SV Industries: Trusted Manufacturer & Supplier of Hydrofoil Impeller in India
At SV Industries, we take pride in being one of the most trusted manufacturers and suppliers of Hydrofoil Impellers in India. With years of experience and a strong foothold in the industrial mixing and agitation sector, we specialize in delivering high-performance, energy-efficient Hydrofoil Impellers designed for optimized fluid dynamics in various industrial applications.
Our commitment to quality engineering, customized solutions, and on-time delivery has earned us the trust of clients across chemical, pharmaceutical, food processing, and water treatment industries. As a leading Agitator Manufacturer in Gujarat, our goal is to provide you with equipment that boosts productivity and process consistency.
Explore our wide range of advanced impeller designs including the Paddle Impeller, Helical Impeller, and Anchor Impeller — all built to handle your unique mixing challenges with precision.
Choose SV Industries — where innovation meets reliability.
What is a Hydrofoil Impeller and Why is It Used in Industrial Mixing?
❓ What is a Hydrofoil Impeller?
A Hydrofoil Impeller is a type of mixing blade with aerodynamically curved blades designed to minimize drag and maximize fluid flow. It promotes axial flow (top-to-bottom movement) in the mixing tank, allowing for faster blending, better suspension of solids, and more efficient mass and heat transfer.
❓ Why is a Hydrofoil Impeller Used in Industrial Mixing?
Hydrofoil Impellers are preferred in industries because they:
Consume less energy while delivering high flow output
Are ideal for large tanks and low-viscosity fluids
Generate low shear, making them suitable for sensitive products
Improve mixing efficiency in processes like chemical processing, water treatment, and pharmaceutical blending
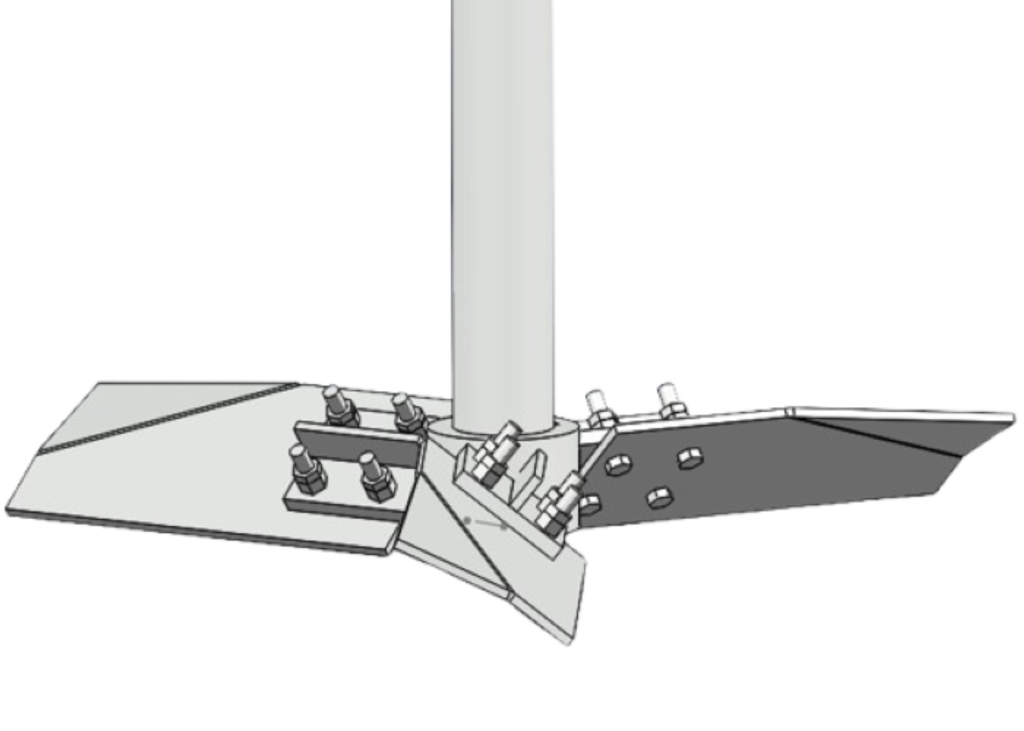
How Does a Hydrofoil Impeller Work?
A Hydrofoil Impeller works by generating a smooth axial flow pattern—meaning it pushes fluid from the top to the bottom of the tank. This flow ensures uniform mixing, better solid suspension, and efficient blending of low to medium viscosity fluids.
The impeller’s foil-shaped blades are specifically designed to:
Minimize drag and reduce energy consumption
Create high flow rates with low shear, preserving product quality
Enable fast mixing even in large-volume tanks
As the impeller rotates, it creates a vortex-free circulation that keeps solids suspended and enhances mass and heat transfer.
💡 Compared to traditional impellers like the Anchor Impeller or Paddle Impeller, hydrofoil blades are more energy-efficient, especially in continuous mixing operations.
Hydrofoil Impeller Design Parameters and Operating Characteristics
Hydrofoil impellers are engineered for maximum efficiency with minimal power input. Their unique blade geometry, pitch angle, and surface finish significantly affect the fluid flow pattern, energy transfer, and overall process results. Understanding the core design parameters and how they influence operating performance is critical for selecting the right impeller for your application.
🔧 Key Hydrofoil Impeller Design Parameters:
Blade Angle & Pitch: Optimized to reduce turbulence while maximizing flow
Impeller Diameter: Directly impacts flow rate and energy distribution
Blade Width & Solidity: Affects the flow profile and power number
Number of Blades: Typically 3 or 4, depending on viscosity and tank design
Clearance & Mounting Height: Influences flow pattern (axial vs radial)
Surface Finish: Critical for GMP applications in pharma & food industries
⚙️ Operating Characteristics:
High Flow, Low Shear: Ideal for gentle yet effective mixing
Low Power Consumption: Energy-efficient compared to traditional impellers
Stable Axial Flow: Promotes uniform mixing and reduces vortexing
Scalable Performance: Designs can be customized for lab, pilot, and production scales
These characteristics make hydrofoil impellers suitable for a wide range of fluid viscosities and tank geometries, particularly where energy savings and clean mixing are priorities.
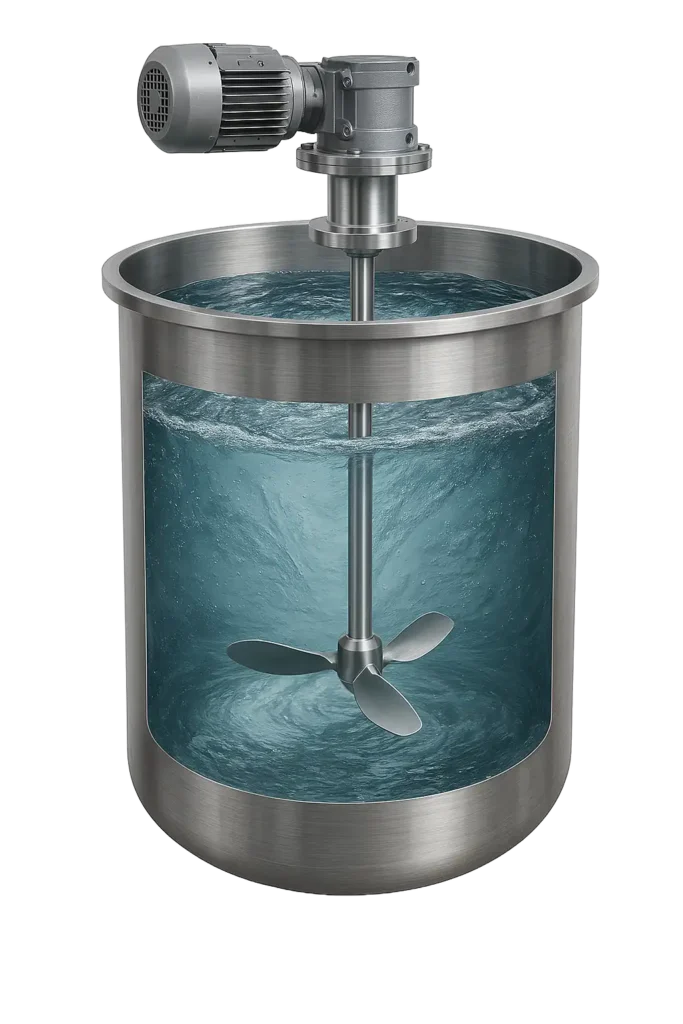
📊 Hydrofoil Impeller Power Consumption vs Flow Rate Chart
In industrial mixing, power efficiency is just as important as performance. This Power Consumption vs Flow Rate Chart illustrates how Hydrofoil Impellers maintain high flow rates with minimal energy usage. By comparing flow output to power input, engineers can make informed choices to reduce operational costs while ensuring effective blending.
