SS Jacketed Vessel Manufacturer in India – SV Industries
Looking for a reliable SS Jacketed Vessel manufacturer in India? At SV Industries, we specialize in designing and fabricating high-performance stainless steel jacketed vessels for a wide range of process industries. Whether you require vessels for heating, cooling, or thermal regulation, our jacketed designs offer exceptional durability, uniform heat transfer, and long operational life.
As an ISO-certified and ASME-compliant manufacturer based in Ahmedabad, Gujarat, we serve clients across India and export markets with precision-engineered, customizable solutions. Our vessels are crafted using premium-grade SS304, SS316, and SS316L materials to ensure corrosion resistance, hygienic finish, and GMP compatibility for critical applications in pharmaceuticals, chemicals, food processing, and cosmetics.
We deliver Pan India support and have become a preferred partner for clients looking for:
Made-to-order SS jacketed vessels with specific pressure, volume, and heat transfer requirements
Fast lead times and responsive technical support
Export-ready packaging and documentation
Ready to enhance your process setup with efficient jacketed vessels?
👉 Get a Quote Now or Download Our Brochure to explore our complete product line.
What is an SS Jacketed Vessel?
An SS Jacketed Vessel is a stainless steel tank designed with an external jacket to allow precise heating or cooling of the contents inside. Commonly used in chemical, pharmaceutical, and food processing industries, it ensures uniform temperature control during mixing, reaction, or storage processes. The outer jacket circulates steam, hot water, or coolant, enhancing process efficiency and product quality.
These vessels are commonly used in pharmaceutical, chemical, food, and cosmetic industries where temperature regulation is critical to the process.
There are different types of jackets, including:
Conventional Jackets (for low-pressure heating)
Dimple Jackets (for efficient thermal transfer and pressure resistance)
Limpet Coils (external coils for heavy-duty heating or cooling)
✅ Curious how limpet coil jackets compare? Check out our Limpet Coil Reactor Vessel page for deeper insights.
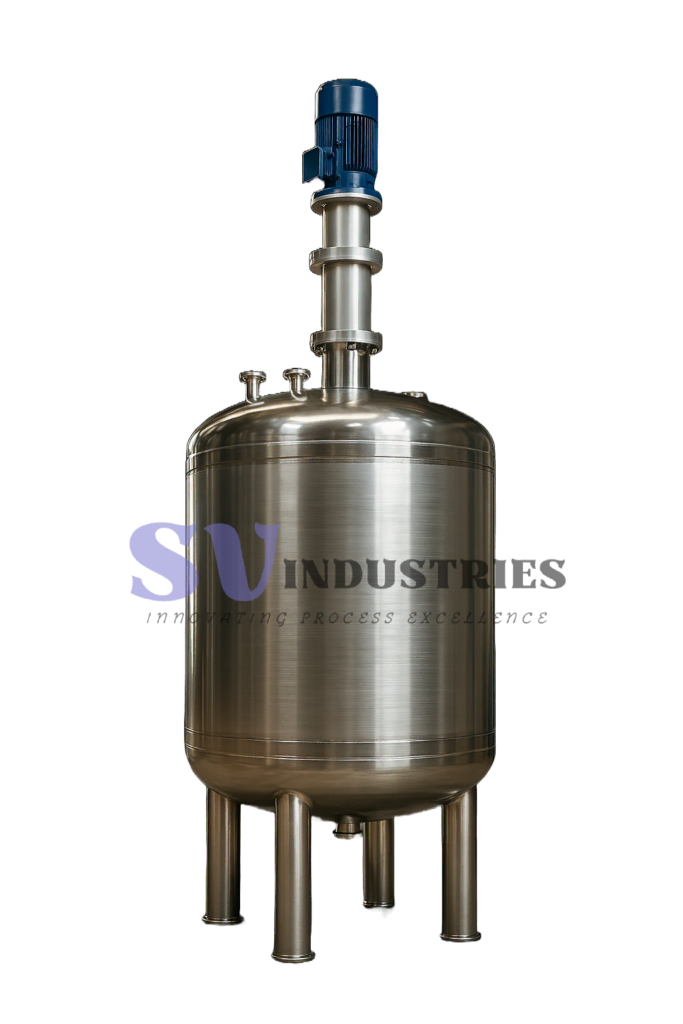
Key Features & Technical Specifications of SS Jacketed Vessels
Our SS Jacketed Vessels are engineered with a focus on durability, precision control, and process safety. Designed for use in chemical, pharmaceutical, food, and cosmetic industries, these vessels support both batch and continuous operations under a wide range of thermal and pressure conditions.
🧩 Design Features That Ensure High Performance
Each jacketed vessel is built with application-specific flexibility and robust thermal control features:
✅ Jacket Options: Available in dimple jacket, limpet coil, and conventional jacket formats
✅ Volume Range: From 100 liters to 30,000 liters, with custom sizing
✅ Pressure Rating: Upto 10 bar jacket pressure and 6 bar internal pressure
✅ Agitation System: Compatible with high-torque industrial agitators including anchor, turbine, and helical types
✅ Inlets/Outlets: Flanged or threaded ports for temperature media, pressure relief valves, sensors, and sampling
📐 Technical Specifications Table
Parameter | Specification |
---|---|
Capacity | 100 L – 30,000 L |
Material of Construction (MOC) | SS304, SS316, SS316L |
Jacket Pressure | Up to 10 bar |
Internal Pressure | Up to 6 bar |
Surface Finish | Mirror Polish, Matte Finish |
Insulation | Rockwool or PU foam (optional) |
Design Temperature | Up to 200°C |
Agitation Mount | Top/Bottom/Side |
🧪 Explore how material choice impacts performance in our Material Comparison Chart and Material Used section.
🏅 Certifications & Compliance Standards
We offer a wide range of Material of Construction (MOC) to meet diverse process requirements:
SV Industries manufactures vessels adhering to globally accepted safety and quality standards:
✅ ASME Section VIII, Div 1 – Pressure Vessel Code
✅ BIS Standards (IS 2825) for pressure and material
✅ GMP-Compliant Design for pharma-grade processing
✅ ISO 9001:2015 Certified Facility
You can verify our About Us page for a full list of certifications and infrastructure capabilities.
🧱 Pressure vs. Wall Thickness: SS 316 vs SS 304
Selecting the right wall thickness for a pressure vessel is critical for safety and compliance. This chart provides a side-by-side comparison of required wall thickness (in mm) for stainless steel grades SS 316 and SS 304 across a pressure range of 1 to 28 bar.
By analyzing this data, engineers can make informed decisions based on material choice, budget, and pressure handling capacity.
📌 Observations:
This chart shows a linear increase in wall thickness with rising pressure. Key insights include:
SS 304 requires slightly more thickness than SS 316 at every pressure level due to lower corrosion resistance and yield strength.
For example, at 10 bar, SS 316 needs 4.32 mm, whereas SS 304 needs 4.59 mm.
At 28 bar, the required thickness jumps to 12.20 mm (SS 316) and 12.97 mm (SS 304).
This information is particularly useful during pressure vessel design, helping you:
Choose between SS 304 and SS 316 depending on budget vs. performance.
Plan for material procurement and regulatory compliance (ASME/PED standards).
Avoid overdesign or under-design in reactors, jacketed vessels, and tanks.
