Limpet Coil Reactor Vessel Manufacturer in India
At SV Industries, we are a trusted manufacturer and supplier of Limpet Coil Reactor Vessels in India, delivering precision-engineered solutions for the most demanding industrial applications. With decades of experience and a modern fabrication unit in Ahmedabad, Gujarat, we specialize in custom-built SS reactor vessels designed for efficient heat transfer, durability, and ease of maintenance.
Our Limpet Coil Reactors are widely used in industries like pharmaceuticals, chemicals, food processing, agrochemicals, and specialty resins, where precise temperature control is critical. Every vessel is fabricated using premium-grade stainless steel (SS304, SS316) or custom materials, and thoroughly tested for pressure, weld quality, and performance.
Whether you require a steam-based heating system or a cooling loop using chilled water or oil, our reactors are tailored to your process needs with optional add-ons like agitators, CIP nozzles, and thermal insulation jackets.
📩 Looking for a quote or have technical queries?
Get in touch via our Contact Page or request a custom design for your process needs.
Design and Customization Options Available
At SV Industries, we offer custom-built Limpet Coil Reactor Vessels engineered to suit your exact process requirements. Whether you’re scaling up batch size, changing heating media, or working with specialized raw materials, our expert team ensures each reactor is tailored with the right size, material, and coil configuration for optimal performance.
Our customization capabilities are ideal for chemical, pharmaceutical, food processing, and resin-based applications that demand strict temperature control, safety, and process adaptability.
📐 Volume Capacity Options
We manufacture reactors in a wide range of capacities to suit small to large-scale production:
100 Liters to 25,000 Liters+
Available in vertical and horizontal orientation
Designed with or without agitator assembly depending on process type
Volume options are ASME or GMP-compliant, and pressure-rated based on process load.
🔄 Coil Type Configuration: Half-Pipe vs Full-Pipe
We provide two coil formats based on heat transfer needs and media pressure:
Half-pipe coils: Most common, cost-effective, and easier to maintain
Full-pipe coils: For high-pressure applications and higher heat transfer surface area
Both coil types can be designed for:Single coil (heating or cooling)
Double coil (dual-zone heating & cooling)
Our coil welding follows DIN/ASME standards with 100% radiographic testing on request.
🛠️ Material of Construction (MOC)
Based on chemical compatibility and process temperature, we offer:
SS304 / SS316 / SS316L – For high-purity, pharma, and corrosive environments
Mild Steel (MS) – For non-corrosive media and cost-sensitive processes
Alloy steel or custom cladded MOCs – Available for special applications (e.g., HCl, HBr)
Refer to our Material Compatibility Chart for guidance on choosing the right grade.
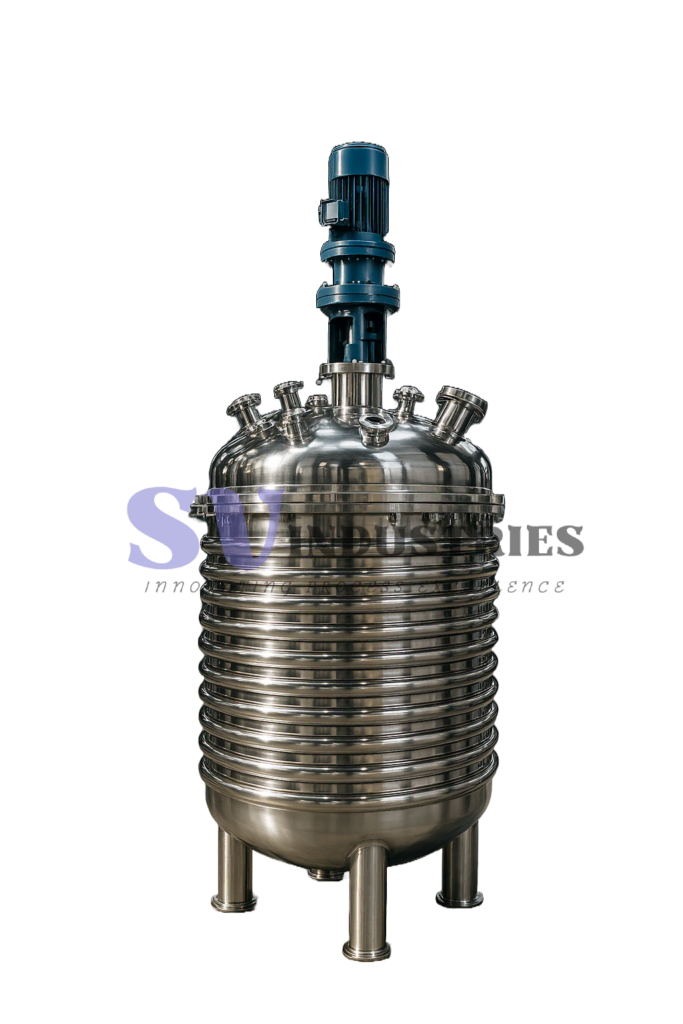
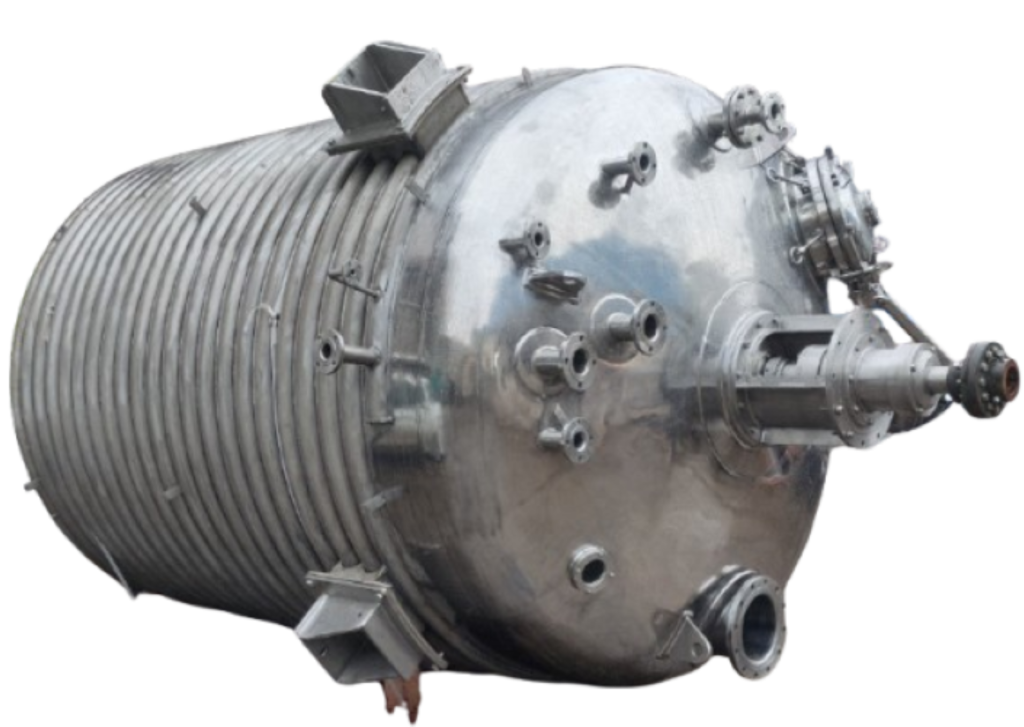
⚙️ Agitation Power Requirement Based on Reactor Volume
Proper agitation is key for homogeneous mixing, heat distribution, and reaction efficiency. As the reactor volume increases, the power required by the agitator motor also rises. The chart below demonstrates this relationship for standard liquid mixing in industrial reactors:
📌 Example Observations:
1 kL reactor typically requires 1.5 HP motor
5 kL system needs 7.5 HP
10 kL unit demands up to 15 HP depending on viscosity
This helps engineers with:
Agitator sizing during plant design
Power load estimation
Mixing performance validation
🔧 Need help selecting the right agitator for your process?