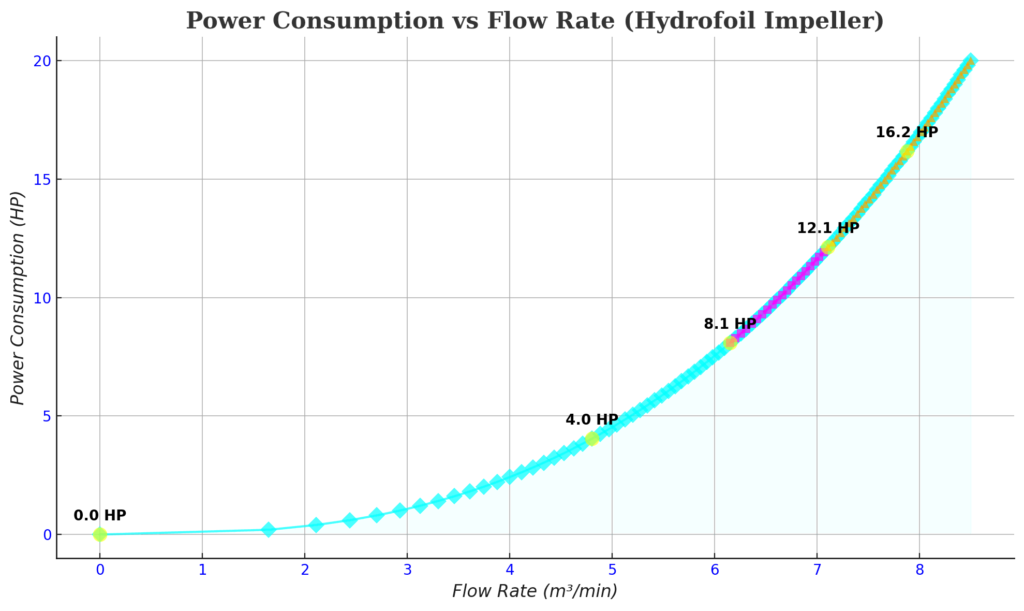

From both versions of the chart, it’s clear that Hydrofoil Impellers offer a power-to-flow ratio that outperforms conventional designs in similar conditions. They’re especially effective in energy-conscious mixing systems, where high throughput and minimal turbulence are essential.
Whether you’re running a continuous agitator setup, batch mixing, or working in power-sensitive environments, this chart reinforces why Hydrofoil Impellers are the preferred choice for modern process plants.
Need help choosing the right configuration? Our expert team at SV Industries Agitators Division is here to guide you.
📊 Hydrofoil Impeller Flow Rate vs Impeller Diameter Chart
Accurate selection of impeller diameter is critical for achieving the desired flow rate in any industrial mixing system. The following Flow Rate vs Impeller Diameter Chart helps in determining the best size of Hydrofoil Impeller based on the required mixing volume and fluid dynamics. This visual guide enables process engineers to optimize design decisions for maximum efficiency and minimal energy consumption.
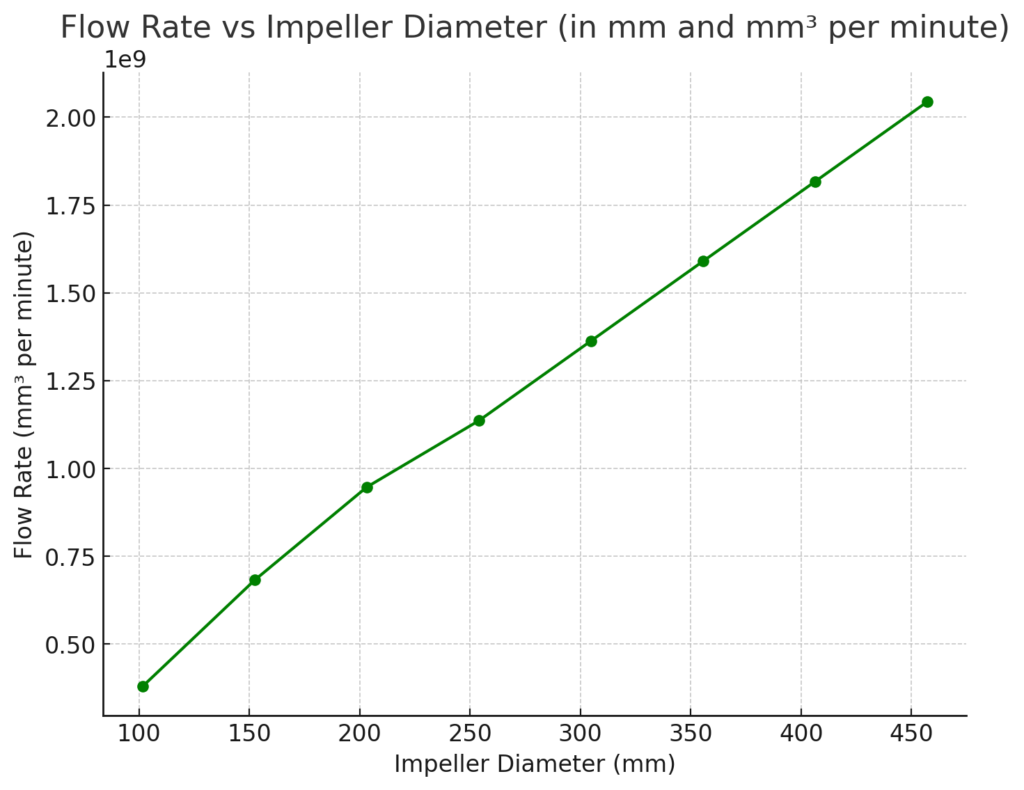
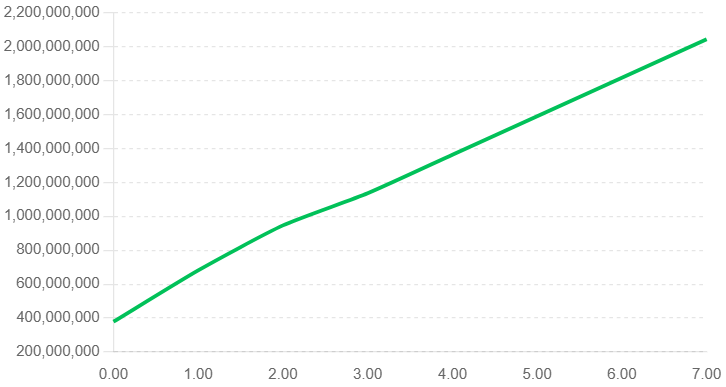
From both charts, it is evident that impeller diameter plays a direct role in determining the volumetric flow rate inside mixing tanks. Larger diameters result in higher axial flow, ideal for bulk liquid blending, while smaller diameters suit low-viscosity precision applications.
Our Hydrofoil Impellers are custom-sized to ensure optimal process output, low shear, and energy savings across varied mixing conditions. Use these charts as a design reference for your next chemical reactor, biotech mixer, or fermentation system.