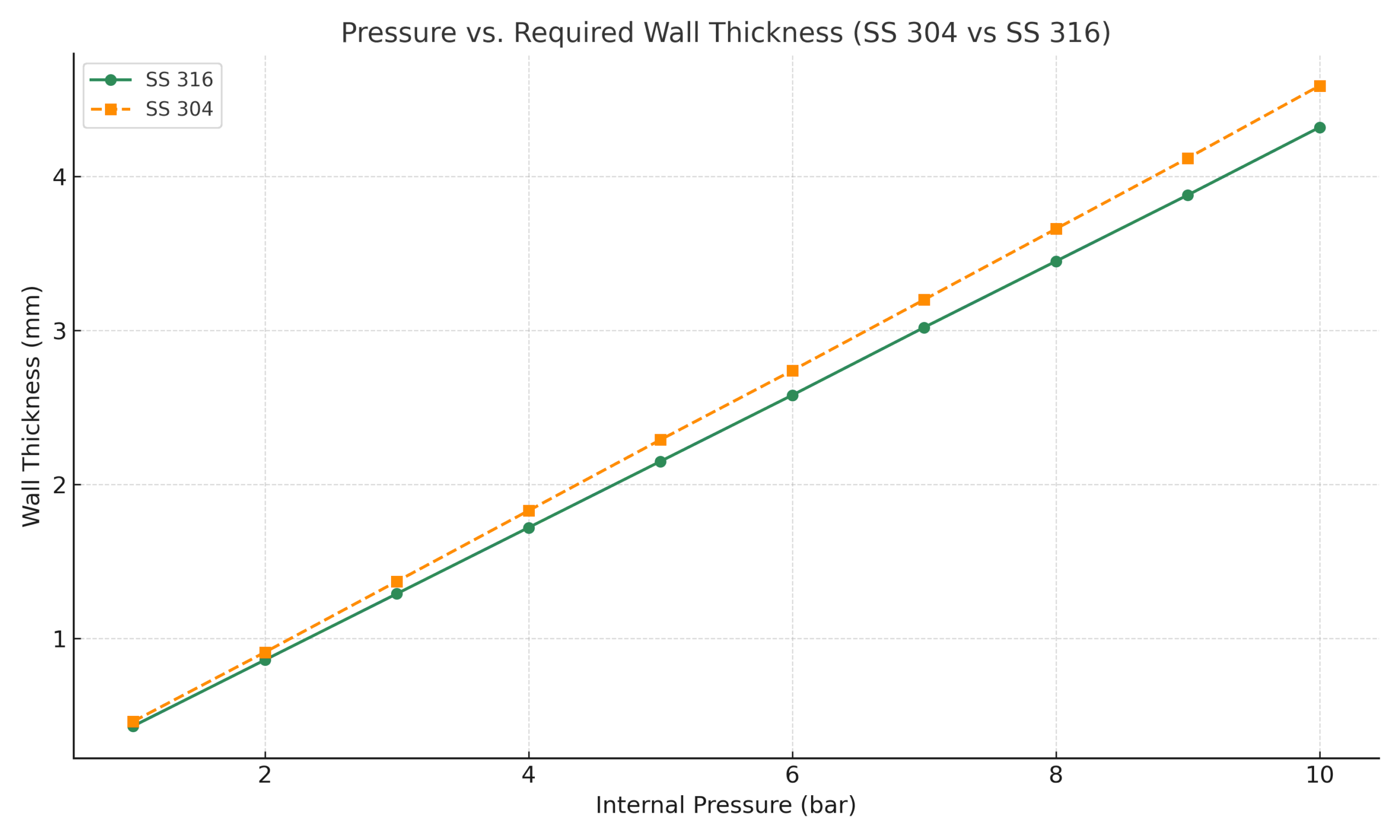
✅ BIS / ASME Design Compliance Table
Why This Matters:
When selecting a process vessel, engineers and procurement teams must ensure compliance with national and international design standards to meet safety, regulatory, and operational benchmarks. Below is a summary of key standards followed in our vessel designs:
🏷️ Design Standard | 🧾 Description | ⚙️ Applicable Component |
---|---|---|
ASME Section VIII | Pressure vessel code for mechanical integrity and safety under pressure | Shell + Jacket |
IS 2825 | Indian standard for unfired pressure vessels; often aligned with IBR guidelines | Internal Vessels |
GMP | Guidelines for hygiene, cleanability, and contamination control | Pharmaceutical-Grade Equipment |
What This Means for You:
Whether you’re sourcing vessels for regulated industries like pharma, or high-pressure systems in chemical processing, our products are engineered to meet the required codes and certifications.
✔️ Ensures legal compliance
✔️ Supports audit-readiness (FDA, IBR, etc.)
✔️ Reduces engineering risk and rework
📌 Always check compliance upfront — it saves cost, time, and regulatory hassles later.
Materials Used in SS Jacketed Vessels
At SV Industries, we manufacture SS Jacketed Vessels using high-grade stainless steel materials like SS304, SS316, and SS316L, depending on the application’s chemical compatibility, hygiene requirement, and corrosion resistance.
Choosing the right material of construction (MOC) ensures long-term durability, process safety, and regulatory compliance—especially in pharmaceutical, food, and chemical environments where contact materials must meet strict quality standards.
🧱 Comparison of Stainless Steel Grades
Material Grade | Description | Typical Use-Cases |
---|---|---|
SS304 | Economical, food-safe, good corrosion resistance | Food processing, cosmetics |
SS316 | Contains molybdenum for better resistance to chemicals | Chemicals, dyes, solvents |
SS316L | Low carbon version of 316, ideal for welding & pharma | Injectable drugs, biotech |
Each grade is chosen based on chemical exposure, temperature range, pressure handling, and hygienic requirements.
🧪 Industry-Specific Material Compatibility
Our SS jacketed vessels are compatible with:
Pharmaceuticals: Meets GMP standards, cleanable, non-reactive (SS316L preferred)
Food & Beverage: SS304 or SS316 depending on acidity/sugar content
Chemicals & Solvents: SS316 for acid, alkali, and oxidizing environments
Cosmetics & Skincare: Mirror-polished SS304 with optional sanitary seals
✅ For aggressive chemicals or CIP systems, we recommend SS316L with mirror finish.
📈 See compatibility data in the Material Compatibility Chart in the performance section.
🧪 Material Comparison: SS 304 vs SS 316
Why This Matters:
One of the most common questions buyers and engineers ask is:
“Should I choose SS 304 or SS 316 for my vessel?”
This side-by-side comparison simplifies that decision by highlighting key material differences in corrosion resistance, cost, and application suitability.
🔍 Parameter | 🧴 SS 304 | 💊 SS 316 |
---|---|---|
Corrosion Resistance | Good (general purpose) | Excellent — ideal for marine & pharma use |
Molybdenum | ❌ Not present | ✅ Yes (2–3%) — enhances corrosion resistance |
Cost | 💲 Lower | 💲💲 Higher |
Temperature Range | Up to 870°C | Up to 925°C |
Typical Use | Food processing, dairy, kitchen equipment | Pharmaceuticals, chemicals, saline environments |
What This Means for You:
If you’re operating in highly corrosive, sanitary, or coastal environments, SS 316 is worth the extra investment due to its molybdenum content and superior corrosion resistance.
For standard industrial or food-grade applications, SS 304 offers reliable performance at a lower cost.
🧠 Still unsure? We’ll guide you based on your exact process fluid and operating conditions.
Design & Customization Options for SS Jacketed Vessels
At SV Industries, we understand that every process has unique thermal, pressure, and mixing requirements. That’s why our SS Jacketed Vessels are fully customizable — designed to match your specific application needs and industry standards.
We offer a wide range of design configurations including:
Jacket Types: Dimple Jacket, Limpet Coil, and Half Pipe Coil — suitable for low to high-pressure operations
Agitator Integration: Various impeller types (Anchor, Turbine, Helical, Hydrofoil) with VFD options for controlled mixing
Capacity Range: From 100 liters to 30,000+ liters with single or multi-compartment setups
Thermal Fluid Compatibility: Supports steam, hot oil, chilled water, or glycol circulation
Pressure & Temperature Ratings: Designed for vacuum to 10 bar pressure and up to 250°C
Material & Finish Options: SS 304, SS 316, with mirror/matte finishes, electro-polishing, or internal coatings
Nozzle & Instrumentation: Inlets, outlets, manholes, thermowells, pressure gauges, sight glass, and CIP/SIP ports
Mounting Types: Leg-mounted, skirt-mounted, or skid-mounted vessels based on layout and mobility needs
Our in-house engineering team also provides custom drawings and 3D models to ensure design accuracy before fabrication. Whether you need a batch reactor, mixing tank, or storage vessel with thermal control, we deliver tailor-made solutions that meet your plant’s performance and compliance goals.