Speak to our technical team →
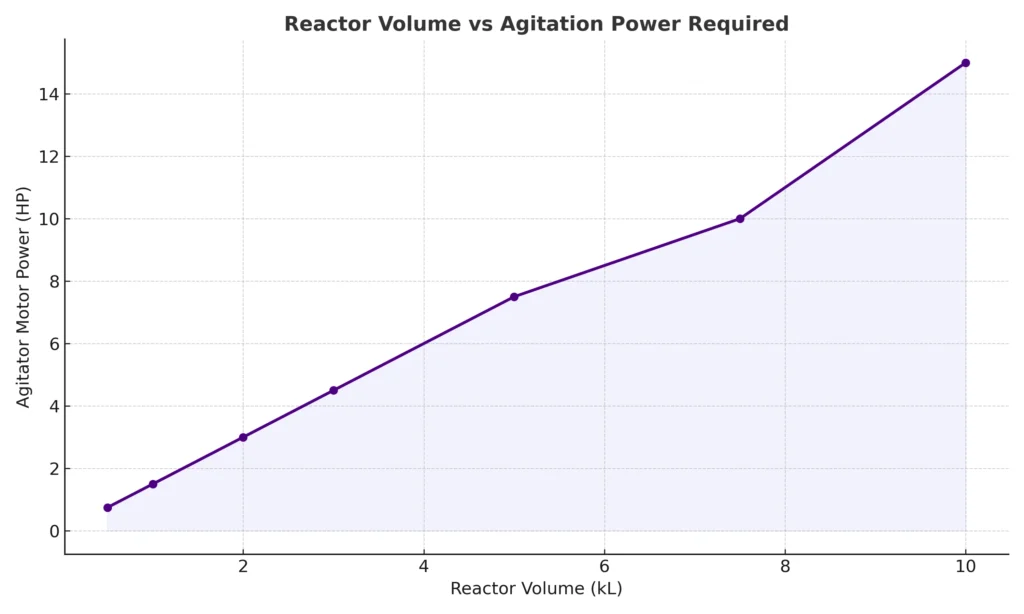
📏 Heat Transfer Area vs Reactor Capacity – Accurate Coil Sizing Guide
Proper limpet coil sizing ensures uniform heat transfer and batch consistency. A common mistake is underestimating the heat transfer surface area required per unit of reactor volume, leading to uneven heating or slow cooling cycles.
This chart provides a practical reference showing how heat transfer area must increase with reactor capacity to maintain optimal thermal performance. It’s a valuable guide for selecting or designing reactors with the right coil layout and coverage.
Heat Transfer Area vs Reactor Capacity
When designing a limpet coil reactor, accurate sizing of the heat transfer surface is essential for thermal efficiency. This chart highlights how the heat transfer area increases proportionally with reactor volume.
For example:
500 L reactor typically has ~0.9 m² coil area
5000 L reactor may need ~6.5 m² coil area
This sizing benchmark helps engineers and process designers calculate the optimal coil length, pipe diameter, and surface requirement for specific capacities.
🧠 Smart Sizing = Better Thermal Control
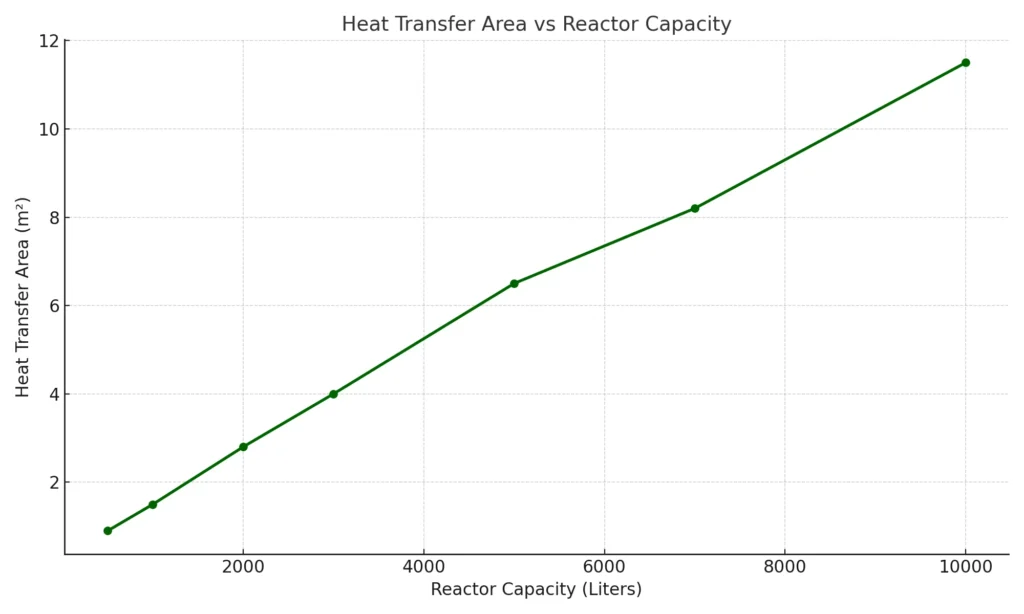
Technical Specifications and Material Grades of Limpet Coil Reactor Vessel
When selecting a Limpet Coil Reactor Vessel, engineers and process designers must consider precise technical details to ensure safe, efficient, and long-lasting operation. At SV Industries, every reactor is fabricated according to the project-specific thermal load, pressure range, and chemical compatibility — backed by high-grade materials and certified welding standards.
