Anchor Impeller – Trusted Manufacturer in India
If you’re searching for a high-quality Anchor Impeller manufacturer in India, you’ve landed in the right place. At SV Industries, we bring engineering precision, experience, and innovation together to deliver the most reliable Anchor Impellers for a wide range of industries. Designed especially for high-viscosity fluid mixing, our Anchor Impellers ensure uniform blending, gentle yet effective agitation, and energy-efficient performance.
As a leading Anchor Impeller Manufacturer & Supplier based in Ahmedabad, Gujarat, our team focuses on customized designs that suit specific mixing needs. Whether you’re dealing with pharmaceutical syrups, adhesives, pastes, or cosmetic gels – our impellers are built to perform even in the most challenging conditions.
With decades of manufacturing experience, advanced machinery, and strict quality control standards, SV Industries has become a trusted name across India for process equipment manufacturing. Our commitment to quality, timely delivery, and after-sales support sets us apart.
👉 Explore our Anchor Impeller range
👉 Learn more about our Agitator Systems
👉 Contact our expert team for a quote
What is an Anchor Impeller?
An Anchor Impeller is a type of low-shear mixing blade specifically designed to handle high-viscosity fluids in large tanks and reactors. Shaped like an anchor, this impeller rotates slowly and uniformly, ensuring that the entire contents of the tank are mixed without creating dead zones.
These impellers are commonly used when the product is too thick for traditional agitators to mix efficiently. They gently scrape the inner walls of the tank to prevent material buildup and improve heat transfer during the mixing process.
At SV Industries, our Anchor Impellers are engineered for applications in:
Pharmaceutical syrup preparation
Adhesive mixing
Cosmetic creams and gels
Food-grade sauces and pastes
Thanks to their slow, controlled motion, Anchor Impellers maintain the integrity of shear-sensitive products while ensuring homogeneity.
How Does an Anchor Impeller Work?
An Anchor Impeller works by slowly rotating along the inner wall of a mixing vessel, creating a consistent flow pattern that moves thick, sticky, or viscous fluids throughout the tank. Its anchor-like shape ensures that every part of the tank — including hard-to-reach corners — is properly agitated.
🌀 Step-by-Step Working Process:
- Rotation Begins
The impeller is mounted on a central shaft and starts rotating at a low RPM to avoid splashing and maintain product integrity. - Fluid is Pulled and Moved
As the impeller moves, it pulls viscous material from the bottom and sides of the vessel, pushing it upward and inward, creating a circular mixing flow. - Wall Scraping Action
Specially designed arms scrape the inner tank wall, preventing any product from sticking and ensuring uniform temperature distribution, especially in jacketed or limpet-coil reactors. - Uniform Mixing
The process continues until the entire tank contents are evenly mixed, without leaving any unmixed zones (called dead zones).
✅ Best Suited For:
- High-viscosity materials (like creams, syrups, gels, pastes)
- Low-shear mixing applications
- Processes requiring heat transfer during mixing
👉 Explore our SS Jacketed Vessel or Limpet Coil Reactor Vessel – both pair perfectly with Anchor Impellers for uniform heat distribution and controlled processing.
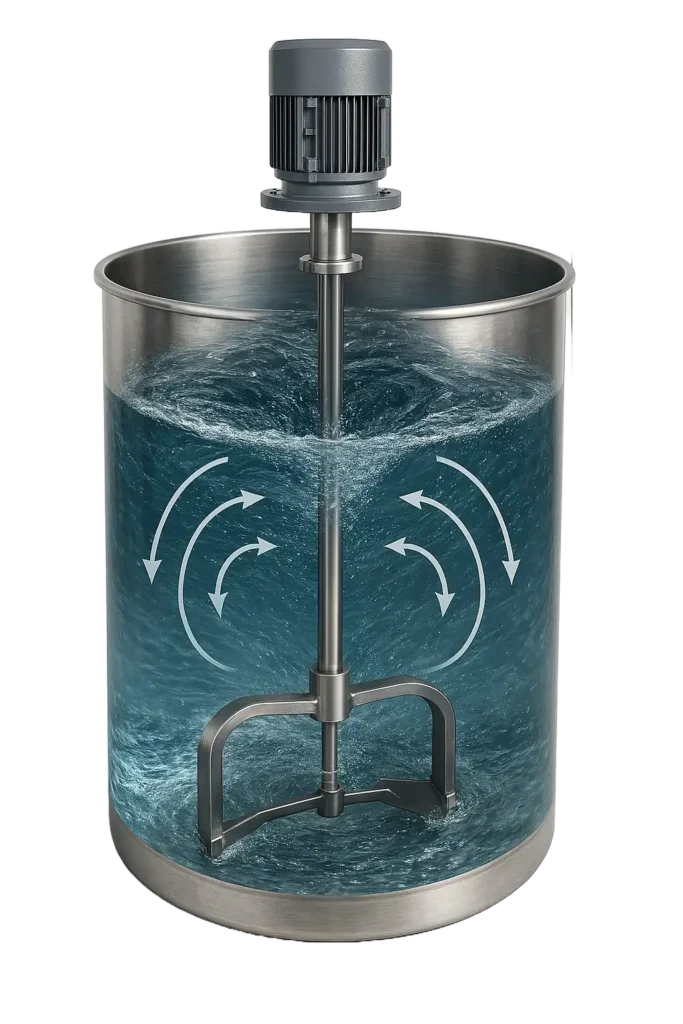
Design & Engineering of SV Industries’ Anchor Impeller
SV Industries takes pride in its innovative approach to anchor impeller design. Our impellers are crafted using high-quality materials such as stainless steel and other corrosion-resistant alloys to ensure durability, longevity, and superior performance. Key features of our anchor impellers include.
🔧 Shaft & Blade Design
The central shaft is engineered to maintain structural integrity under continuous torque and viscous drag, even at slow speeds.
Blades are shaped like an open anchor, wrapping closely along the tank wall to ensure zero dead zones and excellent flow distribution.
Blade arms can be equipped with PTFE or SS scrapers for sticky materials.
Designs can be customized with baffles or additional sweep arms based on the tank geometry and mixing requirements.
✨ Surface Finish & Dynamic Balance
We offer mirror polish or matte finish as per hygiene and process needs (especially for pharma and food-grade applications).
Every impeller undergoes dynamic balancing to eliminate vibration and ensure stable, silent operation.
