Leading SS Jacketed Vessel Manufacturer in India
In the world of industrial process engineering, precision matters — and so does reliability. At SV Industries, we specialize in manufacturing high-performance SS Jacketed Vessels designed to meet the demanding needs of industries like pharmaceuticals, chemicals, food processing, and cosmetics. With a strong commitment to quality, customization, and compliance, we’ve earned our reputation as a trusted stainless steel vessel manufacturer in India.
This comprehensive guide is built for project engineers, plant managers, and procurement heads who are seeking reliable information to make informed purchase decisions. Whether you’re upgrading your facility or planning a new process line, this blog will help you understand:
What SS Jacketed Vessels are and how they work
Design types and customization possibilities
Key performance metrics and technical considerations
How to choose the right vessel for your application
Why working with an experienced manufacturer like SV Industries gives you an edge
Let’s explore the critical design insights, selection tips, and real-world considerations that can make a difference in your next purchase.
What is an SS Jacketed Vessel?
An SS Jacketed Vessel is a stainless steel tank designed with an external jacket (outer layer) that allows controlled heating or cooling of the fluid inside. This jacket acts like a thermal shell, enabling hot or cold media—such as steam, water, glycol, or oil—to circulate around the vessel without coming into direct contact with the process material.
These vessels are commonly used in pharmaceutical, chemical, food, and cosmetic industries where temperature regulation is critical to the process.
There are different types of jackets, including:
Conventional Jackets (for low-pressure heating)
Dimple Jackets (for efficient thermal transfer and pressure resistance)
Limpet Coils (external coils for heavy-duty heating or cooling)
✅ Curious how limpet coil jackets compare? Check out our Limpet Coil Reactor Vessel page for deeper insights.
🧠 Did You Know?
Many reactor vessels use jacketed designs to ensure controlled chemical reactions. Explore more on our Chemical Process Reactor page.
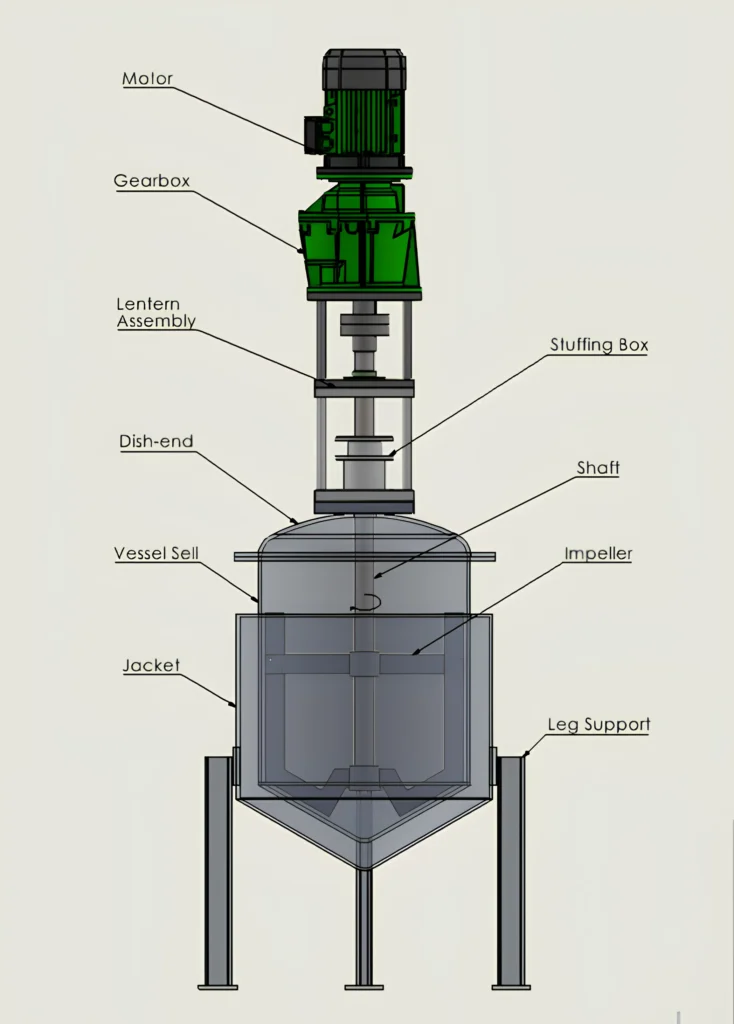
Working Principle of SS Jacketed Vessels
An SS Jacketed Vessel operates on the principle of indirect heat exchange. Instead of directly exposing the process material to heat or cold, a secondary fluid (like steam, hot water, or chilled glycol) flows through the jacket—an external layer wrapped around the main vessel body.
This circulating media either heats or cools the product inside the vessel by transferring energy through the stainless steel wall. As a result, the internal material is processed at a controlled and uniform temperature, making this setup ideal for temperature-sensitive applications.