📊 Standard Technical Specifications
Parameter | Standard Range / Option |
---|---|
Volume Capacity | 100 Liters to 25,000 Liters |
Design Pressure | Up to 10 bar (custom up to 25 bar) |
Operating Temperature | -20°C to 250°C |
Coil Thickness | 3 mm to 8 mm |
Reactor Shell Thickness | 4 mm to 14 mm |
Agitation Speed | 20 – 200 RPM (depends on process) |
Flange Size | DN 50 to DN 600 |
Manhole & Nozzle Ports | Custom layout based on P&ID |
Coil Type | Half-pipe / Full-pipe (Single or Double) |
Finish | Mirror / Matt / Internal Electro-polish |
Testing | Hydro, Radiography, Pneumatic, Dye Pen. |
📎 Note: All specifications are customizable for GMP or ASME compliance.
🧱 Material Grades & Usage
We offer a wide range of Material of Construction (MOC) to meet diverse process requirements:
Material | Application Use Case |
---|---|
SS304 | Standard for food, pharma, non-corrosive chemicals |
SS316 / SS316L | Highly corrosion-resistant, used for acidic media |
Mild Steel (MS) | Cost-effective for non-reactive or solvent-based processes |
Cladded SS-MS | Outer mild steel with inner SS lining — budget + protection |
Hastelloy / Alloy 20 | For high-chloride or exotic chemical resistance |
For more, refer to our full Chemical Process Reactor and Industrial Chemical Reactor pages.
🧪 Material Compatibility Chart for Reactor Manufacturing
Choosing the correct Material of Construction (MOC) is essential to prevent corrosion and ensure process safety. The chart below shows the chemical compatibility of common media with three popular materials used in limpet coil reactor vessels: Mild Steel (MS), SS304, and SS316.
✅ Key Observations:
MS is only compatible with non-corrosive materials like water and NaOH
SS304 can handle most organics and diluted acids
SS316 offers the highest corrosion resistance, ideal for HCl, sulfuric acid, and aggressive solvents
This table helps:
Chemical buyers select proper grade
Avoid long-term corrosion issues
Reduce maintenance and downtime
🧠 Still unsure which MOC suits your chemical?
Get expert recommendation →
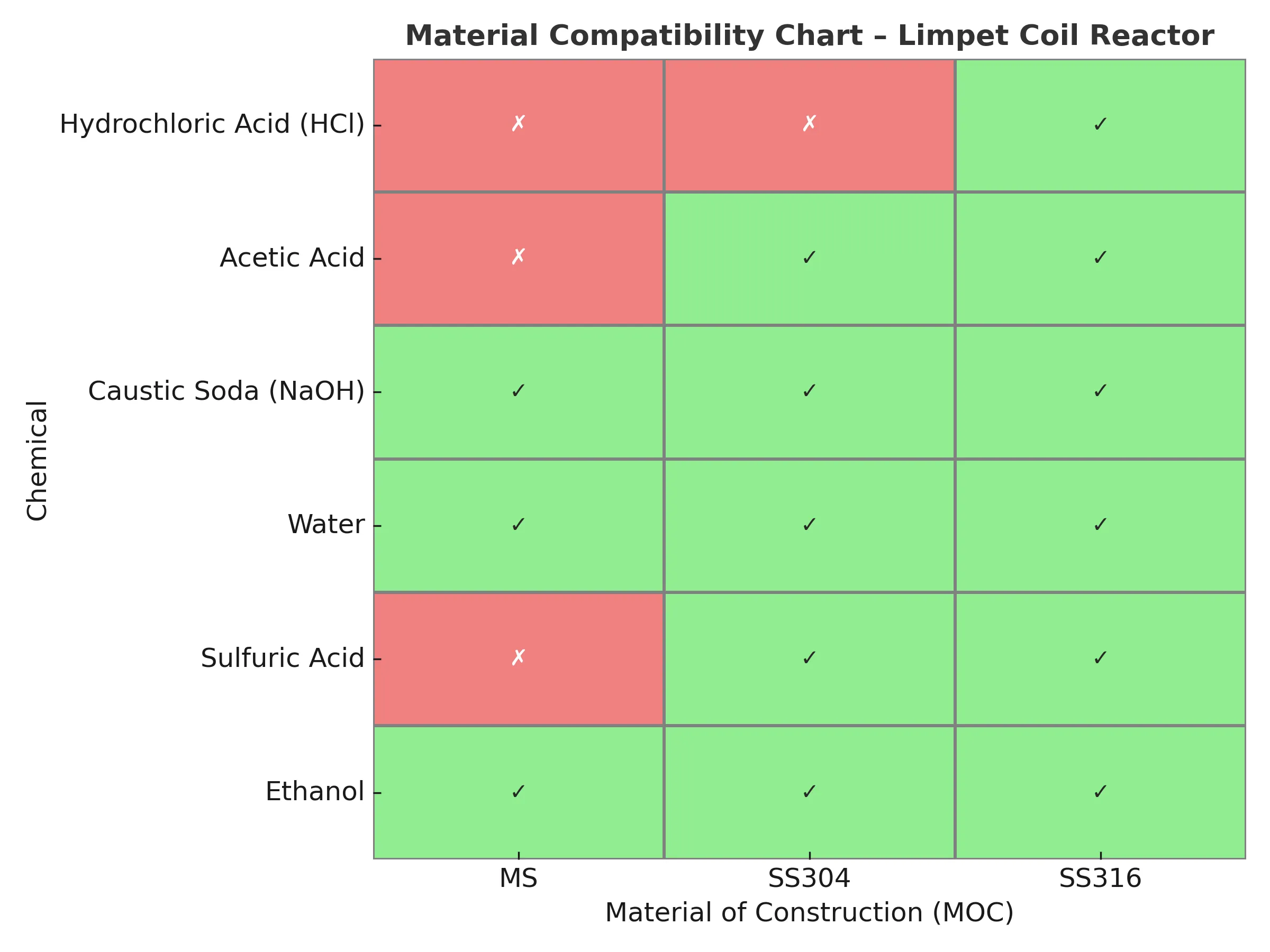
⚡ Temperature Uniformity Across Reactor Zones
Achieving consistent temperature control inside a reactor vessel is essential for high-quality batch processing — especially in pharmaceuticals, specialty chemicals, and food industries. Poor uniformity can cause hotspots, incomplete reactions, or product degradation.