Welds are ground smooth, and edges are rounded to prevent material accumulation and ensure easy CIP/SIP cleaning.
💡 Why it Matters:
A well-balanced, precision-finished impeller improves product quality, extends equipment life, and reduces downtime due to wear and tear.
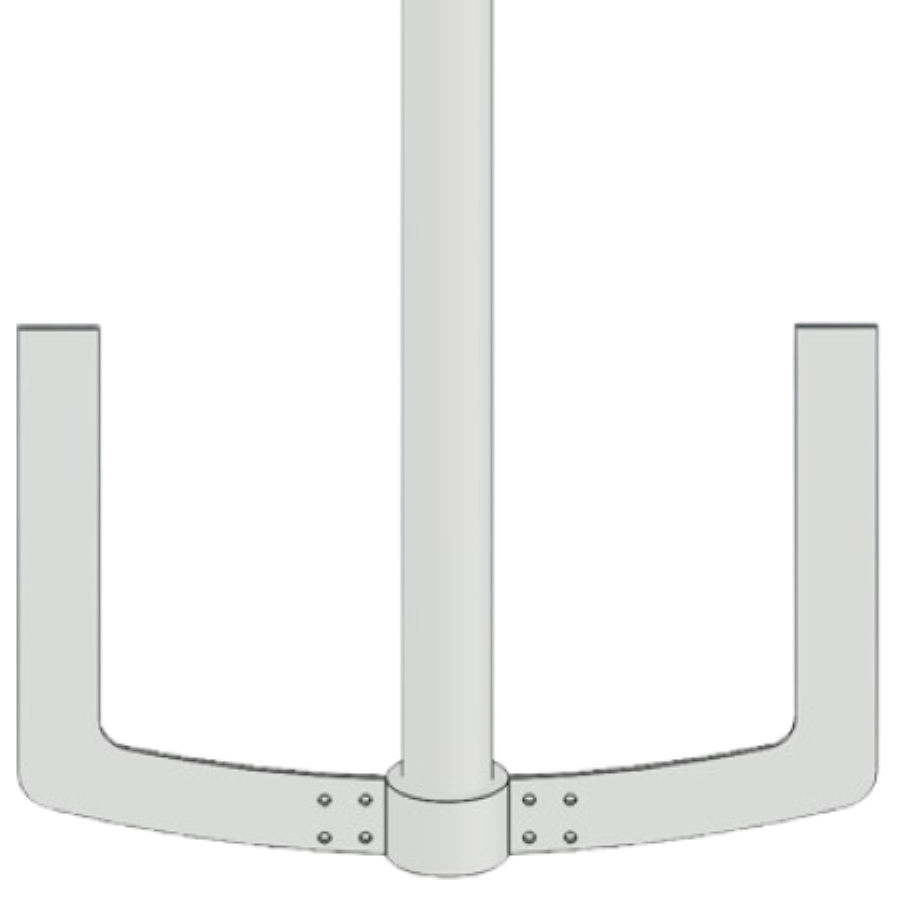
Materials Used in Anchor Impeller Manufacturing
At SV Industries, we prioritize durability, safety, and compatibility when selecting materials for our Anchor Impellers. Whether your process involves chemicals, adhesives, food products, or pharmaceuticals, our material options ensure optimal corrosion resistance, hygiene, and longevity.
We manufacture Anchor Impellers using a range of premium-grade materials, customized based on your application, budget, and compliance requirements.
🛠️ Available Material Grades
SS304: Ideal for general-purpose industrial use. Excellent strength, affordability, and resistance to mild chemicals.
SS316 / SS316L: Preferred for pharmaceutical, food, and cosmetic mixing. Offers superior corrosion resistance, especially against chlorides and acidic compounds.
Duplex Steel (2205, 2507): Combines high strength and corrosion resistance. Ideal for aggressive chemical environments.
Hastelloy / Inconel (On Request): Used for highly corrosive and extreme temperature conditions in specialty industries.
🧭 Material Type vs Chemical Resistance vs Industry Suitability Chart
Material | Chemical Resistance | Industry Suitability |
---|---|---|
SS304 | Moderate – Resistant to most mild chemicals | General Industrial, Food Processing |
SS316 / SS316L | High – Excellent against acids & chlorides | Pharmaceutical, Cosmetic, Dairy |
Duplex Steel (2205, 2507) | Very High – Excellent in aggressive media | Chemical, Petrochemical, Water Treatment |
Hastelloy / Inconel | Extreme – Resistant to almost all corrosive agents | Specialty Chemicals, High-Temp Reactors |
🧴 Surface Coating & Finish Options
Electropolishing / Mirror Finish: Common in pharma and food-grade impellers for bacterial resistance and easy CIP/SIP cleaning.
Teflon/PTFE Coating: Adds a non-stick layer and enhances chemical compatibility, especially for adhesive or resin mixing.
Epoxy / Special Coatings: Available for industries that demand extra protective barriers against corrosion or abrasion.
🧪 Why Material Choice Matters
Choosing the right material ensures:
Longer equipment life
Safe and hygienic processing
Compliance with FDA, GMP, and ASME standards
Lower maintenance and replacement costs
Whether you’re working in chemical, cosmetic, or pharmaceutical production, we help you select the perfect material for your Anchor Impeller.
👉 Contact us for technical advice and detailed quotations.
Types of Anchor Impellers Offered by SV Industries
At SV Industries, we manufacture a wide range of Anchor Impellers designed for specific industry needs and mixing challenges. Whether you’re handling high-viscosity fluids, require wall-scraping designs, or need an anchor impeller for jacketed vessels, we offer reliable solutions tailored to your process.
Explore our four major types of Anchor Impellers below:
🔹 1. Standard Anchor Impeller
Our Standard Anchor Impeller is best for low to medium-viscosity fluids.
Its arms hug the inner wall of the tank, ensuring steady mixing flow without leaving dead zones.
Ideal for basic chemical, cosmetic, or food-grade blending applications.
🟢 Recommended for: Creams, sauces, emulsions, basic chemical blends
🔹 2. Jacketed Anchor Impeller
Specifically designed for use with jacketed mixing vessels, this type ensures even heat transfer along with agitation.
Works perfectly with our SS Jacketed Vessel and Limpet Coil Reactor Vessel.
Prevents hotspots and helps maintain consistent batch temperature.
