Chemical Process Reactor
Your Trusted Manufacturer and Supplier of Chemical Process Reactor
A Chemical Process Reactor is a vessel used in industrial settings to carry out chemical reactions. It provides a controlled environment where reactants are mixed under specific conditions, such as temperature, pressure, and agitation, to produce desired products. These reactors are crucial in various industries, including chemical manufacturing, pharmaceutical production, and petrochemical refining.
The primary function of a Chemical Process Reactor is to ensure that the chemical reaction takes place efficiently and safely. The reactor’s design allows for precise control over factors like mixing speed, heat transfer, and pressure, which directly influence the rate and outcome of the chemical process. Common types of Chemical Process Reactors include batch reactors, continuous reactors, and stirred-tank reactors, each designed for specific types of chemical processes.
Chemical Process Reactors are built using materials that can withstand the harsh conditions of chemical reactions, such as high temperatures and corrosive substances. The material choice ensures the reactor’s durability and safety. For industries requiring continuous production, chemical process reactors provide a steady flow of reactants and products, improving operational efficiency.
These reactors are designed not just for functionality but also for energy efficiency, helping businesses reduce operational costs while maintaining product quality. As technology advances, modern Chemical Process Reactors incorporate automation and safety features, ensuring that the entire reaction process is as controlled and optimized as possible. Whether for small-scale production or large industrial processes, a Chemical Process Reactor is essential for transforming raw materials into valuable chemical products.
What is a Chemical Process Reactor?
A Chemical Process Reactor is a vessel that facilitates a chemical reaction between reactants under controlled conditions. These reactors are used to control the reaction environment, such as temperature, pressure, and mixing, to achieve the desired product. The design of a Chemical Process Reactor includes mechanisms for heat exchange, stirring, and sometimes, the addition of external reagents or catalysts to enhance the reaction.
The design and type of reactor used can vary based on the process, such as batch or continuous, and whether the reaction is exothermic (releases heat) or endothermic (absorbs heat). The materials of construction and the reactor’s configuration are crucial for ensuring that the reactor can handle the specific chemicals involved and meet safety and regulatory standards.
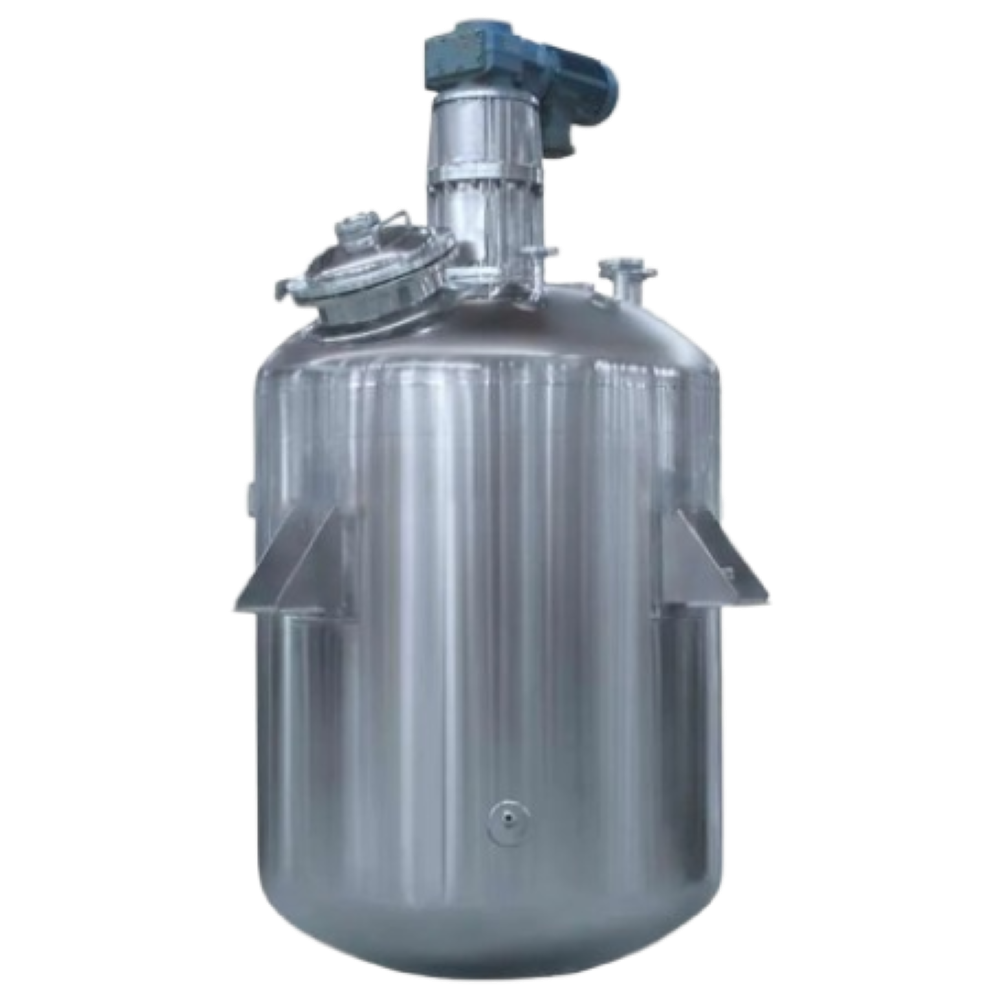
How Chemical Process Reactor Work?
A Chemical Process Reactor works by providing a controlled environment where chemical reactions can occur efficiently and safely. The reactor is designed to manage key factors such as temperature, pressure, and mixing, which directly influence the rate and outcome of the chemical reaction.