🔁 Heating and Cooling Flow Explained
🔥 Heating Mode: Hot media (e.g., steam) enters the jacket, transferring heat to the vessel’s contents.
❄️ Cooling Mode: Chilled media flows through the jacket to absorb heat from the vessel.
♻️ The circulation is typically continuous, regulated by a temperature control unit (TCU).
For enhanced thermal contact, our vessels often include high-efficiency agitator systems that ensure even temperature distribution across the product.
🧱 Types of Jackets and How They Work
Jacket Type | How It Works | Best For |
---|---|---|
Conventional Jacket | A large outer shell covers the vessel; good for low-pressure operations | General heating |
Dimple Jacket | Dimpled pattern improves turbulence & heat transfer with less volume | Food, Pharma |
Limpet Coil | External coil welded around the vessel; allows high-pressure media | Chemical & heavy-duty industries |
✅ Learn more about Limpet Coil Jacketed Vessels for high-temperature or high-pressure processes.
Design & Customization Options for SS Jacketed Vessels
At SV Industries, we specialize in manufacturing custom SS jacketed vessels tailored to your process requirements, industry standards, and plant configurations. From jacket type to capacity, agitation, insulation, and nozzle layout, every vessel can be engineered to meet your specific heat transfer and mixing goals.
Whether you’re scaling a batch process or designing a new production line, our team can assist you in building the most efficient and compliant jacketed vessel for your application.
🧱 Jacket Types We Offer
Selecting the right jacket type is critical for thermal efficiency, cost, and maintenance. SV Industries offers:
🔸 Dimple Jacket
Lightweight and cost-effective, ideal for moderate pressures and uniform heating.
✔ Preferred in food, beverage, and pharmaceutical industries.🔸 Limpet Coil Jacket
Heavy-duty external coils for high-pressure heating/cooling operations.
✔ Ideal for chemical processing, resins, and solvents.
👉 See our Limpet Coil Reactor Vessel for design examples.🔸 Conventional Jacket
Full-sleeve jacket for low-pressure steam or water applications.
✔ Economical choice for general-purpose heating.
📦 Customizable Capacities & Configurations
We manufacture vessels in volumes from 100 liters to 30,000 liters, suitable for:
Batch or continuous processes
Vertical or horizontal orientation
Skid-mounted setups
Add-ons include:
Top or side-mounted agitator (e.g., anchor impeller, pitch blade)
Multiple nozzles for steam inlet, temperature sensor, sampling, or vacuum port
Thermal insulation: Rockwool or PU foam with SS cladding
Finish options: Mirror polish, matte finish, or electro-polished interior
📐 Each vessel is delivered with a custom layout drawing and optional 3D view or animation for your approval.
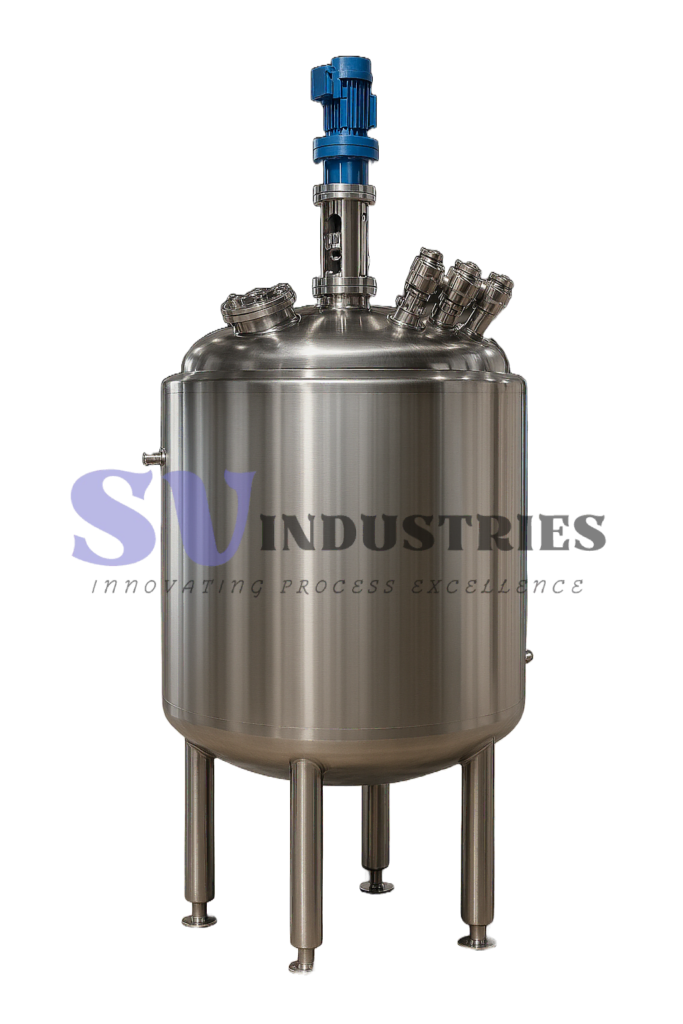
🧪 Comparison of Heat Transfer Efficiency Across Different Jacket Types
This bar chart compares the heat transfer performance of three common jacket types used in stainless steel process vessels—Dimple Jacket, Limpet Coil, and Half-Pipe Coil. The heat transfer coefficient is a key indicator of how efficiently each design transfers heat, impacting heating/cooling time and process efficiency.