The chart below shows temperature readings at various reactor locations (top, middle, bottom) to illustrate how limpet coil design ensures even thermal distribution across the batch.
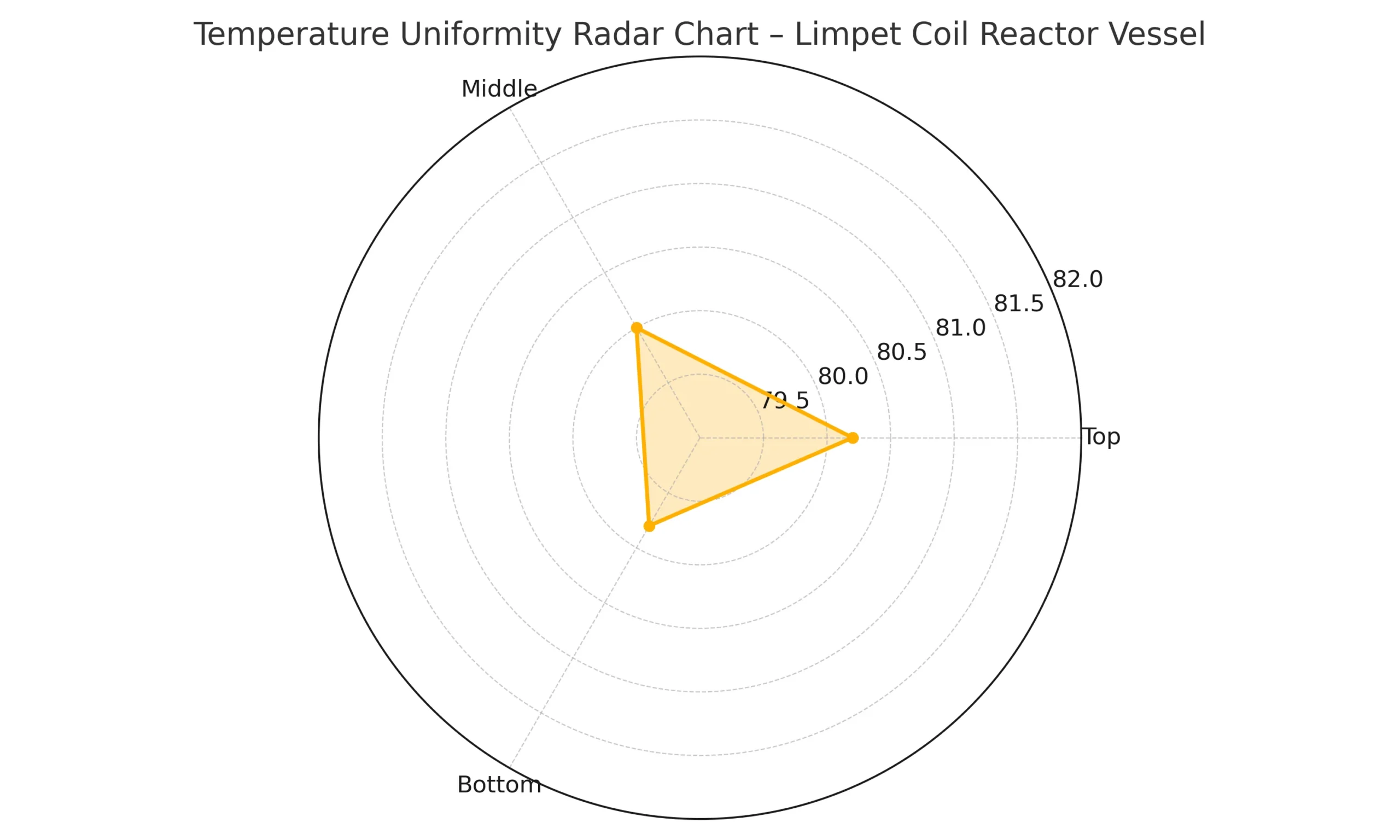
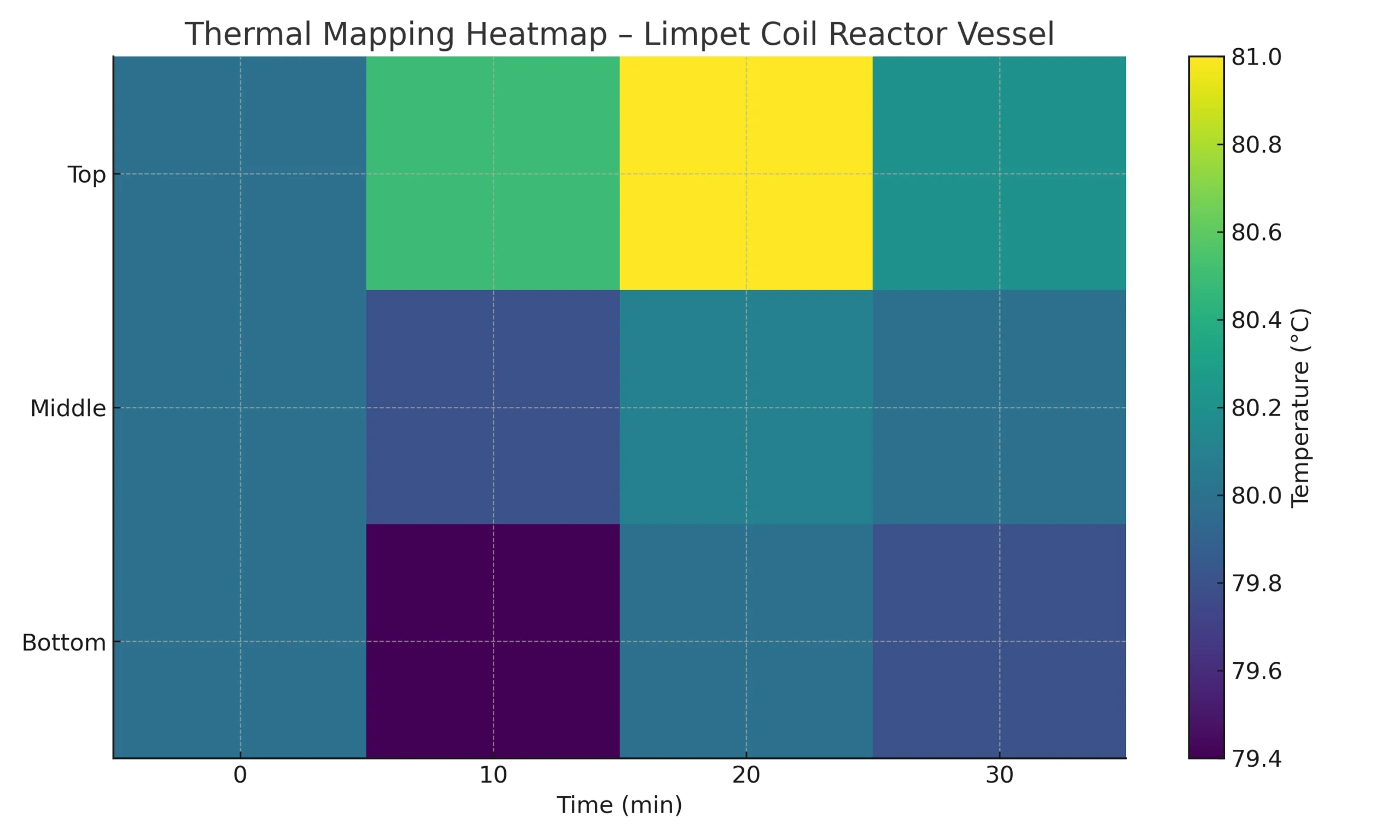
📌 What This Chart Reveals
Achieving a perfectly balanced limpet coil temperature distribution is critical when you’re running sensitive or strongly exothermic reactions. The radar chart below condenses 30‑minute steady‑state data into a simple visual triangle: the top, middle and bottom zones all sit within a razor‑thin ±0.2 °C band. The accompanying heat‑map tracks the same positions every 10 minutes and never shows a variance greater than 0.6 °C.
This thermal mapping confirms that SV Industries’ limpet‑coil architecture transfers heat uniformly along the full height of the reactor shell, eliminating hot‑spots, protecting catalysts and reducing batch‑to‑batch deviation. Whether you’re scaling a pilot recipe or running a high‑volume pharma intermediate, you can trust our vessels to keep your reaction window locked in. Explore the charts, download the raw data above, and chat with our applications team to map your own process parameters today.
Key Features & Performance Advantages of Limpet Coil Reactor Vessel
At SV Industries, our Limpet Coil Reactor Vessels are engineered not just for capacity — but for performance, safety, and process efficiency. With years of field experience and feedback from chemical, pharma, and food plants across India, we’ve continuously refined our design to deliver superior thermal control, higher energy savings, and safer operation.
⚡ Faster Heat Transfer Efficiency
Our limpet coils are designed to provide maximum surface area contact between the heating/cooling media and the reactor wall. This ensures:
Rapid heating and cooling cycles
Consistent temperature distribution
Reduced batch time, boosting production efficiency
With optimized coil pitch and flow direction, your media flow remains turbulent — essential for faster thermal exchange.
🌡 Better Temperature Zone Control
Different reactions require precise thermal zoning — especially in multi-stage or exothermic processes. Our reactors support:
Dual coil zones (top and bottom independently controlled)
Multi-inlet ports for media distribution
Real-time thermal regulation using sensor-based control
This leads to tighter process control, reduced energy consumption, and higher product consistency.
🛡 Pressure and Leakage Safety
SV Industries prioritizes safety by design:
Our limpet coils are 100% radiography tested for cracks and porosity
Designed to withstand internal pressures up to 10 bar
Coil inlet/outlet nozzles feature reinforced gussets and welding rings to avoid vibration damage
Hydro and pneumatic tests are performed before dispatch
This dramatically reduces downtime caused by leakage or weld failure, ensuring long-term operational reliability.