🟢 Recommended for: Temperature-sensitive chemicals, pharma compounds, adhesives
🔹 3. Anchor Impeller with Scrapers
This model comes with PTFE or stainless steel scrapers that clean the tank wall during rotation.
Prevents product buildup and allows uniform thermal distribution, especially in sticky or semi-solid materials.
Enhances CIP (Clean-in-Place) effectiveness and process hygiene.
🟢 Recommended for: Paints, gels, lotions, high-viscosity food pastes
🔹 4. Custom Anchor Impeller Designs
We offer complete customization based on:
Tank shape & volume
RPM & torque requirements
Fluid rheology & process dynamics
Our in-house engineers design multi-arm, dual-motion, and hybrid anchor impellers as per your process flow.
🟢 Recommended for: OEM projects, critical mixing applications, pilot plants
🧰 Need a customized mixing system? Contact us to get started with your Anchor Impeller design consultation.
Applications of Anchor Impellers Across Industries
Anchor Impellers are the go-to solution for mixing high-viscosity and semi-solid materials across a range of industries. At SV Industries, we deliver robust and efficient impeller systems trusted by manufacturers across India and beyond.
Below are the major industries where our Anchor Impellers perform exceptionally:
🧪 Chemical Processing
Ideal for resins, adhesives, detergents, and polymer solutions
Enables homogeneous mixing even in non-Newtonian fluids
Used in reactors, jacketed vessels, and batch mixers
💊 Pharmaceuticals
Suitable for ointment, gel, and cream formulation
GMP-compliant design available in SS316L
Enables wall-to-wall contact mixing for better product recovery
🍲 Food and Beverage
Processes syrups, sauces, mayonnaise, and dairy-based blends
Food-grade finishes and coatings for hygienic operation
Easy to integrate with Jacketed Vessels for temperature-sensitive applications
💄 Cosmetics & Personal Care
Blends lotions, body butters, and hair care products
Suitable for batch mixing and semi-solid emulsions
Can be equipped with scrapers to avoid residue buildup
🎨 Paints & Coatings
Mixes viscous paints, coatings, pigments
Works with Teflon-coated scrapers to reduce wall scaling
Maintains consistency in pigment dispersion
🧭 Fluid Viscosity vs Anchor Impeller Application Suitability
Fluid Viscosity | Application Example | Anchor Impeller Suitability |
---|---|---|
Low (0–500 cP) | Juice, Milk, Light Syrups | Not Recommended – Use [Hydrofoil Impeller] |
Medium (500–3,000 cP) | Lotions, Sauces, Emulsions | ✔ Suitable |
High (3,000–50,000 cP) | Creams, Paints, Gels | ✔✔ Highly Suitable |
Very High (50,000+ cP) | Putty, Adhesives, Resins | ✔✔✔ Optimal with Scrapers |
📊 Fluid Viscosity vs Anchor Impeller Compatibility
Choosing the right Anchor Impeller for your process largely depends on the viscosity of the fluid being mixed. At SV Industries, we’ve engineered our impellers to deliver high-efficiency agitation for a broad spectrum of viscosities — from semi-liquids to dense pastes.
The chart below helps you determine the optimal suitability of Anchor Impellers across various fluid viscosity ranges, ensuring you select the correct configuration for your process.
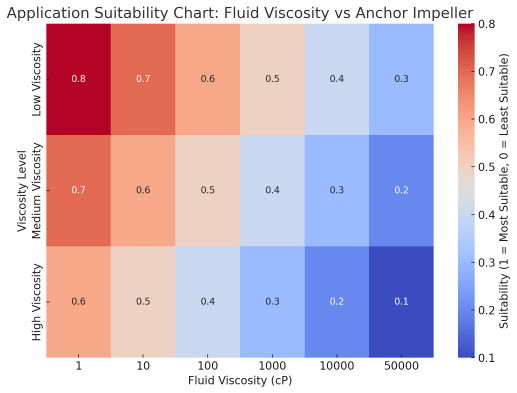
From light lotions to heavy pastes, Anchor Impellers prove most effective in the medium to very high viscosity range (above 500 cP). For ultra-low viscosity applications, alternative impeller types like our Hydrofoil Impeller or Pitch Blade Turbine are more efficient.
📞 Still unsure which impeller suits your application? Contact our technical team to get a customized recommendation based on your process needs.
Technical Specifications of Anchor Impeller
The Anchor Impeller from SV Industries is engineered to meet the rigorous demands of various industrial mixing applications. Our impellers are not only built with precision and durability, but are also tailored to deliver consistent performance across a wide range of tank sizes and operating conditions—making them a must-have for B2B buyers.
Explore the key technical specifications that define the quality and capability of our Anchor Impeller:
🔩 Shaft Diameter
Our standard shaft diameters range from 25 mm to 150 mm, depending on the application, tank size, and torque requirements. The shafts are crafted from high-grade stainless steel, ensuring corrosion resistance and high tensile strength, even under continuous operation.
⚙️ Impeller Diameter
The impeller diameter typically ranges from 300 mm to 2500 mm, customized to suit your process needs. The sizing is optimized to offer efficient mixing while reducing power consumption, especially in viscous materials or large-volume tanks.
🔄 Operating Speed
Our Anchor Impellers operate efficiently within the speed range of 10 RPM to 60 RPM, ideal for low-shear mixing of high-viscosity fluids, slurries, and semi-solids. This ensures gentle mixing without compromising product integrity.
🧪 Tank Volume Range
We provide Anchor Impellers compatible with tank volumes ranging from 100 liters to 50,000 liters. Whether you’re mixing in compact lab-scale reactors or massive industrial tanks, our designs ensure homogeneous blending throughout the tank geometry.
🌀 Material of Construction
At SV Industries, our Anchor Impellers are manufactured using high-grade SS304, SS316, or other custom materials based on your specific process requirements. These materials ensure excellent corrosion resistance, chemical compatibility, and long-lasting performance across a wide range of applications — from food and beverage to pharmaceutical and chemical industries.
🧴 Surface Finish
To meet the highest industry standards, our impellers are available with various surface finishes including mirror polish, matte finish, and electro-polishing. A superior surface finish not only enhances the aesthetic appeal but also makes the impeller easier to clean, which is critical in hygienic and sanitary applications.