Jacket Type | Heat Transfer Coefficient (W/m²·K) | Remarks |
---|---|---|
Dimple Jacket | 300 – 500 | Low pressure, economical, moderate efficiency |
Limpet Coil | 500 – 1000 | Suitable for high-pressure media, good heat transfer |
Half-Coil | 600 – 1200 | High flow rates, best efficiency, used in critical heating/cooling |
📌 Note: Values are generalized for water or steam applications; actual results depend on fluid, flow rate, and surface area.
🏭 Configurations Based on Industry Use
Different industries demand different jacket configurations, materials, and pressure ratings. This table gives a quick glance at which setup is most suitable for your application — saving time during design discussions and procurement.
🧬 Industry | 🧊 Recommended Jacket Type | 🧱 Preferred Material | ⚙️ Pressure Rating |
---|---|---|---|
Pharma | Limpet Coil + GMP Compliant | SS 316L | 6 bar |
Chemical | Dimple Jacket | SS 304 | 3 bar |
Food | Half Coil Jacket | SS 304 | 2.5 bar |
What You Should Know:
Pharma-grade vessels often use SS 316L with limpet coil jackets for superior corrosion resistance and hygienic compliance.
The chemical industry prefers dimple jackets for efficient heat transfer and pressure durability.
For food applications, half coil jackets offer gentle heating suited for sensitive ingredients.
📌 This breakdown helps match your industry’s compliance and thermal processing needs — ensuring safe and efficient operation.
Things to Consider Before Buying SS Jacketed Vessels
Choosing the right SS Jacketed Vessel goes beyond just volume and price — it requires understanding your process parameters, cleaning needs, and material compatibility. At SV Industries, we guide our customers through every key factor to ensure long-term performance, regulatory compliance, and ease of operation.
🌡️ 1. Define Your Temperature & Pressure Requirements
Every application has a thermal and mechanical threshold. Selecting the correct jacket and vessel rating is crucial.
✅ Ask yourself:
What’s the maximum operating temperature?
Will the jacketed system be used for cooling, heating, or both?
Is pressurization required inside the vessel or jacket?
👉 Example:
If you’re operating above 120°C and 4 bar pressure, a limpet coil jacket with SS316 is often ideal.
💧 2. Know the Type of Thermal Media Used
Different jacket types perform better with different thermal transfer fluids:
Thermal Media | Recommended Jacket |
---|---|
Steam | Limpet Coil / Dimple |
Hot Water | Dimple Jacket |
Glycol/Chilled Brine | Dimple / Conventional |
Selecting the wrong jacket for your heat transfer fluid can reduce efficiency by 20–30%.
🧼 3. Cleaning & Sterilization Needs (CIP/SIP)
Industries like pharma and F&B require Clean-In-Place (CIP) or Steam-In-Place (SIP) capabilities.
✅ Features that enable easy cleaning:
Crevice-free internal welds
Spray balls or rotary nozzles
Drainage slope with bottom outlet valve
Mirror-polished surfaces to prevent residue buildup
All vessels can be customized for GMP compliance with complete documentation.
✨ 4. Surface Finish Matters — Both Inside & Outside
Different industries need different finishes depending on hygiene or aesthetic preferences.
Finish Type | Best For |
---|---|
Mirror Polish | Pharma, biotech, cosmetics |
Matte Finish | Chemicals, paint, industrial |
✅ We offer Ra < 0.5 μm for pharma-grade vessels.
🛒 Need Help Choosing?
Our engineering team provides free consultation and layout drawings to help you choose the ideal configuration.
Energy & Process Optimization Insights
SV Industries designs each SS Jacketed Vessel with a strong focus on energy efficiency, operational cost savings, and sustainable performance. This section is especially useful for plant engineers, production heads, and consultants aiming to improve OPEX (operational expenditure) without compromising on process quality.
💰 Batch Processing Cost Reduction
In high-volume industries like pharmaceuticals, chemicals, and F&B, jacketed vessels often run 24×7. SV Industries’ vessels are optimized to reduce energy waste during each batch.
✅ How We Reduce Cost per Batch:
Fast thermal response: Reduces startup time, saving fuel or electricity.
Efficient insulation: Minimizes heat loss during idle or low-flow conditions.
Modular agitation systems: Run at optimized RPM to reduce power usage.
📌 Example:
A typical 5000L SS Jacketed Reactor with dimple jacket and PID-controlled steam inlet saved up to ₹15,000/month in energy costs after switching from a conventional limpet coil design.