In a Chemical Process Reactor, reactants are introduced into the vessel, and the desired reaction takes place. The reactor’s design typically includes components like a stirring mechanism or agitator, which ensures proper mixing of the reactants. This mixing is crucial for maintaining uniform temperature and concentration throughout the process, ensuring that the chemical reaction proceeds at a consistent rate.
Temperature control is another vital aspect of how a Chemical Process Reactor works. Most reactions either release or absorb heat, so the reactor is equipped with heat exchange systems that help regulate the temperature within an optimal range. This can be achieved through external heating or cooling systems integrated into the reactor.
Pressure is another factor controlled within the reactor. Many chemical reactions require specific pressure conditions to occur, and the reactor is designed to withstand and maintain these conditions. Some reactors may include pressure relief systems to prevent accidents caused by overpressure.
In modern Chemical Process Reactors, automation and monitoring systems are often included to ensure precision and efficiency. These systems continuously monitor variables like temperature, pressure, and reaction time, adjusting as needed to maintain optimal reaction conditions. Ultimately, the Chemical Process Reactor ensures that chemical reactions are carried out safely, efficiently, and consistently.
Customization Options
Material Selection
Importance
The material used in the construction of a Chemical Process Reactor is crucial to its durability and safety. Different chemical processes involve different reactants, some of which may be highly corrosive or abrasive.
Customization
Materials such as stainless steel, alloy steels, carbon steel, and specialized corrosion-resistant alloys (e.g., Hastelloy, Titanium) are selected based on the chemical properties of the reactants, the operating temperature, and pressure. For instance, reactors used in acidic environments may require materials that can withstand corrosion, while those used in high-temperature reactions may require heat-resistant alloys.
Benefits
Customizing the material selection ensures the longevity of the reactor and reduces the risk of material degradation, which could compromise the safety and efficiency of the process.
Reactor Design
Importance
The design of a Chemical Process Reactor depends on the type of chemical process being carried out. Different reactions require different mixing, flow patterns, and vessel geometries.
Customization
Reactor designs can be tailored to suit various processes such as batch, continuous, or semi-batch reactions. For example:
Batch Reactors: Typically used for small quantities and processes requiring flexibility.
Continuous Reactors: Designed for large-scale, continuous production with a steady flow of reactants.