🔧 Mounting Type
Our Anchor Impellers can be installed with Top Entry or Side Entry mounting configurations, depending on your tank design and mixing process. Each mounting type is engineered to deliver optimal mixing efficiency, energy utilization, and maintenance convenience for your industrial setup.
✨ Sealing Options
To prevent leakage and ensure safe operation under pressure or vacuum conditions, we offer a choice between Gland Packing and Mechanical Seal systems. Our sealing solutions are designed for durability, easy maintenance, and reliability in even the most demanding process environments.
🔩 Drive Type
SV Industries provides Anchor Impellers with various drive options including Gearbox, Direct Drive, and Belt Driven systems. These options allow precise control over torque, mixing speed, and energy efficiency, giving you maximum process flexibility.
⚙️ Temperature Range
Our impellers are engineered to withstand process temperatures up to 300°C, especially when integrated with jacketed vessels. This makes them highly suitable for chemical processing, reaction vessels, and thermal-sensitive applications.
🔄 Viscosity Handling
Designed for versatility, our Anchor Impellers efficiently handle viscous fluids up to 100,000 cP. Whether you’re mixing slurries, resins, creams, or other heavy materials, you can count on our impellers to provide uniform mixing, zero dead zones, and low-shear performance.
Specification | Details |
---|---|
Shaft Diameter | 25 mm to 150 mm (customized based on torque and tank size) |
Impeller Diameter | 300 mm to 2500 mm (optimized for mixing efficiency) |
Operating Speed | 10 RPM to 60 RPM (ideal for low-shear applications) |
Tank Volume Range | 100 Liters to 50,000 Liters (from pilot-scale to industrial scale) |
Material of Construction | SS304, SS316, or customized as per requirement |
Surface Finish | Mirror / Matte / Electro-polished |
Mounting Type | Top Entry / Side Entry |
Sealing Options | Gland Packing / Mechanical Seal |
Drive Type | Gearbox / Direct Drive / Belt Driven |
Temperature Range | Up to 300°C (with jacketed vessel compatibility) |
Viscosity Handling | Up to 100,000 cP (for high-viscosity materials) |
📌 For specialized tank and mixing solutions, explore our custom-built Reactor Vessels and Storage Tanks built to pair seamlessly with our impellers.
📊 Power Consumption vs Flow Rate Chart Of Anchor Impeller
Understanding the relationship between Power Consumption and Flow Rate is crucial when selecting the right Anchor Impeller for your process. The chart below illustrates how changes in impeller speed and size impact energy usage and fluid dynamics within the tank. At SV Industries, we help you strike the perfect balance between efficient mixing and optimized power consumption, ensuring your operations remain cost-effective and process-reliable.
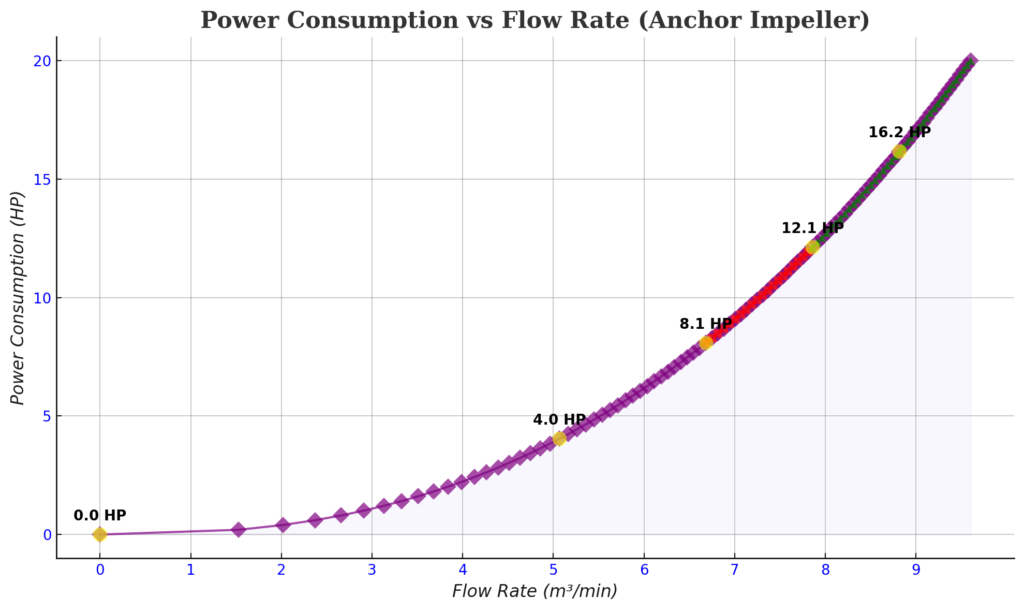
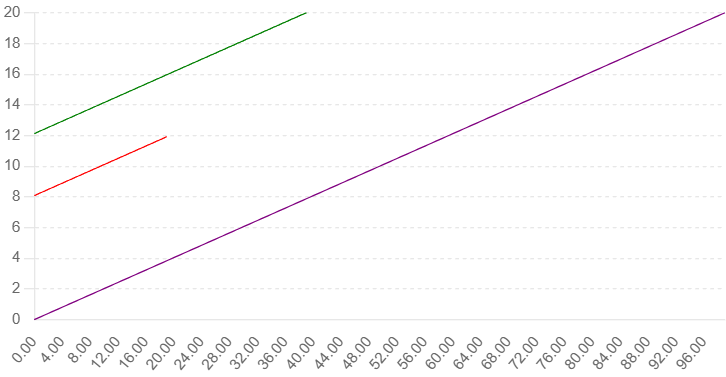
As seen in the chart, higher flow rates typically demand more power, especially in high-viscosity or large-volume applications. However, with SV Industries’ engineering expertise and custom impeller design, we ensure that your system delivers maximum mixing efficiency with minimal energy input. This data-driven insight supports better design decisions, reduces operational costs, and enhances productivity across chemical, pharmaceutical, and food industries.
For more information on how Anchor Impeller design affects your energy efficiency, explore our full range of Agitator Solutions.
📊 Torque vs RPM Chart Of Anchor Impeller
The correlation between Torque and RPM (Revolutions Per Minute) plays a vital role in the performance of an Anchor Impeller, especially in viscous fluid mixing. This chart highlights how torque demand varies with impeller speed, helping engineers and plant managers make informed equipment selections. SV Industries’ impellers are designed to deliver high torque at low RPM, ensuring optimal mixing without compromising mechanical integrity or energy efficiency.