📊 Hydrofoil Impeller Pressure Drop vs Flow Rate Chart
Understanding the relationship between flow rate and pressure drop is essential when optimizing Hydrofoil Impeller performance in fluid systems. This Pressure Drop vs Flow Rate Chart helps engineers evaluate how increasing throughput may impact system resistance, especially in closed or semi-closed vessel applications. The data allows for smart pump and impeller configuration, ensuring a perfect balance between efficiency and control.
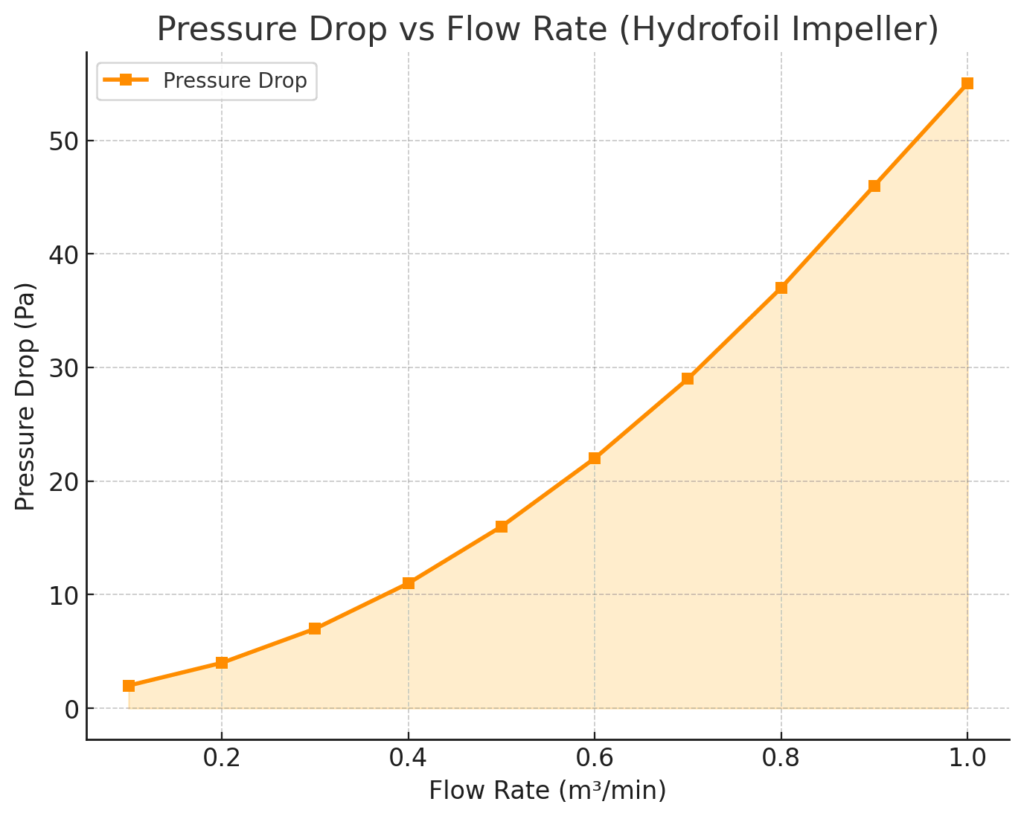
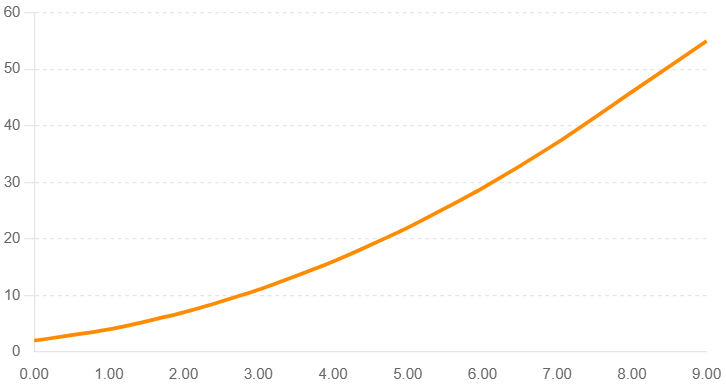
In both charts, it’s clear that as flow rate increases, there is a proportional rise in pressure drop. This information is vital when sizing impellers, selecting pumps, or designing closed system reactors and circulation loops.
For industries using chemical reactors, storage tanks, or multi-phase flow systems, knowing this pressure-flow correlation ensures that energy usage, pump power, and impeller geometry are precisely configured.
Key Features of Hydrofoil Impellers for Efficient Mixing
Hydrofoil Impellers are designed to deliver maximum flow with minimum energy. Their smart engineering makes them the go-to choice for applications requiring gentle, uniform, and efficient mixing.
Here are the standout features that make them ideal for industrial mixing:
✅ Axial Flow Efficiency
Promotes strong top-to-bottom circulation, ensuring complete suspension of solids and faster blending across the tank.
✅ Low Power Consumption
Thanks to their streamlined blade design, Hydrofoil Impellers operate with a lower power number (Np), resulting in reduced energy costs.
✅ Customizable Configurations
Every hydrofoil impeller can be tailored to match specific industrial requirements, from blade angles to materials.
✅ Low Shear Mixing
The hydrofoil impeller ensures gentle mixing, preserving the integrity of sensitive materials like emulsions and suspensions.
✅ Durability
Made from corrosion-resistant materials such as stainless steel, the hydrofoil impeller can withstand harsh industrial environments.
Hydrofoil Impellers from SV Industries are engineered for performance and built to last, ensuring efficient, consistent, and cost-effective mixing in your process.
Types of Hydrofoil Impellers and Their Applications
Hydrofoil impellers may look similar on the surface, but their performance and applications vary significantly based on blade count, blade geometry, and design features. Below are the most common types used across industries:
👉 3-Blade Hydrofoil Impeller
Overview: The most commonly used type. Designed for low-viscosity liquids and gentle yet efficient flow.
Features:
Low power consumption
High flow per unit power
Best For:
✅ Water treatment,
✅ Chemical blending,
✅ Bioreactors in pharma
👉 4-Blade Hydrofoil Impeller
Overview: Offers higher thrust and slightly better mixing for medium-viscosity fluids.
Features:
Improved axial pumping
Balanced flow dynamics
Best For:
✅ Food processing,
✅ Paint and coatings,
✅ Bio-slurry mixing
👉 High Solidity Hydrofoil Impeller
Overview: Designed with wider blades to handle shear-sensitive and high-viscosity materials.
Features:
Ideal for mixing with high solid content
Reduces cavitation in viscous fluids
Best For:
✅ Polymer production,
✅ Sludge digestion,
✅ Cosmetic gels
👉 Custom Hydrofoil Impeller Designs
Overview: Engineered to meet specific tank geometry, fluid dynamics, or clean-in-place (CIP) requirements.
Options:
Foldable blades
Removable hubs
Hybrid blade angles
Best For:
✅ Sterile environments in pharma,
✅ Hazardous chemical mixing,
✅ Energy-efficient retrofits
🧭 Hydrofoil Impeller Type vs Application Type Chart
Application Type | Recommended Hydrofoil Impeller Type |
---|---|
Low-viscosity Liquid Blending | 3-Blade Hydrofoil Impeller |
Medium-viscosity Materials | 4-Blade Hydrofoil Impeller |
High-viscosity or Solids-Heavy Fluids | High Solidity Hydrofoil Impeller |
Custom Mixing Needs / Unique Tank Geometry | Custom Engineered Hydrofoil Impeller |
Applications of Hydrofoil Impellers Across Industries
The versatility of the hydrofoil impeller makes it a preferred choice across various industries:
🧪 Chemical Industry
The hydrofoil impeller is indispensable in chemical manufacturing. It facilitates:
- Mixing of solutions and reagents.
- Homogenization in reactors.
- Applications like neutralization and polymerization.
💧 Water Treatment
In water treatment plants, the hydrofoil impeller ensures uniform mixing during coagulation, flocculation, and aeration processes. Its energy-efficient design makes it a sustainable choice.