Stirred Tank Reactors: Often used for both batch and continuous processes, incorporating a mechanical agitator for efficient mixing.
Benefits
Customizing the reactor design ensures that the process runs smoothly with optimal reaction conditions, improving efficiency and safety.
Temperature and Pressure Control Systems
Importance
Many chemical reactions are highly sensitive to temperature and pressure. Managing these factors effectively is essential for achieving the desired reaction rate and product quality.
Customization
Chemical Process Reactors can be equipped with advanced temperature control systems, such as external heat exchangers, electric heating jackets, or cooling coils, to regulate temperature. Additionally, pressure control systems, such as pressure relief valves and pressure sensors, can be customized to ensure the reactor maintains the required pressure throughout the process.
Benefits
Customizing the temperature and pressure systems helps in maintaining optimal conditions, which can increase reaction efficiency, reduce energy consumption, and ensure safety during high-pressure or high-temperature processes.
Agitation and Mixing Systems
Importance
Proper mixing and agitation are critical to ensure that the reactants are evenly distributed throughout the reactor. Uneven mixing can result in incomplete reactions and low-quality products.
Customization
The agitation system in a Chemical Process Reactor can be customized based on the type of reaction and the viscosity of the reactants. Options include:
Mechanical Agitators: For efficient mixing of liquids or slurries.
Air or Gas-Lift Agitation: Used in reactions where aeration is required.
Magnetic Stirring: Often used in laboratory-scale reactors.
Benefits
Customizing the agitation system ensures uniform mixing, improving reaction efficiency and product consistency. It also prevents issues such as settling or clumping of reactants, which can disrupt the process.
Applications of Chemical Process Reactors
Chemical process reactors are crucial in many industries for carrying out chemical reactions under controlled conditions. These reactors provide the necessary environment to transform raw materials into valuable products, ensuring efficiency, safety, and consistency. Below are some key applications of chemical process reactors across various industries:
Petrochemical Industry
Application
In the petrochemical industry, chemical process reactors are used for refining crude oil and producing essential chemicals like gasoline, diesel, ethylene, and plastics. For example, cracking reactors break down large hydrocarbon molecules into smaller, more useful molecules.
Purpose
To produce fuels, chemicals, and plastics from hydrocarbons, which are integral to energy production and material manufacturing.
Pharmaceutical Industry
Application
Chemical process reactors are widely used in the pharmaceutical industry for the synthesis of active pharmaceutical ingredients (APIs) like antibiotics, vaccines, and other therapeutic compounds.
Purpose
To produce high-quality medicines in a controlled environment, ensuring consistency, purity, and compliance with stringent health standards.
Food and Beverage Industry
Application
Chemical process reactors are used to produce food additives, preservatives, flavorings, and in fermentation processes like brewing beer, making vinegar, or fermenting dairy products.
Purpose
To create ingredients and products with enhanced flavors, longer shelf life, and nutritional value, while maintaining safety standards for consumables.
Agrochemical Industry
Application
In the agrochemical industry, chemical process reactors are used to produce pesticides, herbicides, fungicides, and fertilizers. These reactors are essential for synthesizing chemicals that protect crops and increase agricultural yields.
Purpose
To enhance crop protection and increase food production efficiency by producing agrochemicals that prevent pests, weeds, and diseases.
Polymer and Plastic Manufacturing
Application
Chemical process reactors are crucial for the polymerization process used to create plastics and polymers like polyethylene, polypropylene, and polystyrene.
Purpose
To produce high-quality plastics used in a wide range of products, including packaging materials, automotive components, and consumer goods.
Fine Chemicals and Specialty Chemicals
Application
Chemical process reactors are used in the production of fine chemicals such as dyes, fragrances, and specialty chemicals like lubricants, coatings, and detergents.
Purpose
To create high-value chemicals with specific properties that are used in niche markets, contributing to industries like textiles, cosmetics, and cleaning products.