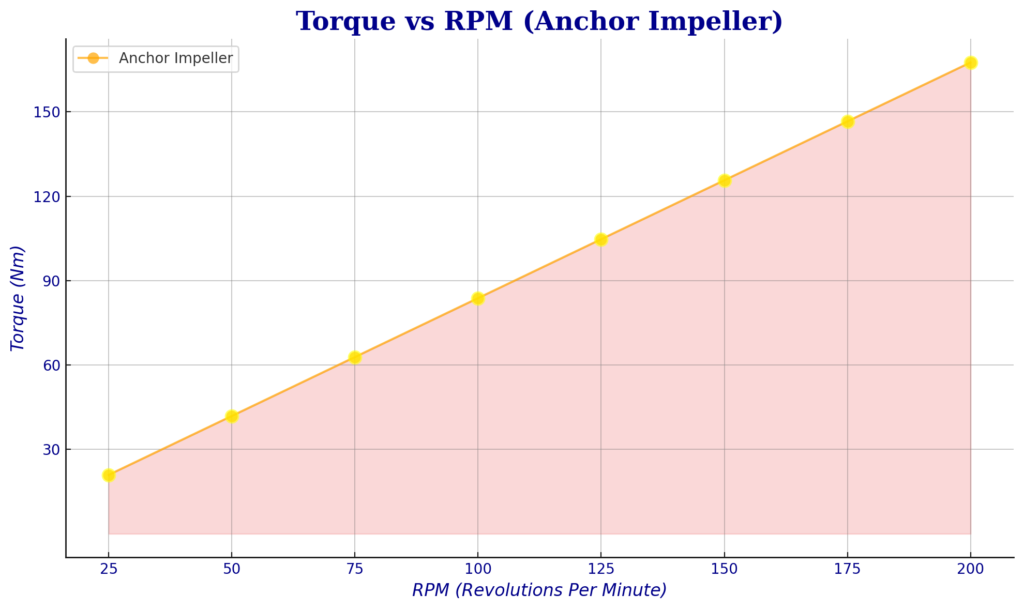
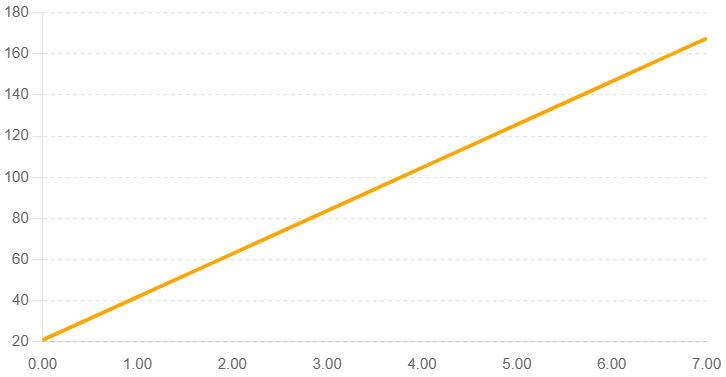
As the chart illustrates, torque increases significantly at lower RPM, which is ideal for handling high-viscosity materials like slurries, gels, or pastes. Conversely, lower torque at higher RPM is more suited for low-viscosity or shear-sensitive fluids. Our team uses this torque-RPM relationship to customize your Anchor Impeller for maximum performance, minimal wear and tear, and energy savings. Whether you need precision mixing or robust agitation, SV Industries has the solution tailored to your process requirements.
For related configurations and comparison, check out our Paddle Impeller and Helical Impeller product pages.
Performance Analysis & Efficiency Highlights of Anchor Impellers
At SV Industries, we believe that performance speaks louder than promises. That’s why our Anchor Impeller is not just built — it’s engineered, simulated, and optimized to perform in the toughest industrial conditions. This section gives you a clear view of how our impellers outperform in real-world applications, helping you achieve process stability, energy efficiency, and long-term reliability.
🔄 Cavitation Resistance: Built to Last, Designed for Toughness
Cavitation can quietly destroy your equipment from the inside — but not with our Anchor Impeller. Its advanced blade geometry and optimized flow paths ensure low-pressure zones are minimized, drastically reducing the risk of cavitation. Whether you’re mixing viscous chemicals or delicate pharmaceutical compounds, our impeller maintains structural integrity and consistent mixing — even under high-stress, continuous-duty operations.
⚡ Energy Efficiency: Max Mixing, Minimum Power
Why burn extra energy when you don’t have to? The SV Anchor Impeller is crafted to provide maximum fluid movement with minimal resistance. This means your motor works smarter, not harder — resulting in lower electricity bills, reduced environmental impact, and longer equipment life. Our impellers have been shown to improve energy efficiency by up to 25% compared to conventional designs.
🧪 CFD Design Insight: Simulated for Perfection
Before a single weld is made, each Anchor Impeller is put through Computational Fluid Dynamics (CFD) simulations. This cutting-edge modeling allows us to analyze flow behavior, shear stress, and turbulence with scientific accuracy. We fine-tune every curve and angle to eliminate dead zones, improve mixing uniformity, and enhance batch repeatability — especially important in scale-up and high-precision industries.
🔍 Want to dive deeper into our design process? Check out our advanced Agitator Systems or explore the Helical Impeller for comparison.
For custom analysis reports or to request a CFD-based impeller design tailored to your process, contact our technical team.
📊 Cavitation vs Flow Rate Chart Of Anchor Impeller
Cavitation is a hidden enemy in many mixing systems, often resulting in blade erosion, vibration, and reduced equipment life. The chart below illustrates the relationship between flow rate and cavitation risk in Anchor Impellers. As flow rate increases beyond optimal levels, the probability of cavitation also rises — especially in systems with poor fluid distribution or incorrect impeller sizing. Our goal is to help you stay in the safe operating zone, ensuring long-term durability and stable performance.