🔌 Utility Management for Maximum Efficiency
Utility optimization is key to plant-wide savings. SV Industries’ jacketed vessels come with design features that allow precision control and data-driven utility monitoring.
⚙️ Key Utility Optimization Features:
Smart jacket zoning: Only heats required zones, reducing utility load.
Steam trap and condensate return system: Prevents energy loss.
Agitation system with VFD: Reduces electricity during partial loads.
CIP-ready designs: Lower cleaning water and detergent usage.
Result:
Up to 25% lower steam usage, 20% lower chilled water consumption, and faster cleaning cycles compared to generic designs.
⚡ Energy Consumption vs. Batch Volume
This chart illustrates how energy usage scales with batch volume during thermal processing in a jacketed reactor or vessel. It’s essential for process engineers, procurement teams, and plant managers aiming to optimize cost and utility usage.
📌 Chart Explanation
As batch size increases, energy usage rises proportionally.
A 500-liter batch consumes ~32 kWh, whereas a 5000-liter batch requires over 319 kWh.
This trend reflects the linear increase in thermal load needed to heat larger volumes, assuming constant heating efficiency and target temperature.
🔍 Key Observations:
Doubling the batch size = doubling the energy load.
Helps in power infrastructure planning and cost per batch estimation.
Highlights the need for better insulation or pre-heating strategies in larger vessels.
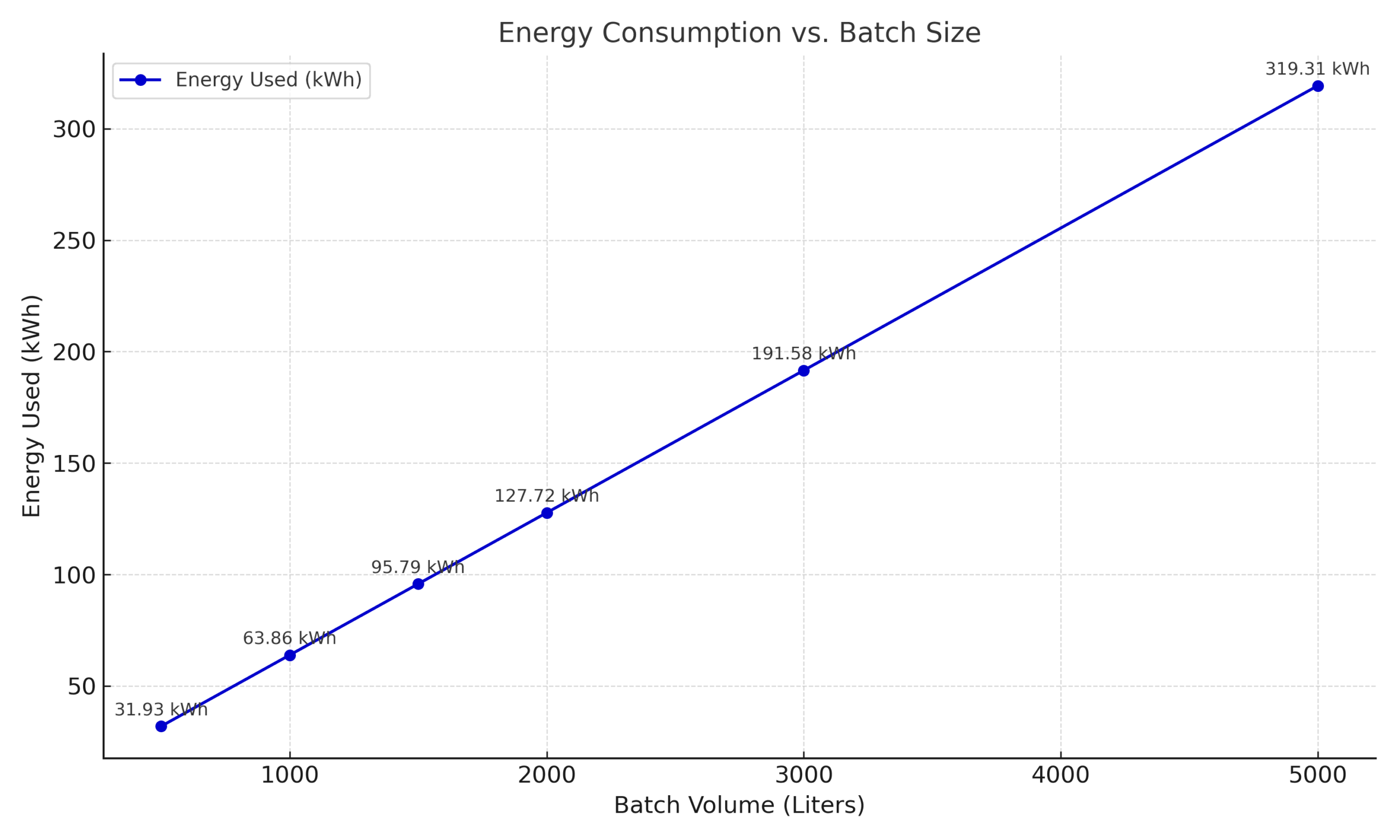
♨️ Steam Consumption vs. Fluid Volume
Efficient steam usage is essential for thermal processing, jacketed heating, and sterilization in reactor vessels. This chart helps visualize the relationship between vessel volume and required steam flow to maintain consistent heating performance.