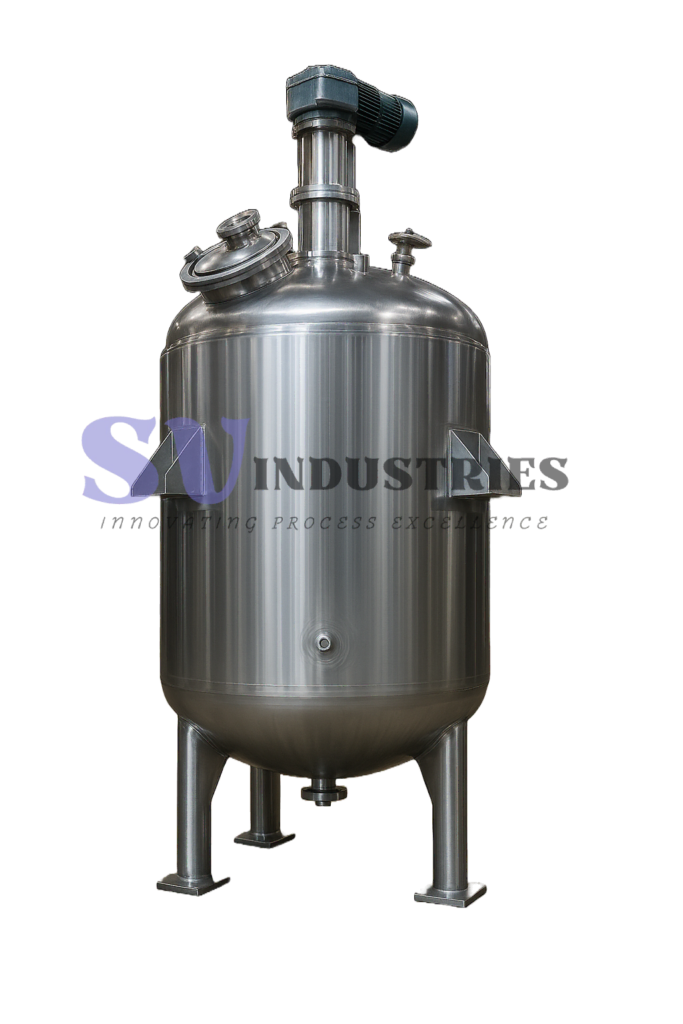
SS Jacketed Vessel Applications Across Industries
SS jacketed vessels are essential in industries where precise temperature control, hygienic contact surfaces, and process consistency are critical. SV Industries supplies custom-engineered vessels for a wide range of industrial applications — all built to meet industry-specific compliance standards like GMP, FDA, ASME, and ISO.
Below is an industry-wise breakdown of typical uses of our stainless steel jacketed vessels:
🏢 Industry | ⚙️ Typical Applications |
---|---|
🧪 Pharmaceuticals | API synthesis, crystallization, buffer preparation, solvent recovery |
🧬 Biotech | Fermentation, cell culturing, enzyme reactions |
🧫 Food & Beverage | Pasteurization, sauce cooking, dairy processing, brewing |
🧴 Cosmetics | Emulsion mixing, lotion heating, batch cream production |
🧯 Chemical | Exothermic reactions, heat-sensitive solvent processing |
🎨 Paints & Resins | Pigment dispersion, resin heating, viscosity control |
🧷 Textiles | Dye bath preparation, sizing chemical heating |
🧼 Detergent & Soaps | Slurry mixing, perfume oil blending |
🧹 Cleaning Products | Liquid disinfectant formulation, acidic/alkaline solutions |
🔬 Laboratory & R&D | Scale-up process design, material testing, controlled reactions |
📍 Need a jacketed vessel tailored for your process? Request a Custom Design now.
Benefits of SS Jacketed Vessels by SV Industries
SV Industries delivers precision-engineered SS jacketed vessels that combine performance, durability, and hygiene. Designed for demanding industrial processes, our vessels offer distinct advantages that set us apart from generic suppliers.
🔥 1. Faster Heating & Cooling Cycles
Optimized jacket surface area and fluid circulation paths enable rapid thermal exchange.
Ideal for time-sensitive batch processing and temperature-sensitive materials.
Available with limpet, dimple, or full external jacket based on your process requirements.
✅ Improves process efficiency and reduces energy consumption.
🛡️ 2. Long Service Life with Corrosion Resistance
Made using SS 304, SS 316, and SS 316L – ideal for corrosive and acidic environments.
Welded and polished using pharma-grade finishing to avoid microbial buildup.
Backed by ISO & ASME standards for mechanical integrity.
✅ Minimizes maintenance and replacement costs over time.
🧼 3. Hygienic, GMP-Compliant Design
Crevice-free interiors, sanitary fittings, and mirror polish finish.
Fully CIP/SIP compatible for pharmaceutical, biotech, and food industries.
Custom design includes spray balls, manways, and valve arrangements to aid cleanability.
✅ Supports regulatory compliance in pharma & food plants.
🛠️ 4. Assured Quality & Service by SV Industries
Built in Gujarat with export-ready infrastructure.
Full technical support including 3D layout, drawings, and validation documents.
Trusted by leading chemical, pharma, and food companies across India.
✅ Get end-to-end support from design to delivery.