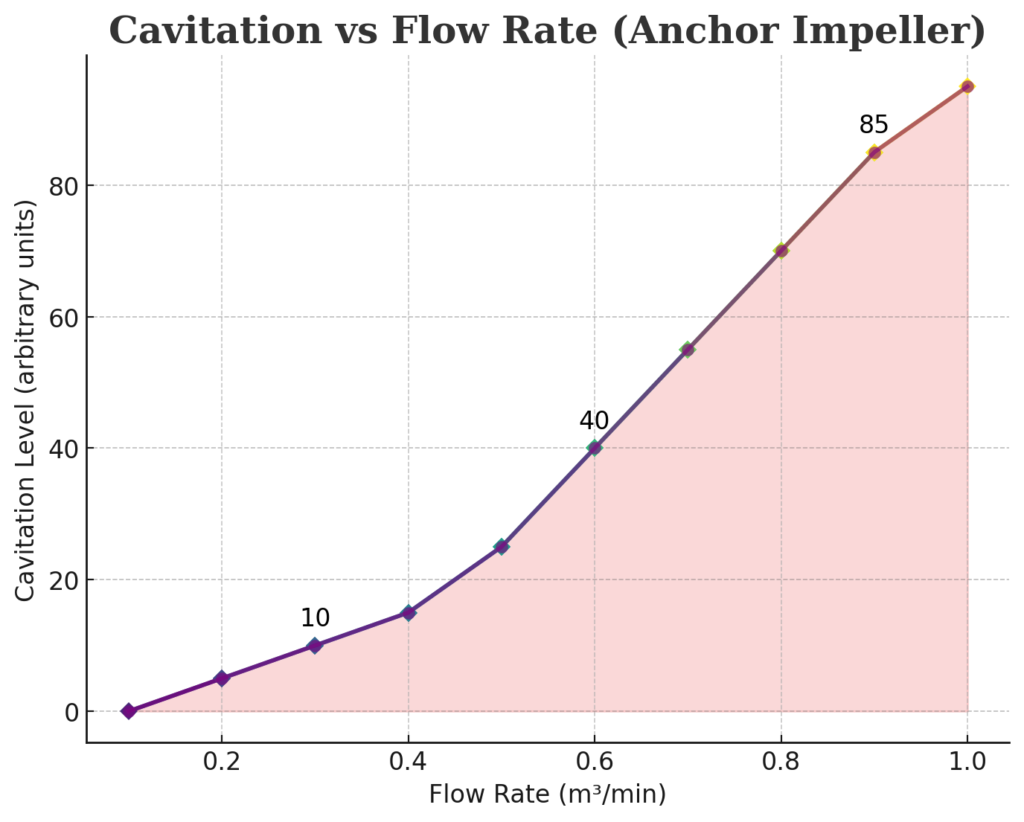

This chart clearly shows how excessive flow rates can trigger vapor bubble formation, leading to mechanical stress and reduced impeller lifespan. SV Industries combats this challenge through precision-engineered blade designs that promote even flow distribution and reduce low-pressure pockets where cavitation typically occurs. When you choose our Anchor Impeller, you invest in a mixing system that runs quietly, efficiently, and reliably — even under dynamic flow conditions.
📌 For impellers designed to reduce cavitation in critical chemical or pharmaceutical applications, check out our Chemical Process Reactor Systems and SS Jacketed Vessels.
📊 Efficiency vs Flow Rate Chart Of Anchor Impeller
The balance between Efficiency and Flow Rate is critical for achieving optimal mixing performance without overloading your system. The chart below showcases how flow rate adjustments impact the overall efficiency of your Anchor Impeller. As flow rate increases, efficiency tends to fluctuate — and finding the sweet spot is essential for maximizing both energy output and fluid movement. SV Industries’ designs focus on maintaining high performance across a wide range of flow rates, ensuring you get the best of both worlds: maximum efficiency and cost savings.

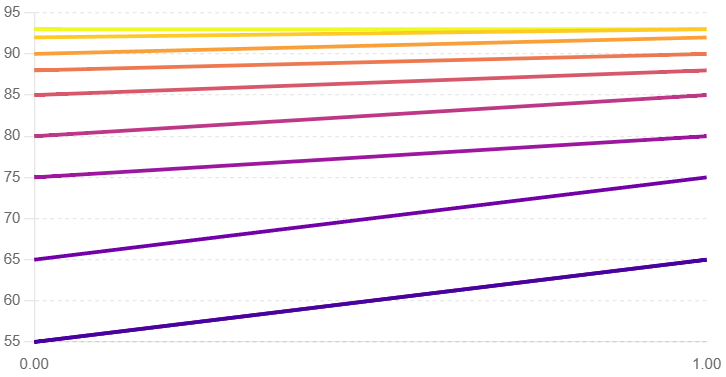
The chart illustrates that moderate flow rates yield the best efficiency, while excessively high flow rates can lead to a drop in mixing efficiency due to higher power consumption and potential system strain. At SV Industries, our Anchor Impellers are specifically engineered to maintain steady, efficient operation across varying flow conditions. By optimizing impeller geometry and blade design, we reduce energy consumption while maintaining the required flow dynamics for effective mixing — no matter the scale of the application.
📈 For more on how our impellers help balance flow and efficiency, visit our Agitator Range and Hydrofoil Impellers.
Anchor vs Other Impellers – Performance Comparison
When selecting the ideal industrial agitator, choosing the right impeller type is crucial. Anchor Impellers are known for their performance with high-viscosity fluids, but how do they stack up against other designs like Pitched Blade Turbine or Rushton Turbine?
Use the comparison below to understand the strengths and limitations of each impeller type, and determine the most suitable choice for your mixing process.
📊 Performance Comparison Chart – Anchor vs Other Impellers
When comparing different industrial impellers, it’s important to evaluate performance factors like fluid handling capacity, energy efficiency, and mixing action. This comparison helps you decide which type is best suited for your specific application.
At SV Industries, we provide a range of impellers including Anchor, Pitched Blade Turbine, and Rushton Turbine — each designed to meet unique process requirements. The chart below presents a detailed side-by-side performance comparison to help you choose wisely.