📌 Chart Explanation
As the vessel volume increases, the steam consumption rises proportionally. This data shows how much steam is needed per hour to heat different fluid volumes effectively:
A 100-liter vessel requires about 14.93 kg/hr of steam.
For 1000 liters, it jumps to 149.29 kg/hr.
At 5000 liters, consumption exceeds 746 kg/hr.
🔍 Key Insights:
The relationship is linear, helping you estimate steam requirements at scale.
Useful for boiler sizing, energy audits, and heat exchanger design.
Supports energy-efficient decision-making in pharmaceutical, chemical, and food processing industries.
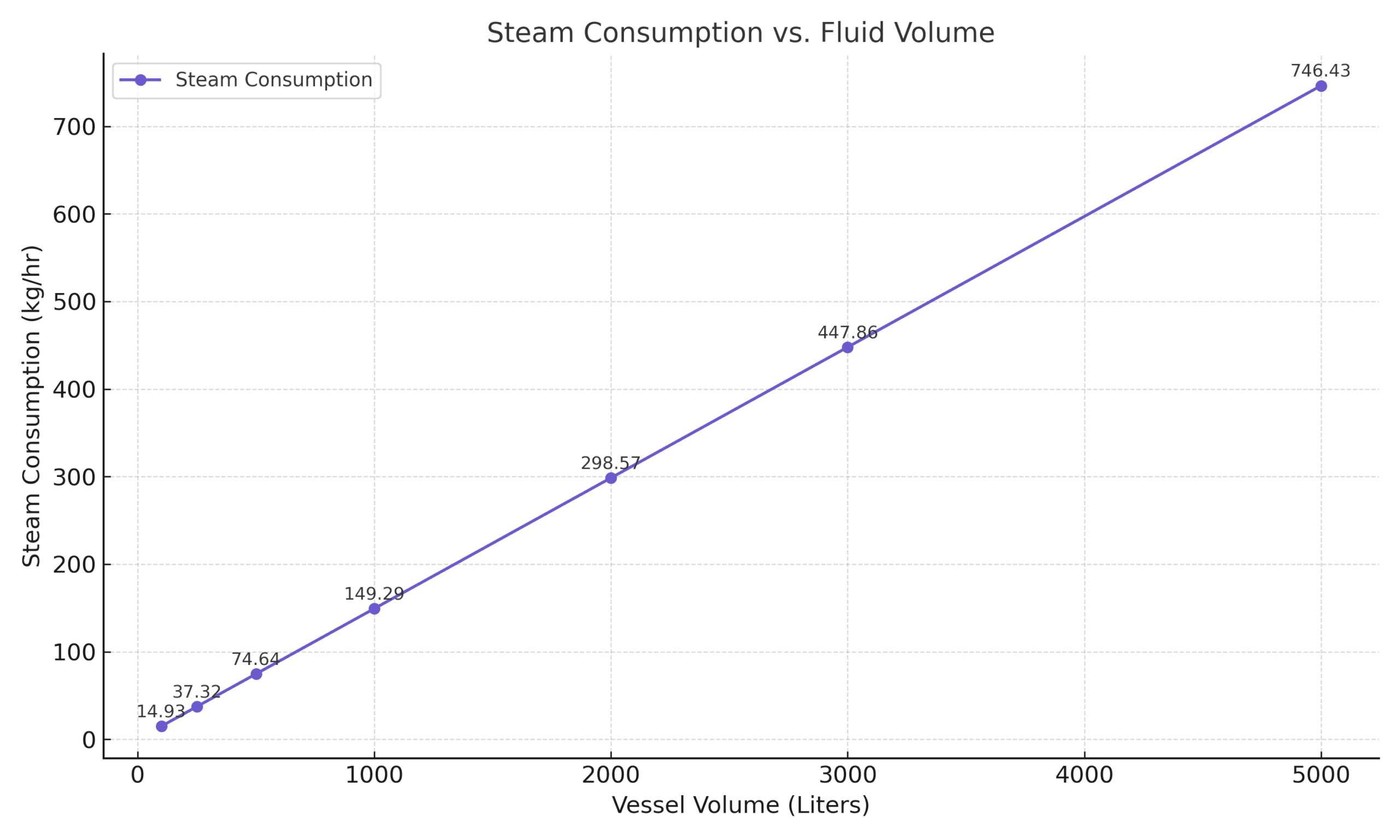
🔥 Effect of Media Inlet Temperature on Heating Time
The temperature of the heating media (such as steam, thermal oil, or hot water) has a direct impact on the time required to heat the vessel’s contents to the desired temperature. This relationship is critical for optimizing batch heating processes, improving energy efficiency, and reducing production cycle time. The table below shows how increasing inlet temperature significantly reduces heating time to reach 80°C.