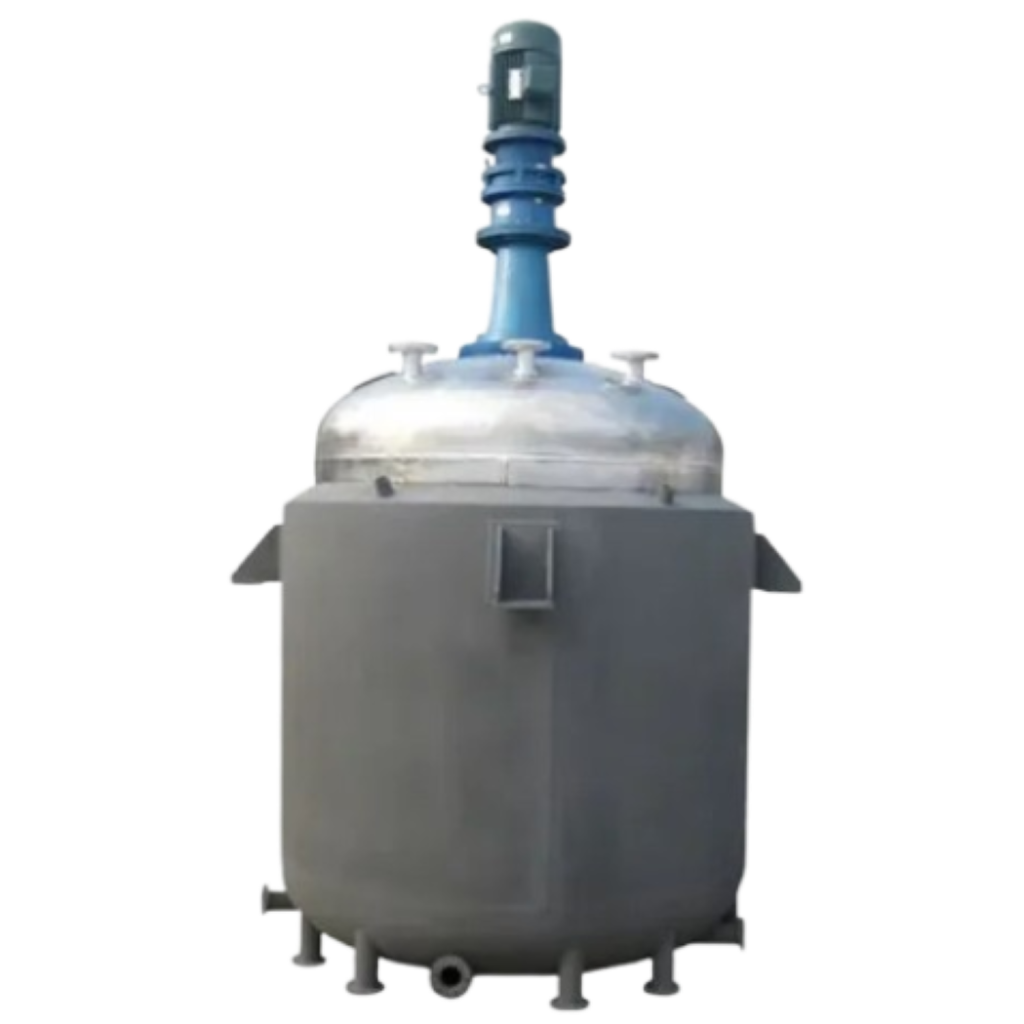
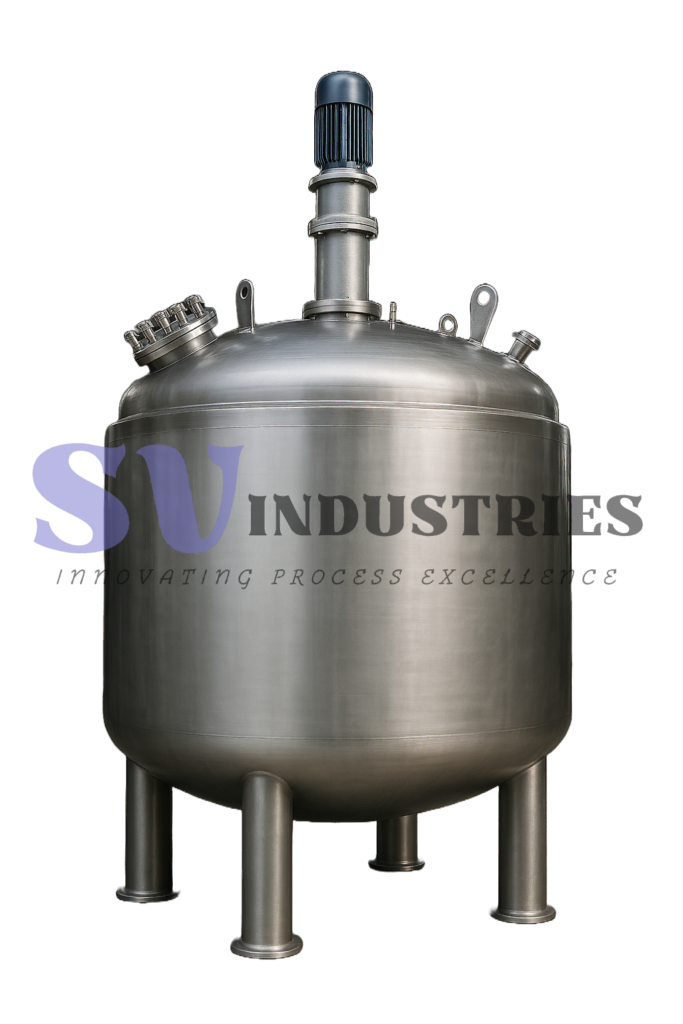
Performance Charts & Efficiency Metrics
At SV Industries, we believe in engineering transparency. To help you make informed decisions, we provide real-world performance charts based on rigorous testing of our SS Jacketed Vessels under standard operating conditions.
🔥 Heat Transfer Efficiency vs. Jacket Pressure
Optimizing jacket pressure directly improves thermal performance inside your reactor. This chart shows how increasing the jacket pressure not only raises the flow rate of the heating or cooling media but also significantly boosts the heat transfer coefficient (HTC). For process engineers, this is essential data when designing high-efficiency thermal systems for jacketed vessels.
📌 Observations:
As shown in the chart, when jacket pressure rises from 1.0 to 4.0 bar, the flow rate of heating/cooling media increases from 30 to 60 LPM, leading to a steady rise in the Heat Transfer Coefficient (HTC) from 180 to 336 W/m²·K. This directly indicates improved thermal exchange between the jacket and vessel contents. Higher HTC results in faster heating or cooling cycles, reduced energy consumption, and tighter process control — all critical for reactors operating in pharma, chemical, and food industries.
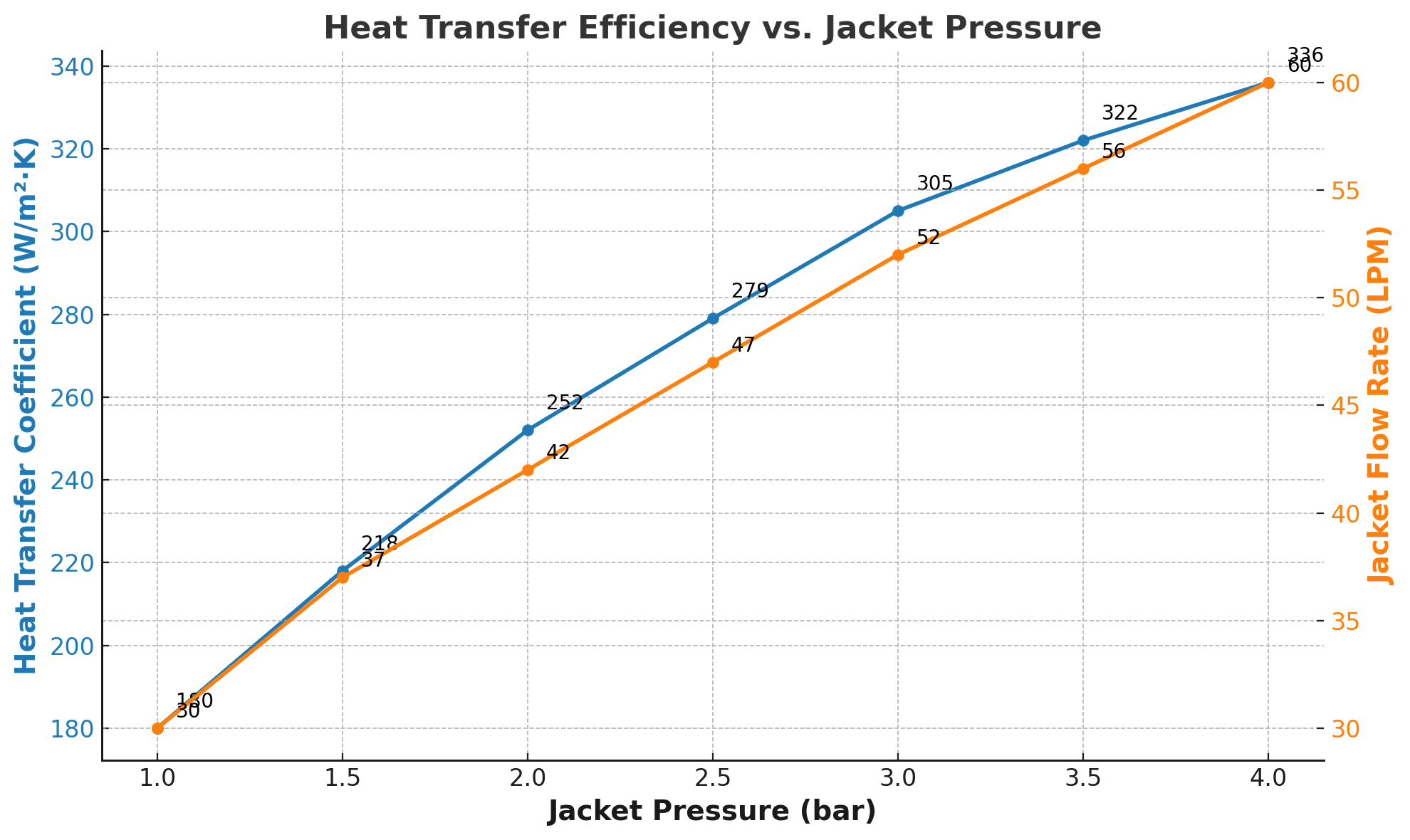
🔥 Heating Time vs. Fluid Volume
As vessel volume increases, the time required to heat the fluid also rises significantly. This chart helps process engineers and buyers estimate heating durations for different batch sizes — an important factor when planning production cycles or energy budgets in reactors or storage tanks.