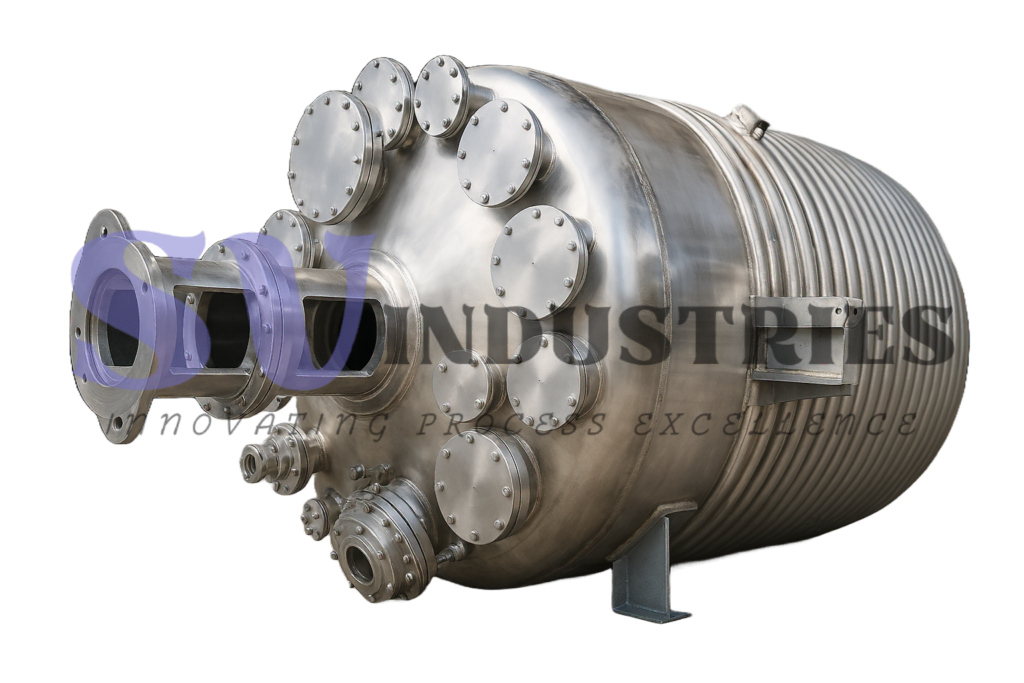
🔥 How Steam Pressure Affects Heating Speed in Limpet Coil Reactors
In limpet coil systems, steam pressure directly influences the heating rate of the process fluid. The graph below shows how increasing boiler pressure reduces the time needed to reach your target temperature:
📌 Observations:
At 2 bar, heating rate is around 4.4°C/min
At 5 bar, it reaches ~7.9°C/min
At 7 bar, peak performance of 10°C/min is achieved
✅ This data helps you:
Choose the right boiler capacity
Optimize batch heating time
Improve energy efficiency without compromising safety
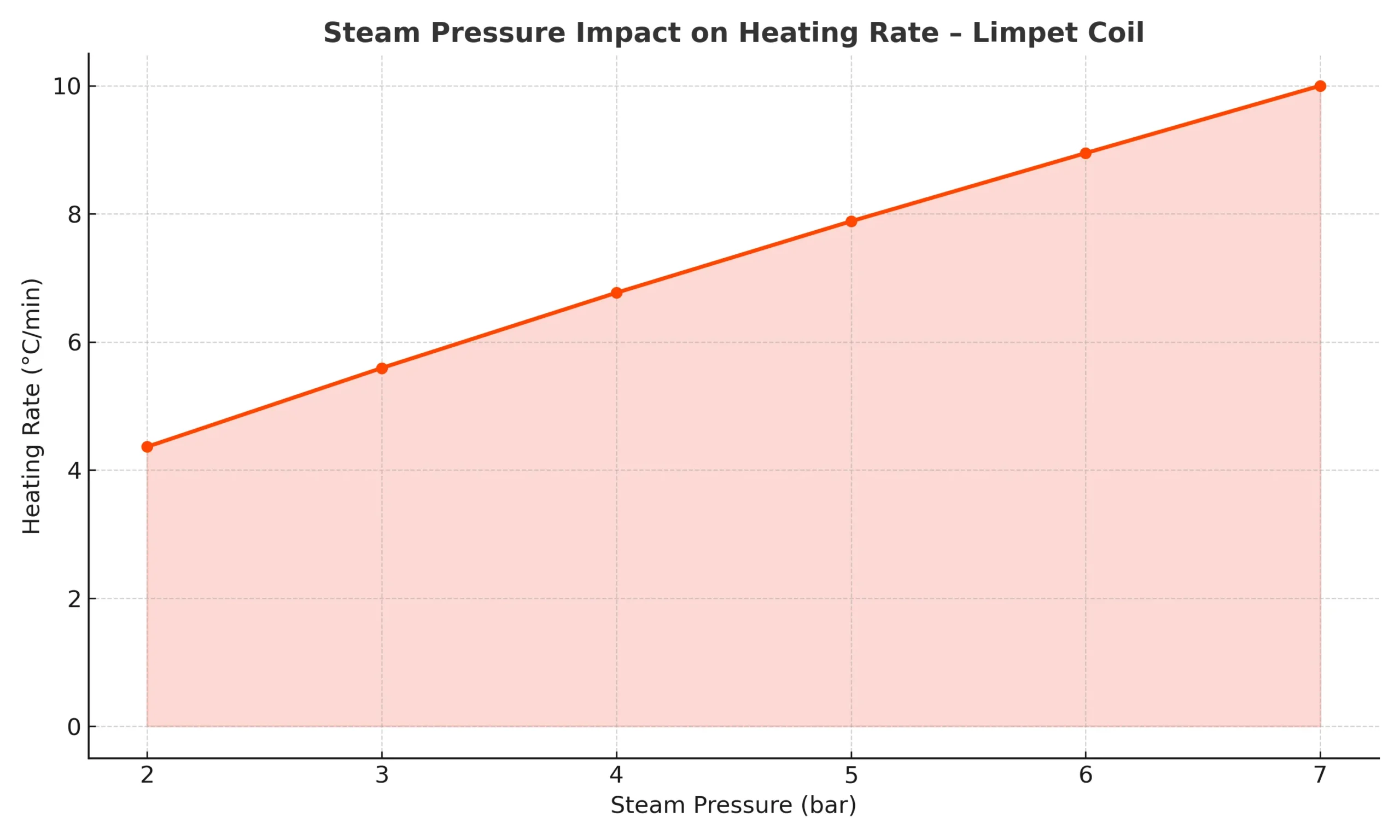
⚡ Cooling Efficiency vs Chiller Load: Optimizing Reactor Thermal Performance
Maintaining optimal reactor temperature is critical for batch consistency and product quality — especially in pharma and specialty chemical processes. This chart illustrates how chiller load affects cooling time, helping design engineers choose the right chilling system size.
By analyzing these trends, you can:
Optimize utility load planning
Minimize cycle delays during cooling
Improve energy efficiency in jacket or limpet coil-based cooling systems
This data is especially useful for:
Process engineers, utility planners, and procurement teams evaluating cooling system performance in large-scale reactor operations.