💊 Pharmaceutical Industry
Precision is key in pharmaceuticals, and the hydrofoil impeller ensures consistent mixing of ingredients, perfect for creating liquid formulations, suspensions, and ointments.
🍲 Food and Beverage Industry
The hydrofoil impeller plays a vital role in blending syrups, sauces, and beverages, ensuring uniform flavor distribution and product consistency.
🛢️ Petrochemical Sector
In the petrochemical industry, the hydrofoil impeller is used for refining and crude oil blending. Its durability and efficiency make it ideal for handling high-pressure and high-temperature environments.
📊 Application Suitability Chart – Fluid Viscosity vs Hydrofoil Impeller
Understanding the compatibility of impeller types with various fluid viscosities is essential for efficient mixing. This Application Suitability Chart for Hydrofoil Impellers provides a clear visual reference to help engineers and plant managers choose the right mixing solution. Whether you’re working with low-viscosity solvents or moderate-viscosity blends, our Hydrofoil Impeller offers reliable performance with high flow and low shear characteristics.
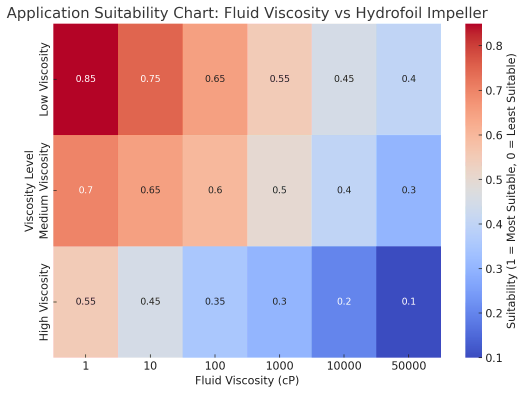
As shown in the chart above, Hydrofoil Impellers perform exceptionally well in low to moderate viscosity fluids, making them ideal for industries such as pharmaceuticals, biotech, food & beverage, and chemical processing. These impellers are engineered to create axial flow patterns, promoting uniform mixing without damaging delicate materials.
For processes involving shear-sensitive materials, our Hydrofoil Impellers offer a perfect blend of gentle flow and energy efficiency. Consult this chart during project planning to ensure maximum productivity and equipment longevity.
Materials Used in Hydrofoil Impeller Manufacturing
Choosing the right material for a hydrofoil impeller is crucial for maximizing performance, ensuring product safety, and extending service life. At SV Industries, we use a range of high-grade, corrosion-resistant materials to meet the demanding needs of various industries.
🛡️ SS316 (Stainless Steel 316)
Why It’s Used: Excellent resistance to corrosion, especially in saline and acidic environments.
Applications: Pharma, chemical processing, food-grade mixing
Advantages:
GMP compliant
Ideal for CIP/SIP systems
🛡️ SS304 (Stainless Steel 304)
Why It’s Used: Cost-effective and corrosion-resistant in mild environments.
Applications: Water treatment, general-purpose mixing
Advantages:
High strength-to-weight ratio
Smooth surface finish for easy cleaning
🛡️ Hastelloy (C-22, C-276)
Why It’s Used: Outstanding resistance to highly aggressive chemicals.
Applications: Acids, oxidizers, extreme pH environments
Advantages:
Maintains integrity under extreme conditions
Long operational life
🛡️ Duplex & Super Duplex Steel
Why It’s Used: Combination of strength and chloride stress corrosion resistance.
Applications: Offshore, wastewater, pulp and paper industries
Advantages:
High mechanical strength
Less prone to pitting or cracking
🧭 Material Type vs Chemical Resistance vs Industry Suitability Chart
Material | Chemical Resistance | Industry Suitability |
---|---|---|
SS316 | High | Pharma, Food, Chemicals |
SS304 | Moderate | Water, Basic Mixing |
Hastelloy C-22 | Very High | Acidic/Corrosive Chemicals |
Super Duplex | High | Offshore, Industrial |
As you can see in the chart above, the choice of material plays a crucial role in the performance, reliability, and compliance of hydrofoil impellers. For industries like pharmaceuticals, food processing, or corrosive chemical mixing, SS316 and Hastelloy C-22 provide excellent corrosion resistance and durability.
On the other hand, SS304 is a cost-effective solution suitable for basic mixing tasks and water-based applications. Super Duplex steel is the go-to choice for heavy-duty applications, especially in offshore or aggressive environments.
Each material has its strengths—selecting the right one can reduce downtime, ensure product purity, and extend the service life of your equipment.
🔧 SV Industries helps you identify the ideal impeller material based on your process needs, operating environment, and industry regulations.
Hydrofoil Impeller Performance Analysis: Flow, Cavitation, and Torque
Understanding the real-world performance of hydrofoil impellers is essential for achieving consistent mixing results, energy savings, and equipment longevity. This section breaks down three critical aspects of hydrofoil performance: flow rate, cavitation risk, and torque behavior.
🧩 Flow Performance: Stable and Predictable
Hydrofoil impellers generate a strong axial flow with minimal turbulence. This results in faster tank turnover and uniform distribution of solids, gases, or liquids—while using less power than traditional agitators. As flow rate increases, the system maintains stability without sudden pressure spikes or dead zones.
For a comprehensive overview of hydrofoil impeller applications and benefits, visit our Hydrofoil Impeller Manufacturer page.
🧪 Cavitation vs Flow Rate: Stay in the Safe Zone
Cavitation occurs when local pressure drops below vapor pressure, causing bubbles that can damage the impeller and tank. Hydrofoil impellers are designed to minimize cavitation, even at higher flow rates. Their thin blades and high-efficiency profiles maintain consistent pressure zones across RPM ranges.
🧠 Engineer’s Insight: Operating slightly below the critical cavitation point can drastically improve equipment lifespan and reduce noise/vibration.
🔄 Torque Analysis: Balancing Load with Efficiency
Torque is a key factor when scaling up mixing systems or running continuous operations. Hydrofoil impellers offer a lower torque-to-flow ratio, meaning they deliver better performance without overloading the motor.
When comparing to traditional anchor or paddle-type impellers, hydrofoil designs require less starting torque and maintain consistent RPM even under load fluctuations.
For insights into anchor impeller designs and their applications, explore our Anchor Impeller Manufacturer page.
These optimized characteristics make hydrofoil impellers ideal for applications that demand scalable flow, reliable torque curves, and cavitation-safe mixing—particularly in pharmaceuticals, specialty chemicals, biotech, and food industries.
📊 Hydrofoil Impeller Cavitation vs Flow Rate Chart
Cavitation can significantly affect the performance and longevity of impellers, especially under high flow or low-pressure conditions. This Cavitation vs Flow Rate Chart illustrates how the risk of cavitation increases with flow rates, providing valuable insight for process engineers designing safe and reliable industrial mixing systems.
Understanding this balance is essential when working with high-speed agitators, where even minor pressure drops can lead to bubble formation and blade erosion.