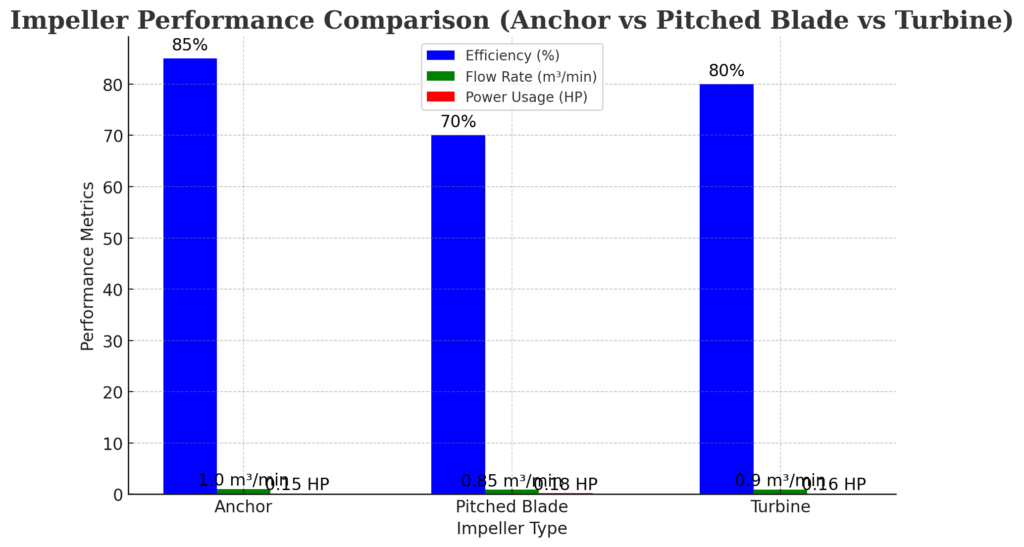
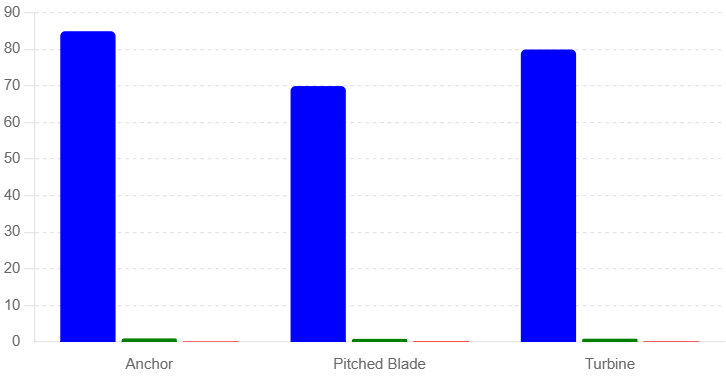
As shown in the chart, Anchor Impellers excel in handling high-viscosity materials and are ideal for slow-speed, wall-scraping mixing. In contrast, Pitched Blade Turbines offer versatile performance across moderate viscosities, while Rushton Turbines are preferred for gas-liquid dispersion.
For a custom agitator solution that matches your exact process parameters, get in touch with our expert team or explore our full impeller range.
Feature | Anchor Impeller | Pitched Blade Turbine | Rushton Turbine |
---|---|---|---|
Viscosity Range | High (2,000 – 100,000+ cP) | Medium (500 – 5,000 cP) | Low to Medium (100 – 3,000 cP) |
Flow Pattern | Laminar, wall-sweeping | Radial + axial | Radial only |
Application | Creams, pastes, heavy slurry | Emulsions, liquids with solids | Fermentation, gas dispersion |
Energy Efficiency | Moderate | High | Moderate |
Scalability | Excellent for large tanks | Good | Moderate |
💡 Need Help Choosing the Right Impeller?
Still confused between Anchor, Paddle, or Turbine-type impellers? Visit our detailed Agitator Page or contact our engineers to get a tailored solution.
Benefits of SV Industries’ Anchor Impeller Design
When it comes to industrial-scale mixing, choosing the right impeller isn’t just about movement — it’s about precision, consistency, and process efficiency. SV Industries’ Anchor Impeller design is thoughtfully engineered to deliver these exact results, especially for viscous fluids and sensitive materials. Here’s why it’s the preferred choice across industries:
🔄 Low Shear Mixing
Ideal for applications where gentle agitation is crucial. It protects shear-sensitive compounds like emulsions, polymers, and biological solutions from degradation.
🧊 No Dead Zones
The sweeping blade profile ensures complete tank coverage, preventing sediment buildup and ensuring uniform product consistency throughout the vessel.
⚡ Energy Efficient
Designed to deliver maximum fluid movement with minimal power consumption — resulting in reduced operational costs and enhanced process sustainability.
🛠️ Customizable Mounting
Available in top, bottom, and side-mount configurations to suit various tank geometries and process requirements. We offer both standard and fully custom options.
🧴 Efficient Mixing of High-Viscosity Fluids
Handles materials like gels, slurries, resins, and adhesives with ease. The impeller’s geometry is optimized for high torque transfer, ensuring proper movement in thick fluids.
🌬️ Minimal Shear Force
Maintains the integrity of shear-sensitive ingredients — making it ideal for pharmaceutical, cosmetic, and food-grade applications.
💸 Cost-Effective Operation
Long-lasting materials, low power needs, and minimal downtime result in a superior return on investment (ROI).
🔧 Reduced Maintenance
Fewer moving parts, corrosion-resistant construction, and optimized shaft alignment reduce wear and tear — minimizing unplanned maintenance and extending equipment life.
📌 Pair the Anchor Impeller with our Limpet Coil Reactor Vessel or SS Jacketed Vessel for a complete, efficient processing solution.
For even more options in fluid mixing technology, explore the Pitch Blade Turbine and Paddle Impeller models.
Anchor Impeller Manufacturer and Suppliers in India
When it comes to industrial mixing excellence, partnering with the right Anchor Impeller manufacturer or supplier in India can define your process success. From custom engineering to timely delivery and post-sales support, the quality and reliability of your vendor matters.
At SV Industries, we take pride in being among the best Anchor Impeller manufacturers in India, offering precision-built agitators that meet global standards.
🔧 Role of Manufacturers
Manufacturers like SV Industries play a crucial role in designing, engineering, and producing Anchor Impellers tailored for specific process applications. Their responsibilities include:
Ensuring high-quality fabrication using stainless steel or exotic alloys
Delivering customized impeller designs for different viscosity levels and tank geometries
Maintaining strict QC checks to meet industry-specific norms like GMP or ASME
Providing R&D-backed innovations, like CFD-tested impeller blade profiles
Looking for precision-built designs? Explore our Agitator Manufacturing Capabilities in Gujarat.