📌 Chart Explanation
Notice how dramatically heating time improves with even small increases in media inlet temperature. For example, jumping from 80°C to 100°C almost halves the heating time — from ~70 minutes to just ~40 minutes. As we move toward 160–180°C, the efficiency peaks, reaching heating times as low as 15 minutes.
This curve highlights a key design insight:
✅ Higher inlet temperatures = Faster heating + Shorter batch cycles
✅ Ideal for thermal-sensitive applications like API synthesis, emulsion heating, or resin polymerization
✅ Enables energy savings, higher productivity, and better process control
Whether you’re optimizing a reactor vessel in pharma, chemical, or food processing, this chart reinforces one fact:
📌 Choosing the right media inlet temperature isn’t just about heat — it’s about total process efficiency.
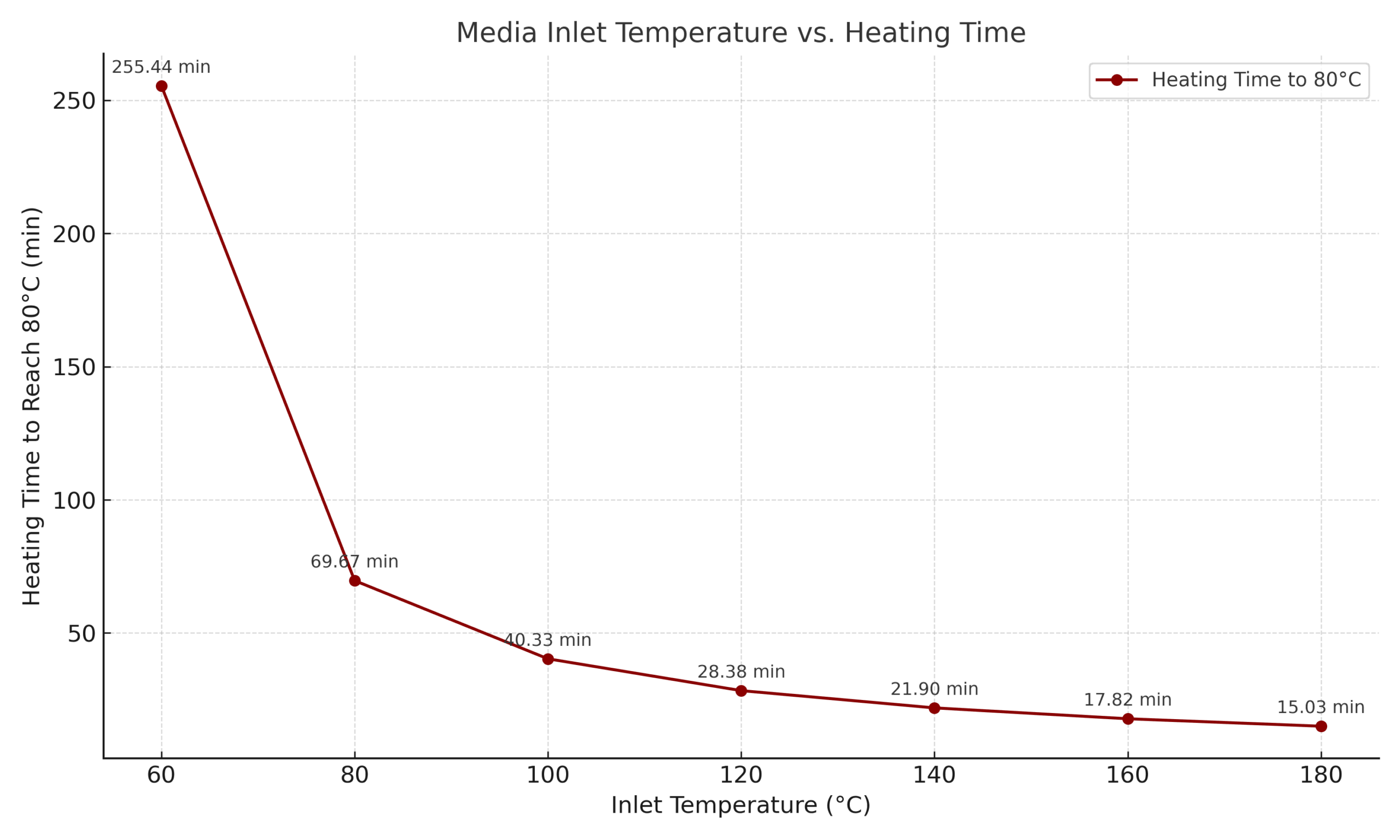
SS Jacketed Vessel vs Limpet Coil Vessel – Which is Right for You?
When choosing the ideal industrial vessel for your application, the debate often comes down to SS Jacketed Vessels vs Limpet Coil Vessels. Both are widely used in chemical, pharma, food, and cosmetic industries—but their design, efficiency, and cost vary depending on the use case.