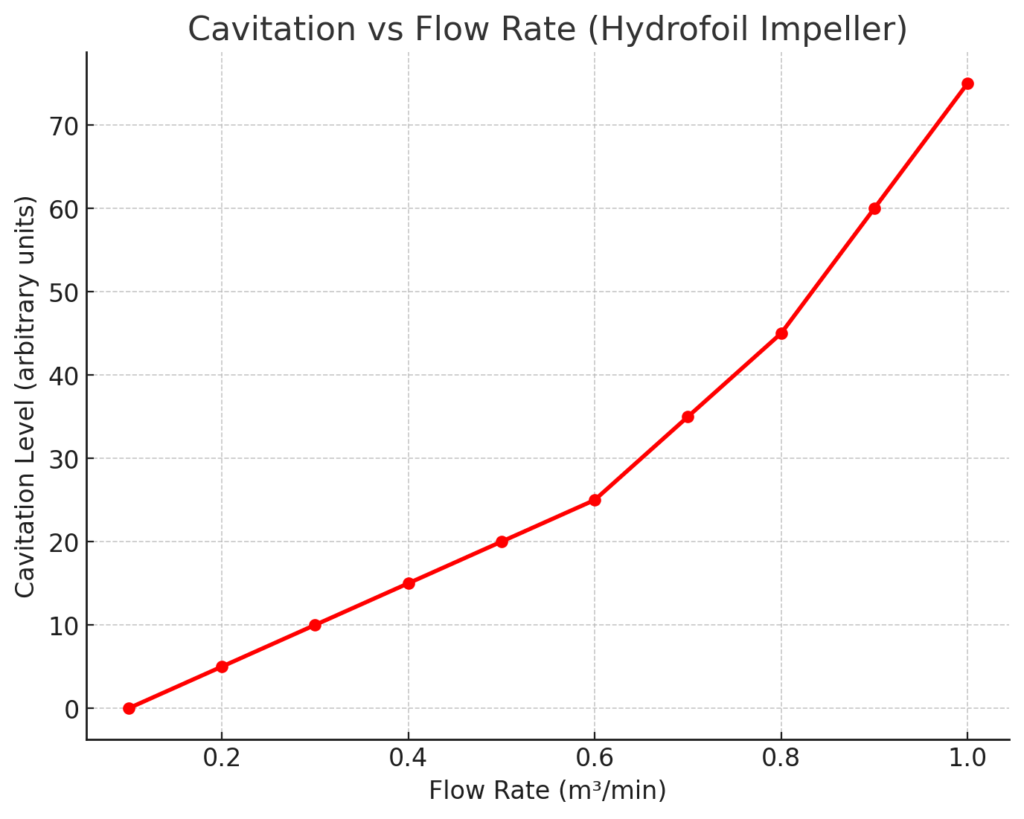
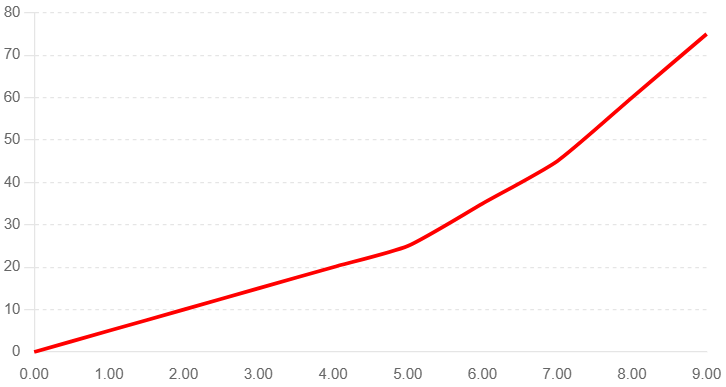
Cavitation is a major concern in high-speed or high-flow mixing applications. These charts help users identify safe flow zones where Hydrofoil Impellers operate without creating vacuum pockets or vapor bubbles, which can lead to vibration, efficiency loss, or surface damage.
When configuring impellers for reactor vessels, closed mixing tanks, or high-viscosity media, use this data to ensure consistent performance and longer equipment life.
To learn more about robust reactor systems that work seamlessly with Hydrofoil Impellers, check out:
👉 SV Industries – Chemical Process Reactor
📊 Hydrofoil Impeller Torque vs RPM for Different Power Values
The Torque vs RPM Chart for different power values is critical when designing and scaling agitator systems using Hydrofoil Impellers. It illustrates how torque changes with varying rotational speeds and power inputs, helping engineers size gearboxes, shafts, and drives precisely.
This chart simplifies mechanical decisions, especially in high-load applications where stability, efficiency, and energy optimization are essential.
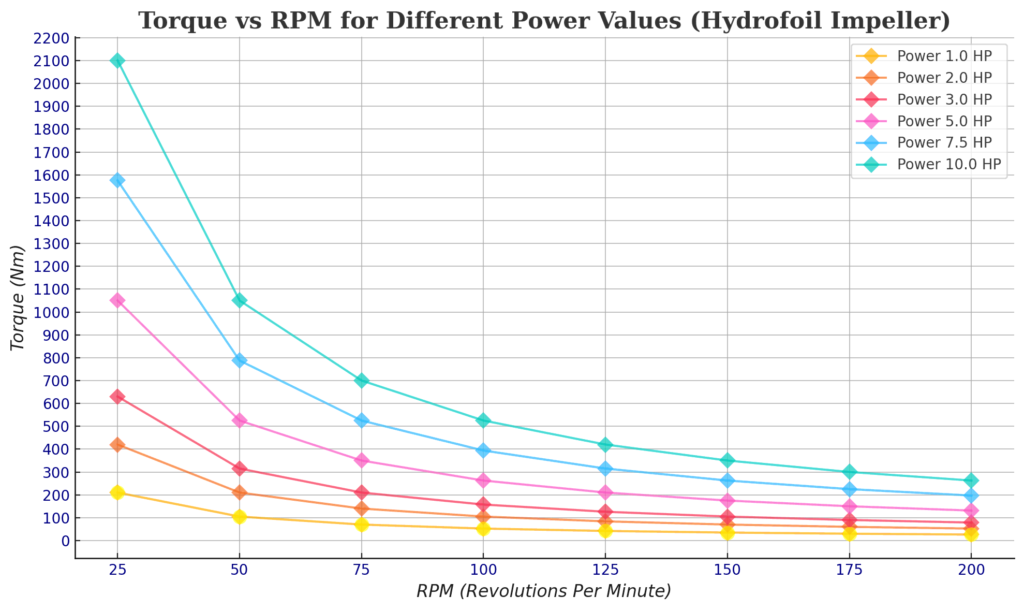
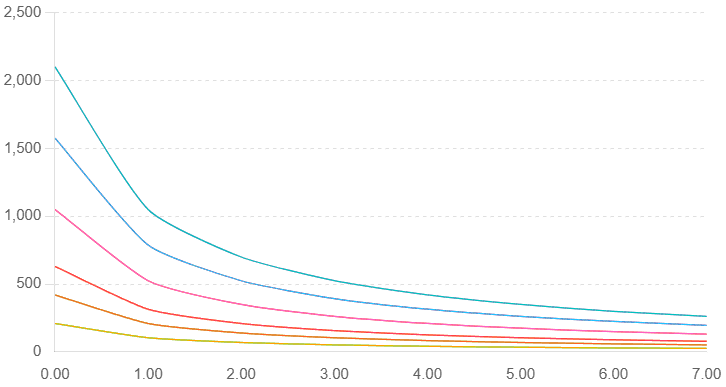
From the charts, it’s evident that higher power ratings can maintain torque levels even at increased RPM, while lower power configurations experience faster torque drop-offs. This data is valuable when balancing motor power and mechanical loads, ensuring smooth operation and avoiding overloading during startup or high-viscosity mixing.
Such analysis is especially beneficial when paired with gear-driven agitators or direct-drive systems found in process equipment like
👉 SV Industries – Anchor Impellers
📊 Torque vs RPM for Hydrofoil and Anchor Impeller
When comparing Hydrofoil Impellers to Anchor Impellers, understanding the relationship between Torque and RPM for both systems is vital. This chart provides a direct comparison, showing how Hydrofoil Impellers generally offer better flow efficiency at higher RPMs, whereas Anchor Impellers provide more stable torque at lower speeds.
By analyzing this data, engineers can select the most appropriate impeller type for applications requiring either high flow or high torque in their mixing processes.


The comparison clearly shows that Hydrofoil Impellers are ideal for high-speed mixing, offering lower torque at higher RPM, which leads to greater energy efficiency and faster mixing times. On the other hand, Anchor Impellers exhibit higher torque at lower speeds, making them the preferred choice for applications where high viscosity or stirring stability is essential.
If you’re selecting an impeller for your reactor vessel or agitator system, this data helps you optimize the balance between torque, speed, and flow, depending on your specific process requirements.