📌 Observations:
As vessel volume increases, heating time doesn’t just add up — it multiplies. A small 100-liter batch reaches 80°C in just 48 minutes, but scale that up to 5000 liters, and you’re looking at a wait of 2400 minutes. This dramatic rise is due to the greater thermal mass and lower relative heat transfer surface area in larger vessels.
For process engineers, this insight is critical. It emphasizes the need to:
✅ Optimize coil or jacket design
⚙️ Choose the right utility capacity
💡 Plan production cycles efficiently
In short, bigger batches require smarter thermal strategies. Understanding this curve can help cut down cycle times and improve plant productivity.
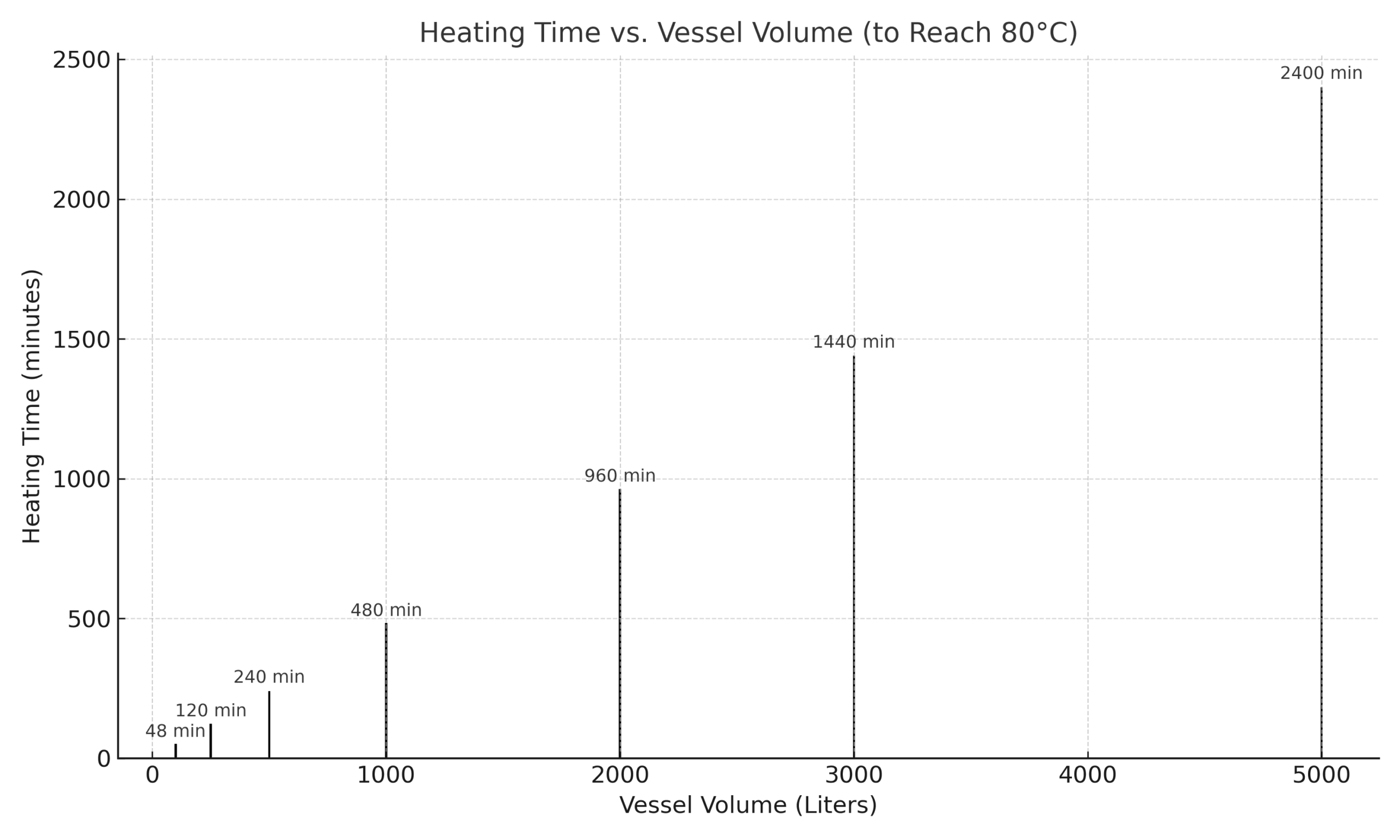
🧊 Cooling Curve: Temperature vs. Time for Water and Glycol Jackets
Understanding how cooling media impacts the rate of heat removal is essential for efficient reactor design. This cooling curve compares two widely used jacket media — Water and Glycol — over a 20-minute period. Both jackets start at 80°C and follow a cooling cycle at their respective heat transfer coefficients (HTC): Water (320 W/m²·K) and Glycol (180 W/m²·K).