To help you decide, here’s a clear comparison:
⚙️ Feature | 🧊 SS Jacketed Vessel | 🔁 Limpet Coil Vessel |
---|---|---|
Design | External shell wraps around the vessel for fluid circulation | Helical coils (usually half-pipe) welded on the vessel body |
Heat Transfer Efficiency | Moderate – best for low to medium thermal loads | High – ideal for high-temperature & pressure processes |
Pressure Handling | Up to 3 bar (depending on design) | Handles up to 12 bar or more |
Maintenance | Easier to clean and inspect | Slightly complex due to coil design |
Cost | More economical | Slightly higher due to complex welding and design |
Applications | Food, beverages, cosmetics, general-purpose mixing | Chemical reactions, resin cooking, solvent recovery – see our Limpet Coil Reactor Vessel |
Material Options | SS304, SS316, SS316L | SS304, SS316, MS with coil |
Suitability | Best for processes with gentle heating/cooling needs | Best for thermal-intensive and high-pressure processes |
👉 At SV Industries, we help clients select between SS jacketed vessels and limpet coil vessels based on media type, temperature, pressure, and budget. Still unsure? Talk to our experts on the Contact Us page.
Common Mistakes to Avoid During SS Jacketed Vessel Selection
Choosing the right SS jacketed vessel for your process plant isn’t just about capacity or cost — it’s about long-term performance, safety, and ROI. Based on our experience at SV Industries, here are the most common mistakes we’ve seen — and how you can avoid them:
❌ 1. Oversizing or Undersizing the Vessel
Many buyers either oversize “just to be safe” or undersize to reduce costs. Both decisions can cause inefficient heat transfer, poor mixing, or even batch failures. Always calculate based on batch volume, hold time, and thermal load.
🔍 Need help? Our Reactor Vessel experts assist with right-sizing based on your input data.
⚠️ 2. Choosing the Wrong Material Grade
Not all stainless steels are equal. SS304 may be economical, but if you’re dealing with corrosive chemicals, SS316 or SS316L is a smarter long-term investment. Refer to our detailed guide on SS Jacketed Vessel Materials.
🧽 3. Ignoring Cleanability and Maintenance
Design that doesn’t allow easy access for cleaning or inspection can lead to downtime, especially in pharma or cosmetic applications. Go for GMP-friendly designs with mirror polish or removable jackets if needed.
Check our Anchor Impeller page for examples of hygienic design options.
🌡️ 4. Skipping Thermal Calculations
Ordering a vessel without understanding the required heating/cooling load, flow rate, or jacket design (limpet vs dimple) is risky. Our team uses proper thermal engineering to match your process needs with the right jacket type.
You can also explore detailed jacket comparisons here.
Maintenance & Cleaning Guidelines for Long-Term Performance
Want your SS jacketed vessel to last 10+ years without downtime? Then maintenance isn’t optional — it’s essential. Whether you’re in pharma, chemicals, or cosmetics, proper cleaning and upkeep can dramatically extend vessel life, preserve product quality, and avoid costly repairs.
Let’s break it down:
🚿 1. CIP & SIP Integration: Clean Without Opening the Vessel
Modern process plants demand automated cleaning solutions. CIP (Clean-In-Place) and SIP (Sterilize-In-Place) systems ensure your jacketed reactor stays contaminant-free—without disassembly.
✅ Best for: Pharma, food, cosmetic sectors
🔍 Want GMP-friendly designs? See our SS Jacketed Vessel options built for CIP/SIP compatibility.
✨ 2. Go for the Right Surface Finish
Your vessel’s internal finish matters more than you think:
Finish Type | Best For |
---|---|
Mirror Polish | Pharma, biotech, cosmetics |
Matte Finish | Chemicals, paint, industrial |
Smooth, polished surfaces prevent product build-up, ease cleaning, and resist bacterial growth. Learn more on our Anchor Impeller and Helical Impeller pages—where finish quality directly impacts hygiene.
🛡️ 3. Anti-Corrosion Best Practices
Even stainless steel can corrode if improperly maintained. Here’s how to protect your investment:
✔️ Use SS316 or SS316L for high-corrosion applications
✔️ Avoid harsh chlorides or incompatible media
✔️ Rinse vessels immediately after acidic batches
✔️ Use passivation regularly to maintain corrosion resistance
Want guidance on the best material selection? Visit SS Jacketed Vessel Material Options.
🛠️ BONUS: Prolong Your Vessel’s Life
🧊 Maintain correct chiller pressure
🔍 Inspect for thermal cracks in jackets
🧽 Schedule monthly external cleaning
🔧 Lubricate any rotating or moving assemblies regularly—especially if paired with an industrial agitator
Why Trust SV Industries as Your SS Jacketed Vessel Manufacturer?