Energy Efficiency: Hydrofoil vs Pitched Blade vs Anchor Impellers
In today’s energy-conscious manufacturing environment, choosing the right impeller plays a crucial role in reducing operational costs. Among the many types of industrial impellers, hydrofoil, pitched blade, and anchor impellers stand out. This section compares their energy efficiency in real-world applications to help you make informed decisions for your mixing system.
Hydrofoil Impeller: Designed for Efficiency
Hydrofoil impellers are engineered for high flow, low shear mixing, making them one of the most energy-efficient impeller types. Their streamlined blades reduce turbulence and drag, translating into lower power consumption without compromising mixing performance.
Pitched Blade Turbine: Versatile but Power-Intensive
Pitched blade turbines (PBT) offer moderate flow with medium shear, suitable for blending and suspension applications. However, their blade design increases resistance, which leads to higher energy usage, especially in high-viscosity processes.
See the full range of Pitched Blade Turbines we manufacture at SV Industries.
Anchor Impeller: Great for High Viscosity, Not for Energy Saving
Anchor impellers are ideal for mixing high-viscosity fluids, such as creams, gels, or slurries. But their low flow generation and large surface area lead to significant energy consumption. They’re best suited for slow-speed, high-torque applications where precision mixing is more critical than energy efficiency.
Check out our Anchor Impeller designs that are engineered for GMP-compliant performance.
Why This Matters?
When it comes to power savings, hydrofoil impellers consistently outperform traditional alternatives. Not only do they require less torque and lower RPMs, but they also enable continuous mixing operations at a reduced cost—making them ideal for chemical, pharmaceutical, and food industries.
📊 Hydrofoil Impeller Efficiency Comparison: Hydrofoil Vs Pitched Blade Vs Anchor
Choosing the right impeller for your industrial mixing application depends largely on its efficiency, energy use, and the fluid dynamics it creates. This efficiency comparison chart offers a side-by-side view of Hydrofoil, Pitched Blade, and Anchor Impellers, helping engineers make data-driven decisions for their reactor vessels, blending systems, or batch processing equipment.
The chart evaluates mixing performance across various parameters, such as power per volume, flow pattern quality, and energy consumption efficiency.
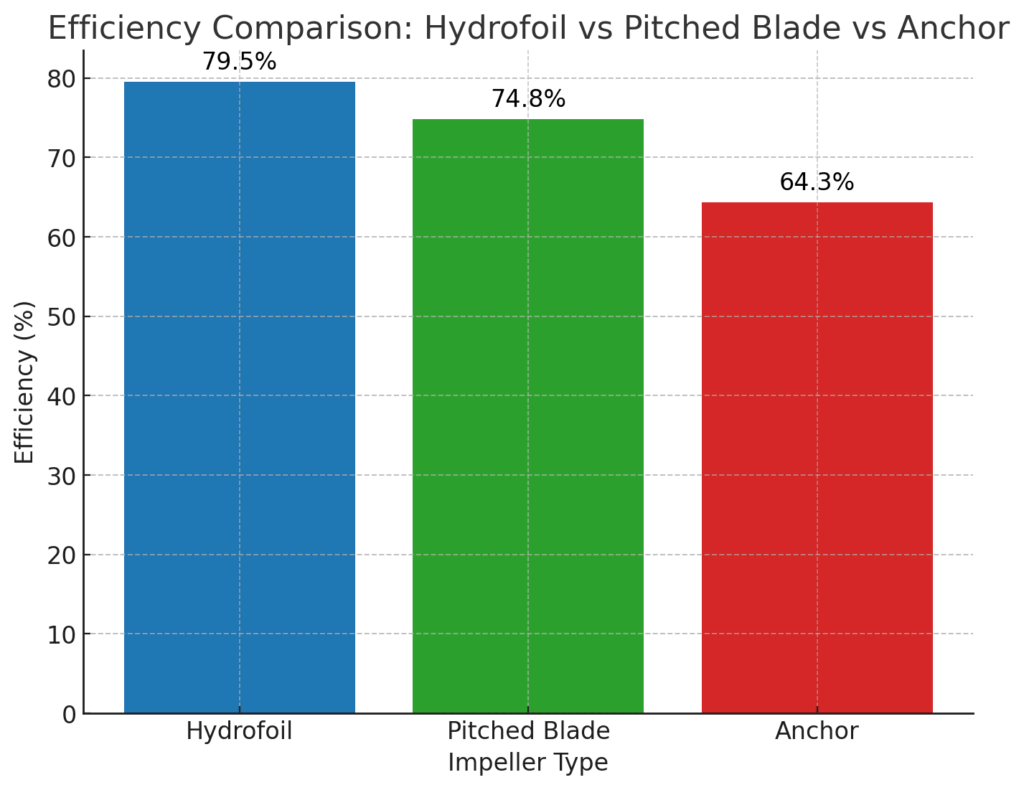
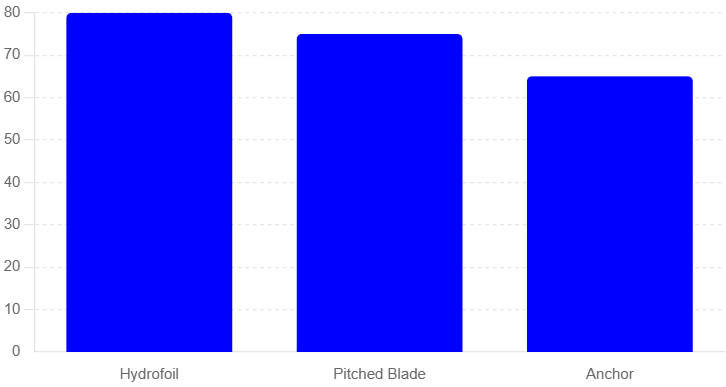
From the comparison, Hydrofoil Impellers clearly lead in flow efficiency, delivering high axial flow with low power input, making them ideal for low-viscosity, large-volume mixing. Pitched Blade Impellers offer a balance of flow and shear, suitable for moderate viscosity fluids. Anchor Impellers, while less energy-efficient, are indispensable in high-viscosity mixing tasks due to their wall-scraping action and torque strength.
This data is essential for manufacturers looking to reduce operating costs while maintaining optimal product consistency in chemical, pharmaceutical, or food industries.
If you’re considering switching to a more energy-efficient mixing setup, explore:
👉 SV Industries – Best Agitator Manufacturer in India
📊 Power Savings Comparison: Hydrofoil Vs Other Mixing Technology
In modern processing industries, energy savings directly impact profitability. This Power Savings Comparison Chart showcases how Hydrofoil Impellers outperform traditional impeller designs in power efficiency, particularly in continuous or batch mixing operations.
It helps plant designers and maintenance engineers choose solutions that reduce electricity consumption, cut operational costs, and increase system lifespan — without compromising on mixing performance.