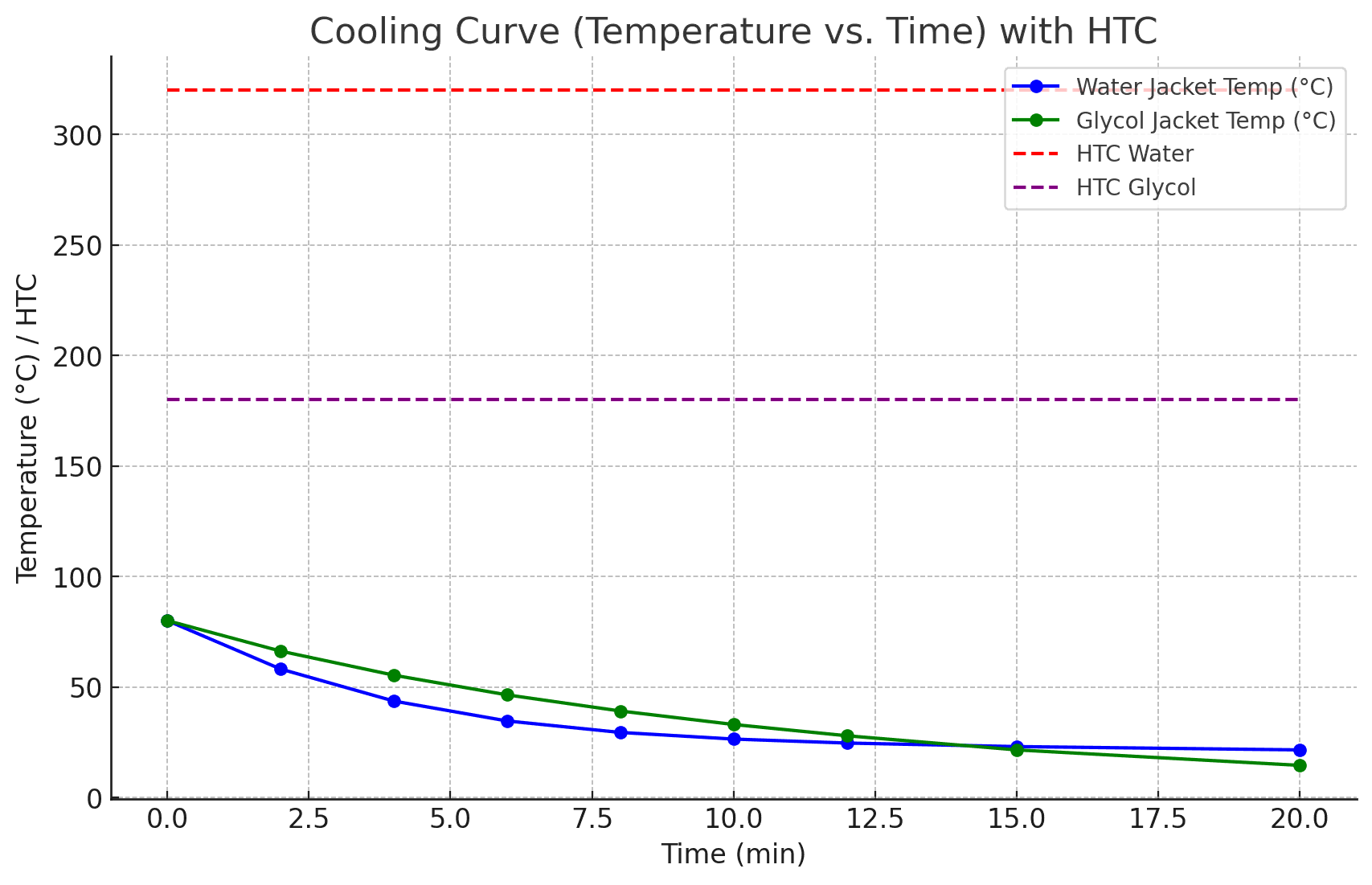
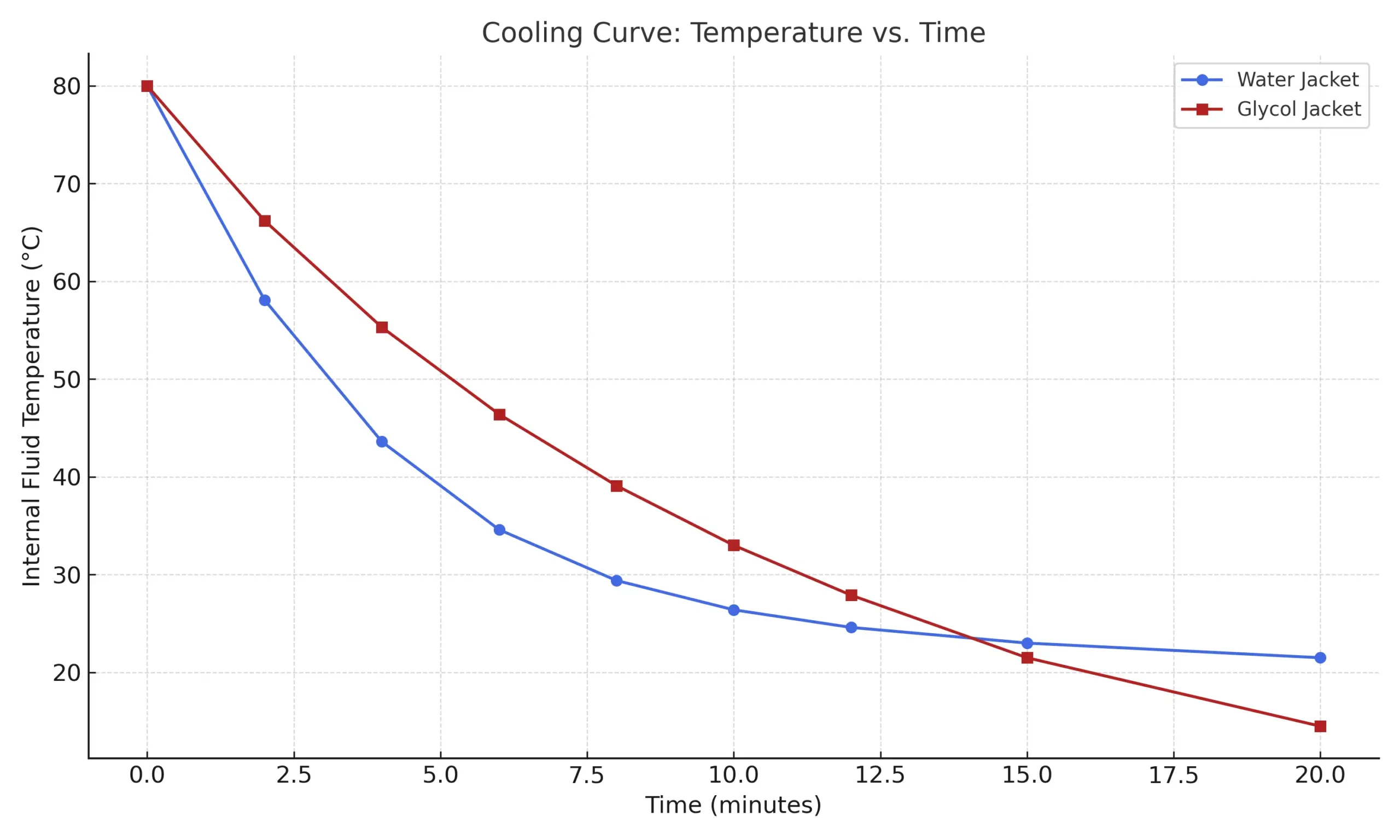
💡 Key Observations
This chart clearly demonstrates that water-cooled jackets cool the reactor contents significantly faster than glycol-cooled jackets. For instance:
At 10 minutes, water-cooled temperature drops to 26.4°C, while glycol-cooled is still at 33.0°C.
At the end of 20 minutes, water achieves near-ambient cooling (21.5°C), while glycol lags at 14.5°C, suggesting slower energy release.
This data is particularly useful when selecting jackets for time-sensitive or thermal-sensitive chemical processes. Water jackets are optimal for rapid cooling, while glycol jackets may suit gradual cooling requirements or very low-temperature operations due to their antifreeze properties.
Temperature & Mixing Performance
Consistent temperature control and efficient mixing are critical performance metrics for any jacketed vessel, especially in pharma, chemical, and cosmetics manufacturing. SV Industries’ jacketed vessels are engineered to deliver uniform thermal distribution and optimized mixing flow, reducing hotspots and enhancing product quality.
🔄 Mixing Effect on Heat Transfer Efficiency
Agitators inside jacketed vessels don’t just blend – they directly influence thermal exchange. Efficient mixing ensures the internal contents are consistently exposed to the jacket surface, improving both heating and cooling cycles.
✅ Performance Enhancers:
Anchor or helical agitators: Ideal for viscous products – ensure bottom-to-top circulation.
Baffles and flow breakers: Disrupt vortex and improve contact time.
VFD-controlled agitation: Dynamically adjusts RPM for heat-sensitive products.
📌 Example:
A 10KL batch reactor using a hydrofoil agitator achieved a 30% faster heating rate compared to a conventional paddle system, with uniformity across ±1°C.
🌍 Thermal Mapping for Uniformity Validation
We use thermal sensors and simulation tools to map temperature gradients within the vessel during operation. This helps clients visualize how well heat is distributed — even at different fill levels or process viscosities.
🔍 Thermal Mapping Includes:
Top-to-bottom temperature measurement
Wall vs centerline readings
Under agitation vs static mode comparison
📊 Typical Uniformity Range:
±1.2°C across vessel with jacketed design + slow-speed anchor agitator in a 3000L batch process.