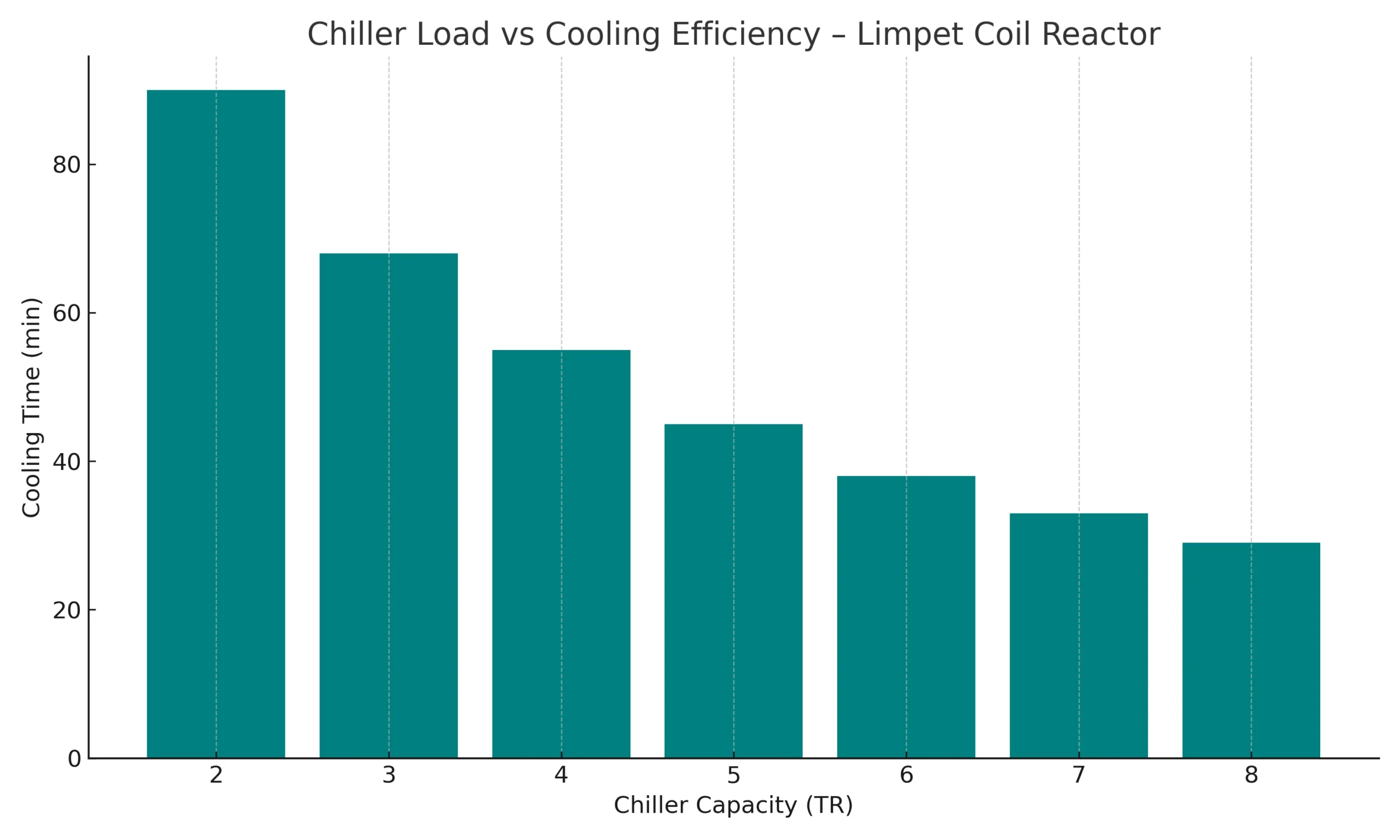
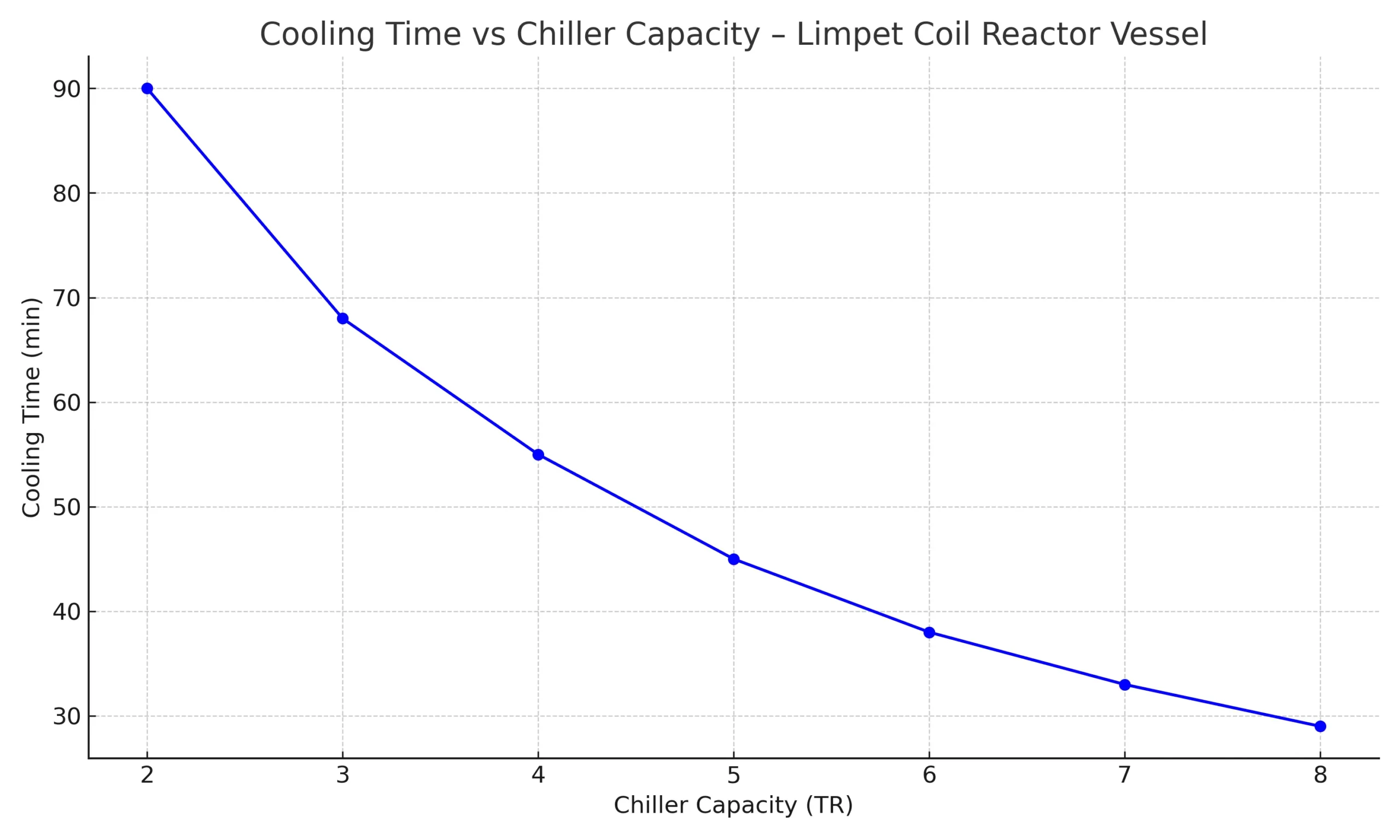
📌 Summary of Findings:
Choosing the right chiller capacity is critical to improving batch turnaround times. The graphs below demonstrate how our limpet coil reactor vessel performs when cooling a 2KL batch from 90°C to 30°C using chillers ranging from 2 TR to 8 TR.