Biofuels and Renewable Energy
Application
In the biofuel industry, chemical process reactors are used to convert organic materials (such as vegetable oils or biomass) into biofuels like biodiesel or bioethanol through processes like transesterification and fermentation.
Purpose
To produce sustainable and eco-friendly fuel alternatives, reducing reliance on fossil fuels and promoting renewable energy sources.
Environmental and Waste Treatment
Application
Chemical process reactors are employed in wastewater treatment and other environmental applications. They are used to neutralize harmful chemicals or to treat industrial waste by-products through oxidation or biodegradation processes.
Purpose
To reduce the environmental impact of industrial processes and ensure the safe disposal or recycling of chemical waste, helping companies comply with environmental regulations.
Metal and Alloy Production
Application
Chemical process reactors are also used in the production of metal alloys, where chemicals react with metals to improve properties like strength, corrosion resistance, and durability.
Purpose
To create high-performance materials used in industries like aerospace, automotive, and construction.
Textile Industry
Application
Chemical process reactors are used in the textile industry for dyeing, bleaching, and finishing fabrics. These reactors help mix dyes, chemicals, and fabrics under controlled conditions to achieve uniform color and texture.
Purpose
To enhance the appearance, durability, and performance of textiles, ensuring high-quality finished products for consumer markets.
Chemical process reactors are essential across various industries, helping transform raw materials into finished products through controlled chemical reactions. Whether in the production of energy, pharmaceuticals, food, agrochemicals, or specialty materials, chemical process reactors ensure that these transformations occur efficiently, safely, and consistently. The versatility of chemical process reactors makes them an integral part of industrial processes, driving innovation and sustainability in many sectors.
SV Industries: Chemical Process Reactor Manufacturer
SV Industries, based in Ahmedabad, is a leading Chemical Process Reactor manufacturer, specializing in providing high-quality, customized reactors for a variety of industries. With a strong focus on innovation, safety, and precision, SV Industries has built a reputation for delivering superior Chemical Process Reactors that cater to the unique needs of each client.
Customization and Tailored Solutions
At SV Industries, every Chemical Process Reactor is designed and manufactured with the client’s specific requirements in mind. The company offers full customization in terms of material selection, reactor design, temperature control, pressure systems, and mixing mechanisms. This personalized approach ensures that each reactor is optimized for the client’s particular process, enhancing both efficiency and safety.
Advanced Manufacturing Techniques
SV Industries uses advanced manufacturing techniques to ensure that each Chemical Process Reactor is produced to the highest standards. Their team of skilled engineers and technicians employs state-of-the-art tools and technologies, including precision welding and machining, to create reactors that meet stringent quality and safety standards.
Energy Efficiency and Safety
SV Industries focuses on creating Chemical Process Reactors that not only meet operational demands but also contribute to energy efficiency and safety. Their reactors come equipped with the latest safety features, such as pressure relief valves, automated monitoring systems, and high-quality insulation, all designed to reduce energy consumption and ensure safe operation during chemical reactions.
Cost-Effective Solutions
SV Industries understands the importance of cost-efficiency in industrial processes. By optimizing manufacturing techniques, utilizing bulk material procurement, and leveraging strong supplier relationships, the company offers highly competitive pricing for their Chemical Process Reactors without compromising on quality. This ensures that businesses can achieve high performance while staying within budget.
Timely Delivery and After-Sales Support
SV Industries is committed to delivering Chemical Process Reactors within the agreed time frame. Their efficient production processes and logistics systems ensure that reactors are delivered on schedule. Additionally, SV Industries provides comprehensive after-sales support, including installation, maintenance, and troubleshooting services, to ensure that the reactors operate smoothly throughout their lifespan.
By choosing SV Industries as a Chemical Process Reactor Manufacturer, industries gain access to cutting-edge technology, unmatched expertise, and a commitment to delivering the most reliable and efficient reactors for their processes. Whether you’re in pharmaceuticals, petrochemicals, or food processing, SV Industries ensures your reactor is optimized for maximum output and minimal environmental impact.