📌 Data-backed Validation:
We provide thermal mapping data during FAT or simulation reports on request for regulated industries like pharma and biotech.
🔥 Temperature Uniformity Across Reactor Vessel
Maintaining uniform temperature inside a reactor vessel is critical for consistent product quality and efficient reactions. Uneven heating can cause issues like hot spots, incomplete reactions, or degradation of sensitive compounds.
This data shows temperature readings from six strategic points — top, mid, and bottom — both at the center and near the vessel walls.
📌 What This Means for Your Process
The temperature difference between top and bottom is minimal — just 1.7°C — which shows that your heating system, jacket design, and agitation setup are doing their job efficiently.
✅ Better batch repeatability
✅ Improved product yield and consistency
✅ Ideal for sensitive processes like crystallization, polymerization, or fermentation
📌 This kind of thermal stability isn’t just impressive — it’s essential for scale-up, GMP compliance, and long-term process reliability.
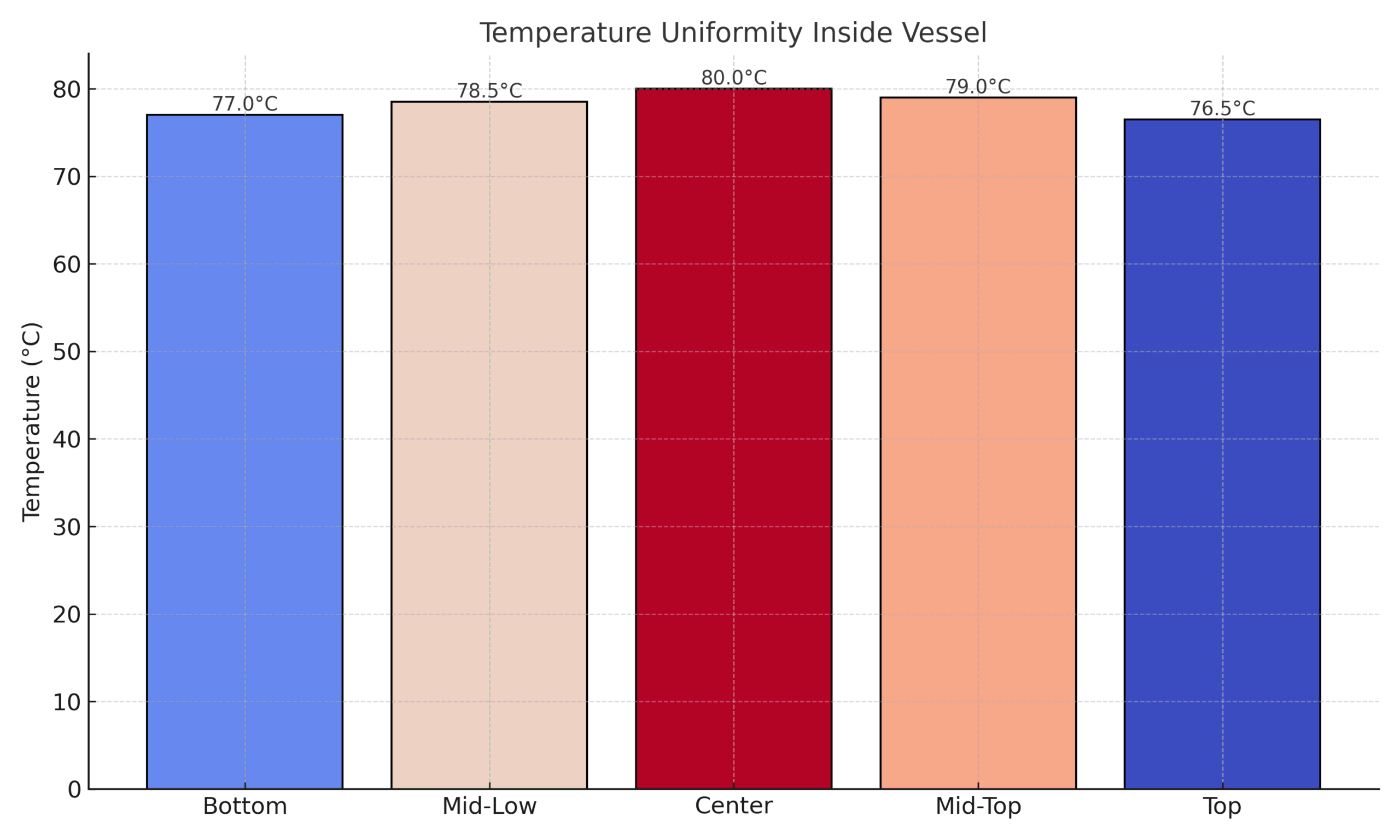
🔁 Agitator Speed vs. Heat Transfer Rate
Mounting an agitator inside a jacketed vessel can significantly improve heat transfer efficiency. This chart compares static vs. agitated heat transfer coefficients (HTC) and the resulting total heat transfer rates across various RPMs.
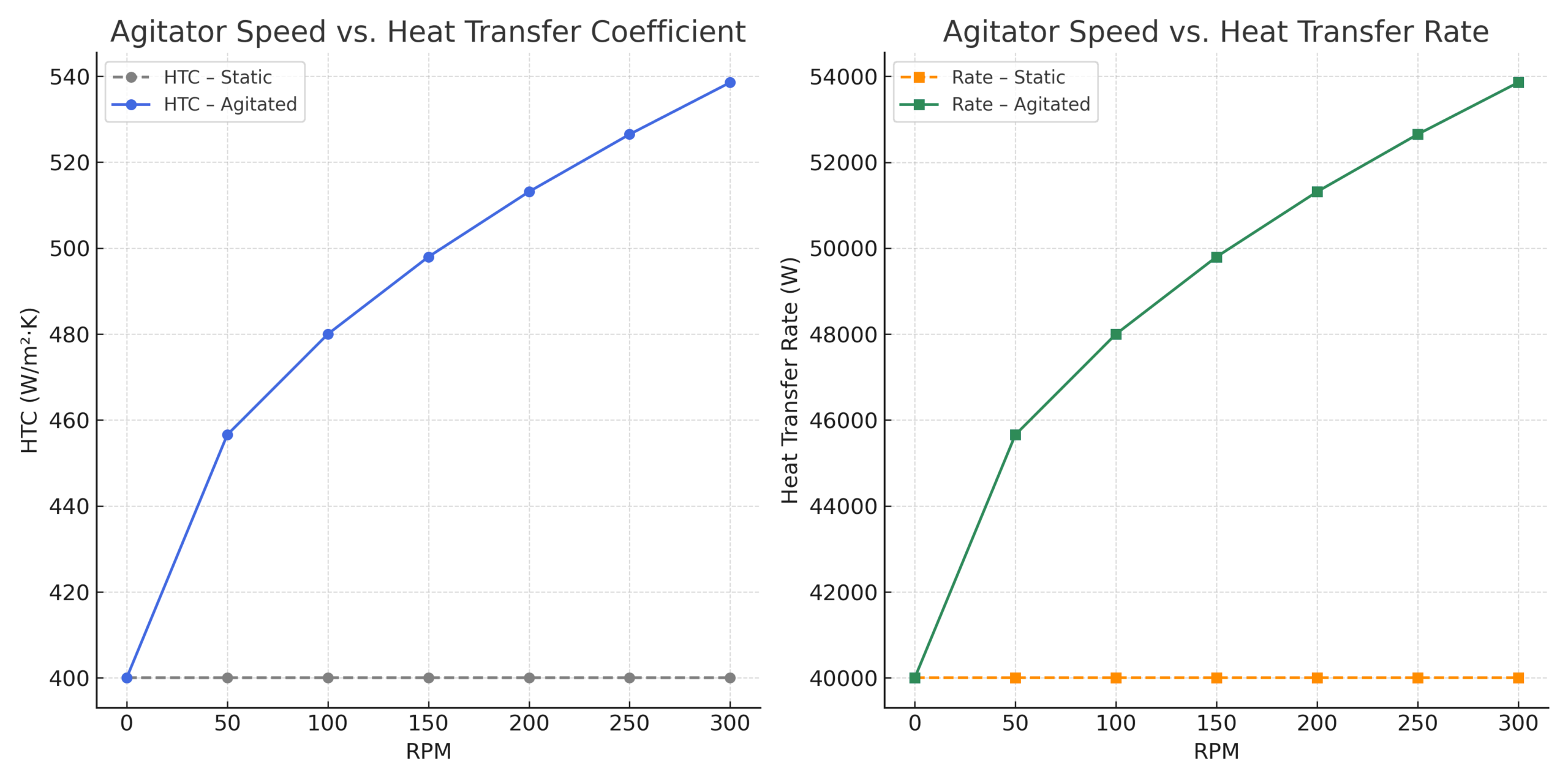
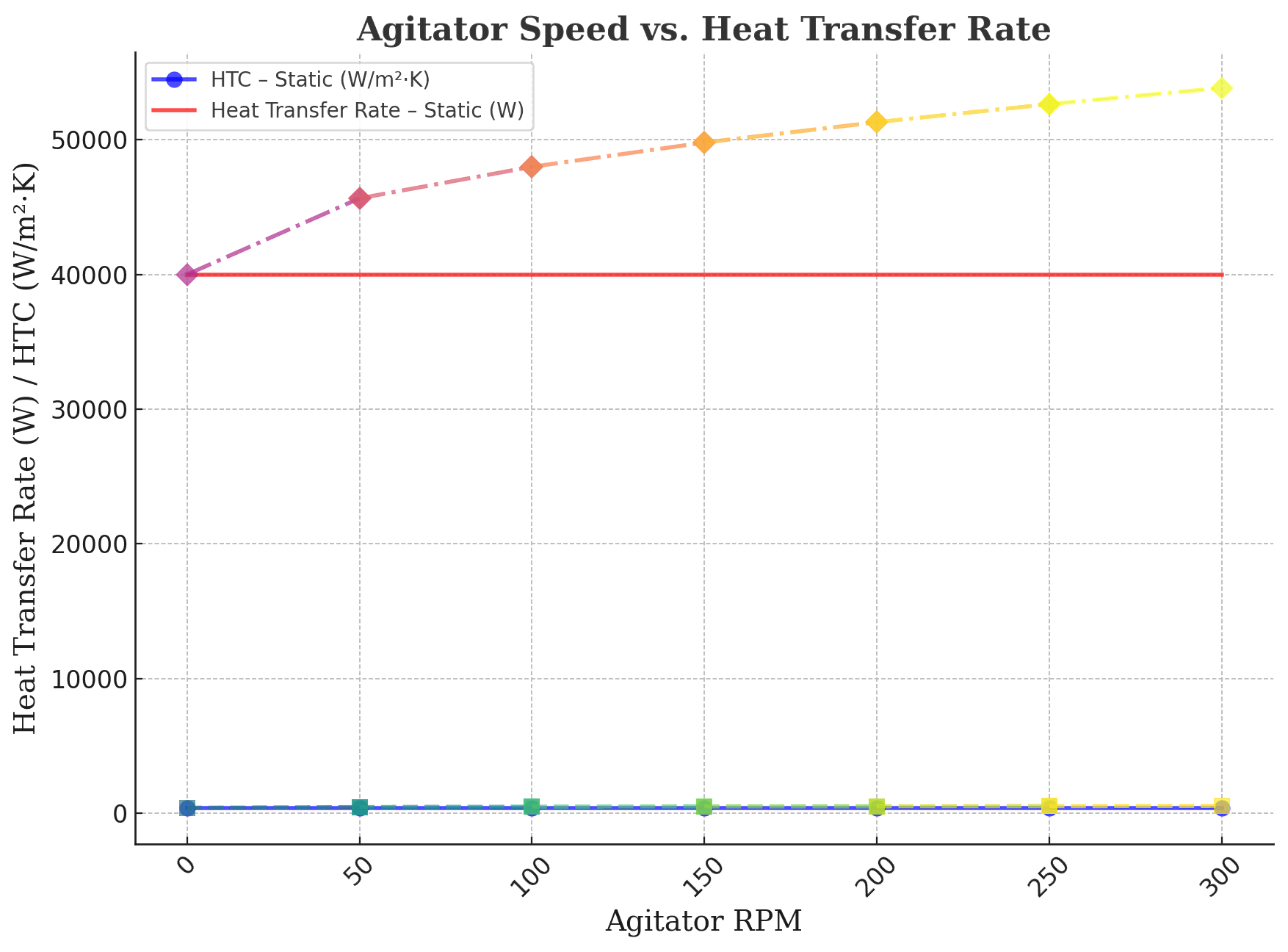
💡 Chart Explanation
At 0 RPM, the system behaves as a static jacketed vessel with 400 W/m²·K HTC.
As the agitator speed increases:
HTC improves steadily, reaching 538.56 W/m²·K at 300 RPM.
Overall heat transfer rate rises by ~34%, from 40,000 W to 53,856 W.
🔍 Key Takeaways:
Even at low RPMs like 100–150, there is a notable 20%+ gain in heat transfer.
Enhanced mixing reduces boundary layer thickness and improves surface exposure.
Helps reduce heating/cooling cycle time and ensures temperature uniformity, especially in viscous or batch processes.
Why Choose SV Industries for SS Jacketed Vessels