When you’re investing in a stainless steel jacketed vessel, you’re not just buying equipment — you’re choosing a long-term partner in your process success. At SV Industries, we combine engineering excellence with real-world industry experience to deliver tailored, high-performance vessels that meet global standards.
Here’s why top manufacturers across India trust us:
🛠️ 1. In-House Fabrication for Better Quality Control
Unlike many others, we don’t outsource fabrication. Every SS jacketed vessel is built in-house at our Ahmedabad facility, ensuring full control over material selection, welding quality, and compliance. This allows us to promise consistent quality and faster delivery times.
Want to know more about our fabrication strength? Visit our About Us page.
🧪 2. Tailor-Made Designs to Suit Your Process
From compact pharma vessels to chemical-grade reactors, we design vessels that match your exact process parameters. Need a vessel with CIP/SIP, custom impeller, or multi-zone jackets? We’ve got you covered.
Explore matching Agitator Solutions and Impeller Types that integrate seamlessly with our vessels.
🛡️ 3. ISO & ASME-Compliant Manufacturing
All fabrication follows ISO-certified procedures, and we also support ASME section VIII designs where required. Each vessel undergoes thorough hydro testing, radiography, and quality checks—making them suitable for regulated industries like pharmaceuticals and specialty chemicals.
🌐 4. Trusted by Clients Across India
We proudly serve a wide range of industries across Gujarat, Maharashtra, Tamil Nadu, Punjab, and beyond. Our clients appreciate our responsive service, custom engineering, and reliable after-sales support.
Want to see our work? Visit our Gallery or browse industry-specific solutions like:
📞 Ready to build your next jacketed vessel? Reach out via our Contact Us page.
Frequently Asked Questions (FAQs) of SS Jacketed Vessels
What is the optimal jacket surface area required for a 500-liter reactor?
The jacket surface area depends on your heat transfer media, desired heating/cooling rate, and the working temperature range. For a 500-liter SS jacketed reactor, the jacket area typically ranges from 0.6 to 1.0 m², but must be calculated precisely using thermal load formulas. You can request a jacket surface area vs volume chart from our SS Jacketed Vessel page.
Can I use chilled glycol in a limpet coil jacketed reactor vessel?
Yes, chilled glycol is commonly used in limpet coil reactor vessels, especially for exothermic reactions requiring fast heat dissipation. However, ensure the coil material (SS316 or SS316L) is compatible with glycol and check for proper flow rate and viscosity to avoid pressure drop.
Is it possible to combine both limpet coil and dimple jacket in a single reactor?
Absolutely. For advanced thermal control, we offer dual jacketed reactors with limpet coils for heating and dimple jackets for cooling zones. This is ideal for batch processes that require precise thermal cycling.
How does jacket pressure affect the selection of gasket and flange rating?
Higher jacket pressure ratings (e.g., above 6 bar) require metallic or PTFE gaskets and ANSI B16.5 flanges with appropriate ratings (150# or 300#). This ensures leak-free operation under thermal stress. We advise checking gasket compression during jacket testing.
What’s the difference between jacketed reactors for batch vs continuous processes?
In batch processes, jacketed vessels are designed for variable temperature control, longer residence time, and frequent cleaning (CIP/SIP). For continuous flow reactors, the jacket is optimized for constant media flow, faster heat exchange, and minimal downtime.
How does surface finish impact CIP/SIP performance in jacketed reactors?
Mirror-polished surfaces (Ra ≤ 0.4 µm) significantly enhance cleanability in CIP/SIP systems, reducing biofilm formation and particle retention. For pharma-grade jacketed reactors, we recommend electropolished internal finishes for compliance and hygiene.
Can you provide ASME Section VIII certification for jacketed reactor vessels?
Yes, we offer ASME Section VIII, Div 1 certified SS jacketed reactor vessels, complete with U-stamp documentation and hydro/pneumatic testing. This is especially useful for exports or installations in regulated industries.
How to select jacket thickness for high-pressure steam application?
For steam above 6 bar, we typically recommend:
Limpet coil thickness: 3–4 mm
Shell thickness (jacket side): as per ASME code
Proper stress analysis and corrosion allowance are also included in our design.
Selecting the right SS jacketed vessel is more than just a technical decision — it’s about ensuring thermal efficiency, long-term durability, and process reliability. From understanding the types of jacketed vessels to avoiding common selection mistakes, we’ve covered everything you need to make an informed decision.
Here’s a quick recap:
✅ Know the difference between Limpet Coil and SS Jacketed Vessels
✅ Avoid sizing, material, and thermal calculation mistakes
✅ Follow smart maintenance & cleaning practices for extended life
✅ Choose a trusted manufacturer like SV Industries with in-house fabrication and certified processes
Ready to move forward?
👉 Visit our SS Jacketed Vessel Product Page to view:
📊 Technical specs
📉 Performance charts
📩 Quick RFQ submission
Or explore our complete product range to discover compatible equipment like:
Have questions? Our Contact Us team is just a click away.