, crystallization
- Chemical & Petrochemical – Polymerization, oxidation, hydrogenation
- Food & Beverage – Fermentation, flavor production, hydrogenation of oils
- Agrochemical – Fertilizer and pesticide production
- Water Treatment & Environmental – Chemical coagulants, oxidation processes
With years of experience in reactor manufacturing, SV Industries is dedicated to delivering high-performance, cost-effective, and reliable reactor solutions. Whether you need a customized batch reactor or a large-scale continuous reactor, we have the expertise to design and manufacture reactors that optimize your production efficiency and operational safety.
Frequently Asked Questions (FAQs)
What is an Industrial Chemical Reactor?
An Industrial Chemical Reactor is a specialized vessel used in industries to facilitate and control chemical reactions efficiently. These reactors are designed to handle temperature, pressure, and mixing requirements to optimize the chemical process and ensure safe and high-yield production.
What materials are used to manufacture Industrial Chemical Reactors?
At SV Industries, we manufacture reactors using high-quality materials such as:
✔ Stainless Steel (SS 304, SS 316, SS 316L) – Ideal for corrosion resistance.
✔ Carbon Steel – Cost-effective and durable for general chemical applications.
✔ Glass-Lined Reactors – Used for acidic and highly corrosive chemical reactions.
✔ Special Alloys (Hastelloy, Titanium, Inconel) – For extreme chemical resistance and high temperatures.
How do Industrial Chemical Reactors work?
An Industrial Chemical Reactor works by providing a controlled environment for chemical reactions to take place efficiently. It regulates:
✔ Temperature – Ensures the reaction occurs at the optimal heat level.
✔ Pressure – Controls reaction rate and safety.
✔ Agitation & Mixing – Ensures even distribution of reactants.
✔ Reaction Time – Determines how long reactants stay inside the reactor to achieve desired conversion rates.
What industries use Industrial Chemical Reactors?
Industrial Chemical Reactors are widely used in:
✔ Pharmaceutical Industry – For drug synthesis and fermentation.
✔ Chemical & Petrochemical Industry – For polymerization, oxidation, and refining.
✔ Food & Beverage Industry – In fermentation and food processing.
✔ Agrochemical Industry – For fertilizers, pesticides, and herbicides.
✔ Biotechnology Industry – For biofuel production and enzyme reactions.
How do I choose the right Industrial Chemical Reactor for my process?
Choosing the right Industrial Chemical Reactor depends on:
✔ Reaction Type – Batch or continuous processing?
✔ Operating Conditions – Temperature, pressure, and mixing requirements.
✔ Material Compatibility – Reactors must be resistant to the chemicals being processed.
✔ Production Capacity – Determining the reactor size and output volume.
✔ Automation Needs – Manual, semi-automated, or fully automated operation.
At SV Industries, our experts assist in selecting the best Industrial Chemical Reactor for your specific process requirements.
Can Industrial Chemical Reactors be customized?
Yes! At SV Industries, we offer fully customizable Industrial Chemical Reactors based on:
✔ Reactor Type & Design (Batch, Continuous, CSTR, PFR, etc.).
✔ Material of Construction (SS, Carbon Steel, Glass-Lined, Hastelloy).
✔ Heating & Cooling Options (Jacketed, Limpet Coil, Heat Exchangers).
✔ Agitation & Mixing Mechanism (Anchor, Turbine, Propeller Agitators).
✔ Automation & Control Systems (PLC, SCADA, Remote Monitoring).
We tailor our Industrial Chemical Reactors to meet specific industry requirements for maximum efficiency and performance.
What maintenance is required for an Industrial Chemical Reactor?
Regular maintenance ensures optimal performance and long service life of an Industrial Chemical Reactor. Recommended maintenance includes:
✔ Cleaning & Inspection – Regular inspection of reactor vessels, agitators, and seals.
✔ Checking Temperature & Pressure Sensors – Ensuring they function correctly.
✔ Lubrication of Agitators & Moving Parts – To prevent wear and tear.
✔ Inspecting Safety Valves & Automation Controls – Ensuring proper functioning of shutdown and alarm systems.
✔ Corrosion Monitoring – Checking material integrity in corrosive environments.
At SV Industries, we provide after-sales support and maintenance services for all our reactors.
Why choose SV Industries for Industrial Chemical Reactors?
At SV Industries, we specialize in high-quality Industrial Chemical Reactors that ensure efficiency, durability, and safety. Our advantages include:
✔ Expert Engineering & Precision Manufacturing
✔ Customizable Reactor Solutions Based on Industry Needs
✔ Use of High-Grade Materials for Corrosion & Heat Resistance
✔ Advanced Automation & Control Systems for Process Optimization
✔ Compliance with International Safety & Quality Standards (ASME, GMP, ISO, CE)
✔ Affordable Pricing & On-Time Delivery
Why SV Industries Stands Out
An Industrial Chemical Reactor is a crucial component in various industries, enabling precise and controlled chemical reactions for pharmaceuticals, chemicals, petrochemicals, food processing, agrochemicals, and more. The choice of reactor depends on factors such as reaction type, operating conditions, material compatibility, and automation needs.
At SV Industries, we specialize in designing and manufacturing high-quality Industrial Chemical Reactors that meet the highest industry standards for efficiency, durability, and safety. Our reactors are customizable, ensuring they align perfectly with your specific process requirements. We use premium materials, integrate advanced automation, and ensure strict quality control to deliver high-performance reactor solutions.
With our expertise, innovative technology, and commitment to customer satisfaction, SV Industries is your trusted partner for Industrial Chemical Reactors. Whether you need a batch, continuous, or specialized reactor, we provide cost-effective and reliable solutions for your manufacturing needs.