When you invest in an SS Jacketed Vessel, you’re not just buying a product — you’re choosing a partner for performance, reliability, and long-term value. At SV Industries, our commitment to engineering precision, customer-centric service, and end-to-end quality control sets us apart.
🏭 1. 100% In-House Manufacturing
We design, fabricate, inspect, and test every vessel in our Ahmedabad-based facility.
This in-house capability means:
Faster delivery timelines
Strict quality control at each stage
Better pricing — no outsourcing margins
Customization from 100L to 30,000L capacity with limpet, dimple, or conventional jackets
Every weld, every nozzle, every finish — done under our expert supervision.
⏱️ 2. Commitment to On-Time Delivery
We understand that delays in process equipment mean delays in your operations.
✅ How we ensure timely delivery:
Lean manufacturing techniques
Dedicated project managers
Real-time updates and milestone tracking
Most standard vessels delivered within 4–6 weeks. Rush orders possible on request
🧰 3. End-to-End After-Sales Support
Buying a vessel is just the beginning. SV Industries offers:
Installation guidance and drawings
Operation manuals
Troubleshooting and spare parts availability
Priority support for maintenance or upgrades
Our clients trust us for lifetime serviceability.
Frequently Asked Questions (FAQs) of SS Jacketed Vessels
What industries use Jacketed Vessels?
Jacketed Vessels are used in pharmaceuticals, chemicals, food processing, cosmetics, dairy, and more.
What is the material grade used for SS Jacketed Vessels?
We use SS 304, SS 316, and SS 316L based on corrosion resistance and application requirements
Can SS Jacketed Vessels be customized?
Yes, we offer custom-built SS Jacketed Vessels to match specific industrial needs.
How do I maintain an Jacketed Vessel?
Regular cleaning, pressure testing, and inspection ensure longevity and performance.
What is the lead time for manufacturing?
Typically, our production time ranges from 4 to 6 weeks, depending on customization.
What is the maximum capacity available?
We manufacture SS Jacketed Vessels ranging from 100 liters to 20,000 liters.
Do you provide installation support?
Yes, we offer on-site installation and training for proper usage.