As the chiller tonnage increases, cooling time drops significantly—from 90 minutes with a 2 TR unit to just 29 minutes with 8 TR. The line chart illustrates this trend for thermal engineers looking for predictive guidance. The bar chart makes it easy for plant heads to make quick decisions on cost-to-time tradeoffs.
This cooling efficiency study supports accurate chiller sizing in pharma, chemical, and specialty processing plants. Whether you’re scaling up or optimizing your energy footprint, SV Industries’ jacketed limpet coil design ensures responsive cooling and rapid cycle completion.
Applications Across Industries
The Limpet Coil Reactor Vessel is a cornerstone in various industrial processes that demand precise thermal control, durability, and process reliability. At SV Industries, we serve a diverse range of sectors where custom-designed reactors enable better batch consistency, safe chemical handling, and scalable operations.
Whether it’s heating viscous resins or cooling reactive pharmaceutical intermediates, our reactors are built to perform under demanding conditions.
🏭 Where Our Limpet Coil Reactors Are Used
Industry | Application Examples |
---|---|
Pharmaceuticals | API synthesis, crystallization, solvent recovery |
Agrochemicals | Pesticide formulation, herbicide production |
Paints & Resins | Resin cooking, pigment dispersion |
Specialty Chemicals | Fine chemical synthesis, reaction processes requiring thermal cycling |
Food Processing | Flavor extraction, sauce processing, fermentation |
Dyes & Pigments | Dye intermediates, slurry agitation under heat |
Petrochemicals | Additive blending, oil refining |
Biotech & Enzymes | Controlled fermentation, enzyme reactions |
📎 Note: We also cater to pilot plant setups, research labs, and OEM system integrators across India.
Why Choose SV Industries as Your Limpet Coil Reactor Manufacturer?
When it comes to critical process equipment like Limpet Coil Reactor Vessels, you need a partner that brings more than just fabrication. At SV Industries, we blend engineering expertise, in-house infrastructure, and decades of experience to deliver reactors that meet industry standards and exceed expectations.
🏆 Experience & Expertise That Counts
With over a decade of serving India’s pharmaceutical, chemical, and process industries, we’ve developed a deep understanding of what engineers and plant managers require — from heat transfer optimization to pressure safety and everything in between.
Explore our full Agitator and Reactor Range for more advanced designs.
✅ Quality Control & Rigorous Testing
Each reactor undergoes hydro testing, welding inspection, and leakproof validation. We follow ISO-based SOPs to ensure every product shipped from our plant is reliable, durable, and process-ready.
See our recent projects in our Gallery section.
🏭 Ahmedabad-Based Factory with In-House Fabrication
All equipment is manufactured at our Ahmedabad, Gujarat facility using modern tools like CNC plasma cutting, automatic welding systems, and surface finishing stations. This in-house setup allows for faster lead times, customization, and tight quality control.
Read more about our manufacturing strengths on the About Us page.
🔧 After-Sales & Technical Support
Our commitment doesn’t end with delivery. We offer installation guidance, technical documentation, and remote support to ensure smooth integration into your plant. Whether it’s a jacketed vessel, agitator, or a custom-built reactor, our Contact Us team is always ready to assist.
Frequently Asked Questions (FAQs) about Limpet Coil Reactor Vessel
What is a Limpet Coil Reactor Vessel?
A Limpet Coil Reactor Vessel is an industrial unit designed for controlled heating and cooling using external limpet coils. It ensures precise temperature regulation for various chemical reactions.
What industries use Limpet Coil Reactor Vessels?
They are widely used in pharmaceutical, chemical, petrochemical, food processing, and dye industries.
What materials are used for manufacturing Limpet Coil Reactor Vessels?
We use SS 304, SS 316, SS 316L, mild steel, and alloy steel, depending on industrial requirements.
What are the advantages of a Limpet Coil system?
It offers uniform heating, improved heat transfer, energy efficiency, and precise process control.
What capacities are available for Limpet Coil Reactor Vessels?
We manufacture reactors ranging from 100 liters to 20,000 liters.
What is the difference between a Jacketed Reactor and a Limpet Coil Reactor?
A Jacketed Reactor has a full outer shell for temperature control, while a Limpet Coil Reactor uses external coils for heating/cooling.
Can Limpet Coil Reactors handle high-pressure applications?
Yes, we design reactors for low, medium, and high-pressure operations.
What heating/cooling mediums are used?
Steam, oil, water, and thermic fluid are commonly used.
Do you offer customization options?
Yes, we customize capacity, material, coil type, agitator, and control systems as per client needs.
Your Trusted Partner for Limpet Coil Reactor Solutions
When it comes to precision-engineered limpet coil reactor vessels, SV Industries stands out as a trusted manufacturer and supplier across India. From customized designs, CIP-friendly construction, to technical charts and performance insights, we ensure every aspect of your reactor matches the highest process, safety, and quality standards.
Whether you’re from pharmaceuticals, chemicals, food processing, or specialty industries, SV Industries delivers:
✅ Decades of fabrication expertise
✅ In-house machining, polishing, and QC
✅ On-time delivery & service support
✅ Fully compliant with ASME & GMP guidelines
📩 Ready to Get a Quote?
Start your project with confidence.
👉 Get in Touch — Share your requirements, and our technical team will respond within 24 hours.