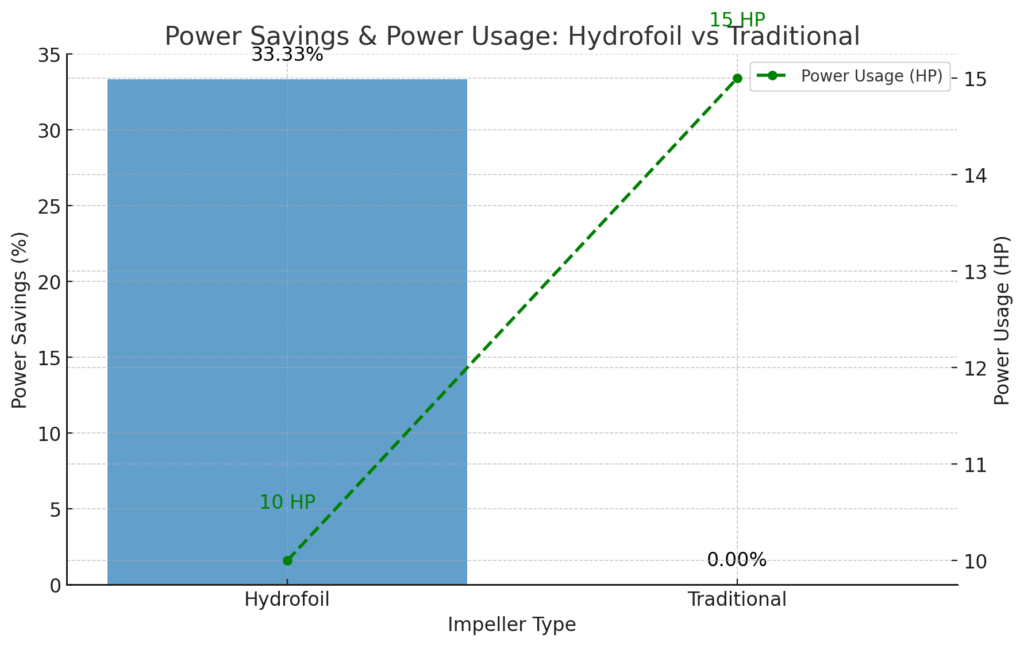

The data clearly illustrates that Hydrofoil Impellers can offer 20%–50% power savings in similar mixing applications. Their unique aerodynamic blade profile reduces drag and turbulence while maintaining a strong axial flow, unlike traditional impellers that often demand more energy for the same results.
These savings add up significantly in large-scale processing plants, especially where multiple mixers run simultaneously for extended durations. Reducing power demand also contributes to sustainable practices and lowers your carbon footprint.
To explore more innovative impeller technologies that save power and boost productivity, check out:
👉 SV Industries – Helical Impeller Design
Current Trends in Hydrofoil Impeller Design and Innovation
In the world of industrial mixing, Hydrofoil Impeller design is undergoing a silent revolution. Today’s manufacturers and process engineers are constantly pushing the boundaries of efficiency, sustainability, and precision. The focus has shifted from traditional trial-and-error approaches to data-driven engineering and CFD (Computational Fluid Dynamics) simulations, ensuring optimized axial flow and low power consumption under varying load conditions.
One of the most notable trends is the integration of energy-efficient blade profiles tailored to specific fluid viscosities and tank geometries. These modern hydrofoil blades are engineered to reduce turbulence, lower torque demand, and still maintain high circulation rates, especially in large-volume mixing tanks.
Material innovation is another major advancement. Impellers are now being crafted using corrosion-resistant stainless steel, duplex alloys, and even coated composites to enhance performance in aggressive chemical environments.
Another game-changer? The rise of modular and customizable impeller designs. Manufacturers like SV Industries – Agitator Manufacturer in Gujarat are offering tailored solutions to match process-specific mixing goals—from pharmaceuticals to petrochemicals—ensuring better product consistency and reduced operational cost.
Additionally, smart sensor integration and IIoT (Industrial Internet of Things) compatibility are making their way into mixing systems, allowing real-time monitoring of flow dynamics, energy usage, and maintenance needs—a step forward in building Industry 4.0-ready reactors.
As sustainability and process optimization become core goals across industries, the modern hydrofoil impeller is no longer just a component—it’s a strategic asset in achieving lower energy costs, improved yields, and environmental compliance.
Current Trends in Hydrofoil Impeller Design
Discover how modern engineering is redefining mixing performance & energy efficiency
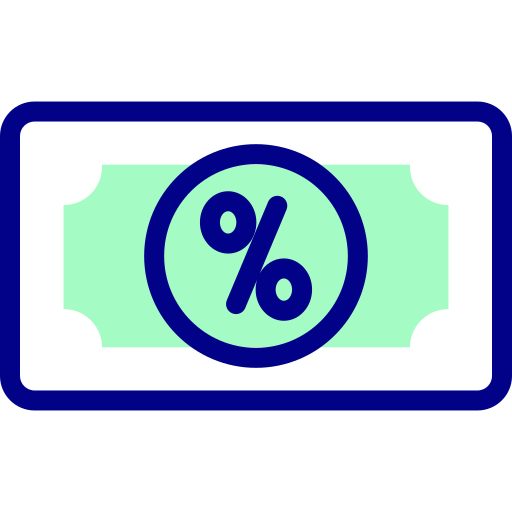
CFD-Optimized Blade Profiles
Improved flow dynamics with blade shapes tested through CFD simulation for enhanced axial flow.
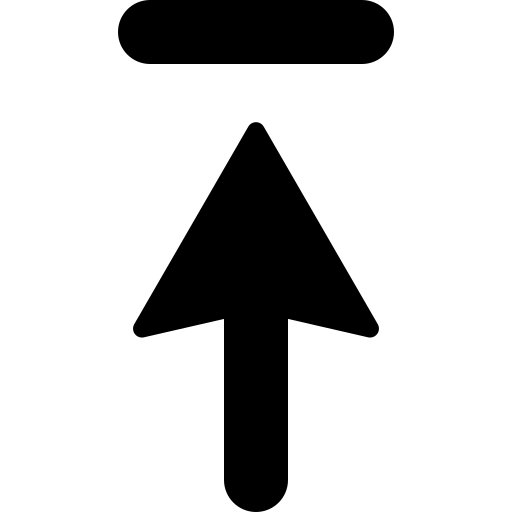
Material Innovation
Stainless steel & composite coatings now deliver high resistance in aggressive chemical environments.
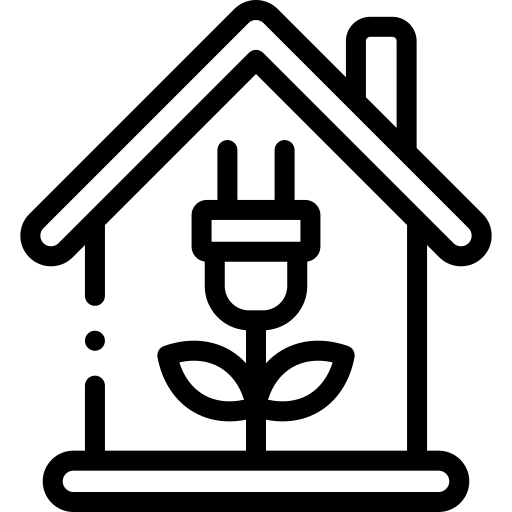
Smart Mixing Systems
Industrial mixing meets the future with IIoT integration for real-time efficiency monitoring and control.
"The Hydrofoil Impeller is no longer just a tool — it's a strategic advantage for sustainable, high-efficiency operations."
Technical Specifications Table – Hydrofoil Impellers
Explore the detailed technical specifications of our high-efficiency Hydrofoil Impellers designed for a wide range of industrial mixing applications. Each impeller is precisely engineered to deliver superior flow characteristics, low power consumption, and optimal mixing performance.
Parameter | Specification Range |
---|---|
Impeller Diameter | 100 mm to 2000 mm |
Speed (RPM) | 50 to 1500 RPM |
Flow Capacity | Up to 500 m³/h |
Material of Construction | SS304, SS316, Hastelloy, Duplex Steel |
Number of Blades | 3 or 4 |
Mounting Options | Flanged, Threaded, Welded |
Surface Finish | Mirror Polish, Matt Finish, Electro Polish |
Application Type | Low to Medium Viscosity Fluids |
Compatibility | Compatible with Agitators and Chemical Reactors |
Our Hydrofoil Impellers are available with complete customization options to match your industrial process requirements. Whether you’re working with chemical reactors, fermentation systems, or blending tanks, we ensure precise alignment with your operational goals.
📩 Need a custom impeller for your plant? Contact us today for expert assistance.
Installation and Maintenance Guidelines for Hydrofoil Impellers
Proper installation and maintenance are key to ensuring the long-term performance, safety, and efficiency of your hydrofoil impeller system. Whether you’re upgrading an existing setup or installing a new system, follow these best practices to maximize your investment.