📦 Responsibilities of Suppliers
Suppliers, whether local or national, serve as a vital bridge between manufacturers and end-users. Trusted suppliers:
Ensure on-time delivery and logistics coordination across India
Offer installation support, commissioning, and technical assistance
Maintain inventory and spare parts for faster service and maintenance
Act as your go-to contact for replacements, upgrades, and cross-product consultation
SV Industries supports both direct sales and distributor-based supply chains, ensuring nationwide availability of Anchor Impellers and other mixing equipment.
🧠 Tips to Choose the Right Vendor
Whether you’re in Ahmedabad, Mumbai, or anywhere across India, keep these tips in mind before finalizing your impeller vendor:
✅ Check if the vendor is also a manufacturer with in-house design and production
✅ Ask for past client references and customization options
✅ Verify their technical support and installation expertise
✅ Confirm that they offer after-sales service, warranty, and part availability
✅ Look for vendors with digital presence and detailed product info (like SV Industries)
Choosing the right Anchor Impeller supplier means better performance, lower downtime, and a stronger ROI on your mixing system.
Why SV Industries is India’s Trusted Anchor Impeller Manufacturer
SV Industries, based in Ahmedabad, Gujarat, has firmly established itself as a leading manufacturer and supplier of anchor impellers. Over the years, we have gained a reputation for producing high-quality, durable, and efficient industrial impellers that cater to the diverse needs of industries across India and beyond. Our anchor impellers are designed with cutting-edge technology and precision to meet the demands of high-viscosity fluid processing, offering both performance and reliability.
Anchor impellers are a vital component in various industries where mixing or agitating thick, viscous, or dense liquids is essential. From chemical processing to pharmaceutical production, food & beverage manufacturing, paint industries, and cosmetic production, SV Industries’ anchor impellers play a crucial role in ensuring that these processes are efficient, consistent, and energy-saving. Our impellers are tailored to ensure that the thick liquids, pastes, slurries, and creams are uniformly mixed, preventing clumping and ensuring that the final product has the right consistency.
One of the primary reasons why SV Industries has earned the trust of its clients is our unwavering commitment to quality and innovation. We understand that each industrial application is unique, which is why we offer customized anchor impellers that meet specific client requirements. We work closely with our customers to comprehend their operational needs and design impellers that deliver optimal results. Our anchor impellers are engineered for low-speed operation, which helps minimize power consumption while delivering high-efficiency mixing. This energy-saving feature makes them highly sought after in industries looking to reduce operational costs.
At SV Industries, we use only the highest-quality materials in the manufacturing of our anchor impellers. This includes stainless steel and other corrosion-resistant alloys that ensure durability and long-lasting performance, even in harsh industrial environments. Our impellers are built to withstand the rigors of continuous use, ensuring that they provide consistent performance over time, reducing the need for frequent maintenance or replacements. This durability is key to lowering long-term operational costs, providing our clients with a cost-effective solution that doesn’t compromise on performance.
We take pride in offering an expansive range of anchor impellers designed to handle varying tank sizes, fluid types, and viscosities. Each impeller is designed to perform efficiently in large industrial tanks, where high volumes of thick materials need to be continuously mixed. The flat blades of the anchor impeller make it ideal for scraping the walls of the tank, preventing buildup and ensuring that the mixing process is uniform throughout the tank. This results in more effective mixing, better product consistency, and reduced processing times.
Our supply network is vast, covering Gujarat, Rajasthan, Maharashtra, Madhya Pradesh (MP), Uttar Pradesh (UP), Bihar, and other parts of India, enabling us to provide timely and efficient delivery to clients across the country. We also ensure that all our products adhere to stringent quality control standards, ensuring that every anchor impeller leaving our facility is ready to perform under the toughest conditions.
Choosing SV Industries for your anchor impeller needs means opting for a partner who values innovation, quality, and customer satisfaction. Our commitment to sustainable practices, energy efficiency, and performance-driven solutions makes us a trusted choice in the industry. Our focus on continuous improvement and client-centric services ensures that we meet the ever-evolving demands of industries and provide our customers with the best possible solutions for their mixing and agitation needs. Whether you need a custom solution or a standard impeller, SV Industries is your go-to provider for all your anchor impeller requirements.
Frequently Asked Questions (FAQs) – Anchor Impeller
What is the primary function of an anchor impeller?
Anchor impellers are designed to efficiently mix and agitate high-viscosity liquids in industrial processes, making them ideal for thick fluids, slurries, and pastes.
How does an anchor impeller work?
The anchor impeller’s large, flat blades scrape the tank walls while rotating, ensuring efficient mixing and uniform distribution of viscous fluids.
What industries use anchor impellers?
Anchor impellers are commonly used in chemical processing, pharmaceuticals, food & beverage, cosmetics, paint manufacturing, and water treatment.
What makes SV Industries’ anchor impellers different?
SV Industries’ anchor impellers are built with high-quality materials for durability, customized designs to meet specific needs, and energy-efficient operation for reduced power consumption.
Can anchor impellers be used for both low and high-viscosity fluids?
Anchor impellers are specifically designed for high-viscosity fluids, but they can also handle low-viscosity liquids in some cases, depending on the application.
How do anchor impellers reduce energy consumption?
The anchor impeller operates at lower speeds, which reduces the energy needed to mix thick fluids compared to higher-speed impellers.
Are SV Industries’ anchor impellers customizable?
Yes, SV Industries offers custom anchor impellers tailored to your specific mixing needs, including size, blade configuration, and materials.
What materials are SV Industries’ anchor impellers made of?
Our anchor impellers are made from stainless steel and other corrosion-resistant alloys, ensuring durability and resistance to harsh chemicals and high-viscosity materials.
What is the lifespan of an anchor impeller?
SV Industries’ anchor impellers are built to last for many years with proper maintenance, offering long-term durability and reliability.
How can I order an anchor impeller from SV Industries?
You can contact us through our website or call us directly for inquiries and to place an order. Our team will guide you through the process.
Get a Custom Anchor Impeller Quote Today!
Looking for a custom-engineered Anchor Impeller that meets your exact process needs? Whether you require a low-shear mixer for high-viscosity fluids or an energy-efficient agitator for your reactor vessel, SV Industries delivers precision-built solutions backed by expert support.
We manufacture and supply across India – from Ahmedabad to Hyderabad, and from Mumbai to Delhi.
🔧 Ready to take the next step? Get in touch now for pricing, drawings, or a detailed technical consultation.
📦 Bulk orders, OEM partnerships, and urgent deliveries welcome.