Frequently Asked Questions (FAQs)
What is a Chemical Process Reactor?
A Chemical Process Reactor is a vessel used to facilitate chemical reactions under controlled conditions. It regulates factors such as temperature, pressure, and mixing to ensure that the reaction happens efficiently and safely, producing the desired chemical products.
How do Chemical Process Reactors work?
A Chemical Process Reactor works by mixing reactants under controlled conditions (temperature, pressure, and agitation) to promote the chemical reaction. The reactor typically includes components like heat exchangers, agitators, and pressure relief systems to maintain optimal reaction conditions.
What industries use Chemical Process Reactors?
Chemical Process Reactors are used in various industries, including pharmaceuticals, petrochemicals, food processing, agrochemicals, and biotechnology, where chemical reactions need to be controlled and monitored for producing specific products.
What are the different types of Chemical Process Reactors?
There are several types of Chemical Process Reactors, including:
- Batch Reactors: For small-scale, flexible production.
- Continuous Reactors: For high-volume, continuous production.
- Stirred Tank Reactors: Often used in both batch and continuous operations for mixing.
- Plug Flow Reactors: For ensuring a consistent residence time for the reactants.
How do I know which Chemical Process Reactor is right for my application?
The right Chemical Process Reactor depends on factors such as the scale of production (batch vs. continuous), reaction type (exothermic or endothermic), and specific requirements like temperature control, pressure, and mixing. Consulting with experts like those at SV Industries can help identify the best reactor for your needs.
What customization options are available for Chemical Process Reactors?
Customization options include:
- Material selection (e.g., stainless steel, titanium, alloys)
- Reactor design (batch, continuous, or stirred tank)
- Temperature and pressure control systems
- Mixing mechanisms (mechanical agitators, air or gas-lift agitation)
- Safety features (pressure relief valves, monitoring systems)
How does SV Industries ensure the quality of its Chemical Process Reactors?
SV Industries follows strict quality assurance processes, including the use of advanced manufacturing techniques, such as precision welding and machining, as well as rigorous testing to meet international standards. They also adhere to certifications like ISO and ASME to ensure the highest quality and safety.
What industries does SV Industries serve with its Chemical Process Reactors?
SV Industries serves industries such as pharmaceuticals, petrochemicals, food processing, agrochemicals, and biotechnology, providing tailored Chemical Process Reactors for each industry’s specific needs.
How can I ensure the safety of a Chemical Process Reactor during operation?
SV Industries incorporates various safety features into its Chemical Process Reactors, including pressure relief valves, temperature control systems, and automated monitoring. Additionally, following proper operational guidelines and regular maintenance can ensure safe operation.
What after-sales support does SV Industries offer for its Chemical Process Reactors?
SV Industries provides comprehensive after-sales support, including:
- Installation services
- Maintenance and troubleshooting
- Technical guidance
- Periodic performance checks to ensure the reactor continues to function optimally.
Why SV Industries Stands Out
In conclusion, Chemical Process Reactors are essential components in various industries that require precise control over chemical reactions. Whether in the pharmaceutical, petrochemical, or food processing sectors, these reactors play a critical role in ensuring efficiency, safety, and product quality. SV Industries stands out as a leader in Chemical Process Reactor manufacturing, offering customized, high-quality solutions that cater to the unique needs of each industry.
With a focus on advanced manufacturing techniques, energy efficiency, safety features, and cost-effective pricing, SV Industries provides reliable reactors that help businesses optimize their operations. Their commitment to innovation and customer satisfaction ensures that clients receive tailored reactors that enhance process efficiency, reduce costs, and maintain high standards of safety.
If you’re looking for a trusted partner to meet your Chemical Process Reactor needs, SV Industries offers the expertise, customization options, and comprehensive after-sales support that can take your chemical processes to the next level. With their focus on quality, safety, and performance, SV Industries is the ideal choice for businesses seeking to maximize their production efficiency and minimize operational risks.