🛠️ Installation Guidelines (Step-by-Step)
Verify Shaft Alignment
Misalignment can lead to vibration, seal wear, and reduced impeller efficiency. Always use a dial gauge or laser tool for precision.Check Impeller Blade Orientation
Ensure the hydrofoil blades are mounted in the correct axial direction for optimal fluid flow. Misorientation can reduce mixing performance.Secure Mounting with GMP Standards
Use stainless steel fasteners and food-grade gaskets for compliance in pharma, food, or chemical applications.
Explore our GMP-compliant mixing vessels.Test Drive the System
Before full operation, run the agitator at low RPMs and monitor for unusual noise or wobble.
For reliable agitators, visit our Agitator Product Page.
🔧 Maintenance Best Practices
Routine Inspection
Check for signs of wear, corrosion, or buildup every 30 to 60 days depending on usage.Lubrication of Bearings
Use the recommended lubricants and intervals to prevent friction-related issues.Vibration Monitoring
Install vibration sensors for large-scale systems to detect imbalance early.Cleaning Protocols
Use CIP (Clean-In-Place) systems or manual cleaning based on your industry standards.Seal Maintenance
Periodically inspect and replace mechanical seals, especially in high-viscosity or abrasive environments.
For heavy-duty, low-maintenance systems, consider our Industrial Reactors built for rugged operations.
Why Choose SV Industries for Hydrofoil Impeller Solutions
When it comes to high-performance Hydrofoil Impellers, SV Industries stands out as a trusted manufacturer and supplier in India. With decades of engineering experience and a commitment to precision, we deliver custom mixing solutions that are efficient, reliable, and tailored to your needs.
🔹In-House Design & Manufacturing
Our team of experts uses advanced CAD tools and CFD analysis to create precision-designed impellers that ensure optimal mixing performance in your specific application.
🔹Premium Quality Materials
We manufacture Hydrofoil Impellers using SS 304, SS 316, Hastelloy, and other corrosion-resistant alloys to ensure long-term durability and chemical compatibility.
👉 Check out our SS Vessel Manufacturing
🔹Industry-Specific Solutions
Whether you operate in chemical processing, pharmaceuticals, wastewater treatment, or food & beverage, our impellers are tailored for your industry standards and certifications.
🔹Proven Track Record
We have supplied custom agitators and impellers to top-tier companies across India, earning a reputation for quality, consistency, and support.
🔹Complete Agitation Systems
Looking beyond impellers? SV Industries offers complete agitator systems, reactors, and storage tanks to support your entire process setup.
📞 Need expert help with your mixing system?
Contact Us today or explore our Hydrofoil Impeller page for detailed specifications, use cases, and technical support.
Hydrofoil Impeller Manufacturer and Suppliers in India
When it comes to industrial mixing solutions, hydrofoil impellers have emerged as a game-changer, offering high efficiency and low power consumption. In India, SV Industries, based in Ahmedabad, has positioned itself as a leading hydrofoil impeller manufacturer and supplier, catering to industries like chemical processing, water treatment, and food production. With a focus on precision engineering and innovative designs, SV Industries delivers world-class solutions tailored to diverse industrial needs.
India is home to numerous manufacturers specializing in hydrofoil impellers, but not all offer the same level of quality and customization. At SV Industries, we ensure that every impeller is crafted with meticulous attention to detail, ensuring optimal performance and durability. Our company has gained recognition as a trusted hydrofoil impeller supplier in India, owing to our commitment to quality, timely delivery, and competitive pricing.
🛠️ What Makes Us the Preferred Choice?
✅ Precision-Engineered Hydrofoil Designs
Designed for low power consumption and high axial flow, ideal for large mixing tanks.
✅ Wide Material Range
Available in SS 304, SS 316, Hastelloy, Duplex Steel, and more — built to withstand aggressive media.
👉 Explore: Industrial Reactors
✅ Nationwide Supply Network
We serve clients across Ahmedabad, Gujarat, Maharashtra, Karnataka, Delhi, Tamil Nadu, and other major industrial zones in India.
✅ Custom Agitator Integration
We design impellers compatible with our full range of agitators and mixing vessels — ensuring smooth process performance.
✅ Quick Delivery & Support
Fast turnaround times and technical assistance from selection to installation.
📌 Whether you need a standalone Hydrofoil Impeller or a complete agitation system, SV Industries is your one-stop solution in India.
📞 Request a Quote or speak with our team today!
Key Considerations When Choosing Hydrofoil Impeller Manufacturers and Suppliers
Selecting the right hydrofoil impeller manufacturer and supplier is critical to ensuring the efficiency and reliability of your industrial processes. Here are some key factors to consider:
- Experience and Expertise: opt for manufacturers and suppliers with a proven track record and extensive experience in producing high-quality hydrofoil impellers.
- Customization Capabilities: Ensure the manufacturer can provide customized solutions to meet your unique requirements.
- Material Quality: The durability and performance of an impeller largely depend on the quality of materials used. Always choose manufacturers who use premium-grade materials.
- Technical Support: A good supplier should offer robust technical support and after-sales services, including installation guidance and maintenance.
- Cost-Effectiveness: While cost is an important factor, it’s essential to balance affordability with quality. Opt for a manufacturer who provides value for money.
- Client Reviews and Testimonials: Check reviews and testimonials to gauge the reputation and reliability of the manufacturer and supplier.
By keeping these considerations in mind, businesses can partner with the best hydrofoil impeller manufacturers and suppliers in India, ensuring seamless operations and long-term benefits.
Frequently Asked Questions (FAQs) About Hydrofoil Impellers
What is a hydrofoil impeller agitator?
A hydrofoil impeller agitator is a highly efficient mixing device designed with a unique blade profile to maximize fluid flow while minimizing energy consumption. It is widely used in industries for blending, dispersing, and maintaining uniformity in various liquids.
What industries commonly use hydrofoil impeller agitators?
Hydrofoil impeller agitators are extensively used in industries like chemical processing, pharmaceuticals, water treatment, food and beverages, petrochemicals, and paint manufacturing. Their versatility and efficiency make them a preferred choice in these sectors.
What are the advantages of using a hydrofoil impeller agitator?
Hydrofoil impeller agitators offer several benefits, including:
- High energy efficiency.
- Improved flow patterns.
- Reduced operational costs.
- Versatility in handling low to medium viscosity fluids.
- Enhanced mixing performance with minimal shear forces.
How does a hydrofoil impeller agitator work?
A hydrofoil impeller agitator works by rotating its specially designed blades within a tank or vessel, creating axial and radial flow patterns. This movement ensures uniform mixing, effective blending, and suspension of solids in liquids.
What materials are used to manufacture hydrofoil impeller agitators?
Hydrofoil impeller agitators are typically made from high-grade materials like stainless steel (SS304, SS316) or other corrosion-resistant alloys. The choice of material depends on the application and the type of fluids being processed.
What are the key applications of hydrofoil impeller agitators?
Key applications of hydrofoil impeller agitators include:
- Mixing chemicals and reagents.
- Blending ingredients in food processing.
- Maintaining uniformity in wastewater treatment plants.
- Dissolving solids in liquid mediums.
How do I choose the right hydrofoil impeller agitator for my application?
Selecting the right hydrofoil impeller agitator depends on factors like the viscosity of the liquid, tank size, process requirements, and desired mixing efficiency. Consulting with experts at SV-Industries can help you find the perfect solution.
Are hydrofoil impeller agitators energy efficient?
Yes, hydrofoil impeller agitators are known for their energy efficiency. Their blade design minimizes power consumption while achieving optimal mixing, making them a cost-effective choice for various industrial applications.
Can hydrofoil impeller agitators be customized?
Absolutely! At SV-Industries, we offer customized hydrofoil impeller agitators tailored to your specific process requirements, including blade design, speed, and materials.
What is the maintenance requirement for a hydrofoil impeller agitator?
Hydrofoil impeller agitators require minimal maintenance, thanks to their robust design. Regular inspections, cleaning, and lubrication of moving parts ensure a long service life and consistent performance.