Trusted Limpet Coil Reactor Vessel Manufacturer in India
Looking for a trusted Limpet Coil Reactor Vessel manufacturer in India? At SV Industries, we specialize in delivering precision-built reactor systems tailored for demanding industrial processes in the pharmaceutical, chemical, agrochemical, and food processing sectors. Each Limpet Coil Reactor Vessel is designed with high-efficiency heat transfer in mind, ensuring thermal stability, process control, and safety under pressure.
We offer custom fabrication options based on your operating temperature, material of construction (SS316/304, Alloy), and design standards. Whether you’re scaling up production or improving your batch performance, SV Industries ensures consistent quality, timely delivery, and after-sales technical support.
Our vessels are also engineered to be CIP-friendly, with hygienic nozzle placements and easy-access cleaning ports — essential for cleanroom manufacturing and GMP compliance.
Explore complementary equipment like our high-performance Industrial Agitators, SS Jacketed Vessels, and Heat Exchangers for a complete process solution.
➡️ Ready to discuss your requirement? Contact us today and work with a reliable Limpet Coil Reactor manufacturer you can count on.
What Is a Limpet Coil Reactor Vessel?
A Limpet Coil Reactor Vessel is a type of industrial pressure vessel designed for precise heating or cooling of chemical processes using a coiled jacket welded externally on the reactor shell. These coils—known as limpet coils—allow the circulation of steam, hot oil, or chilled water, enabling indirect heat exchange with the process media inside the reactor.
Unlike standard jacketed vessels, a limpet coil system offers higher pressure resistance, faster thermal response, and easier maintenance, making it ideal for batch processing in pharmaceutical, chemical, and food industries.
🔧 Construction & Material of Construction (MOC)
Limpet coil reactors are typically fabricated using:
SS304 / SS316 – suitable for pharma, food, and corrosive chemicals
Mild Steel (MS) – used in non-corrosive or cost-sensitive applications
Special Alloys – on demand for high-pressure or temperature-specific usage
The limpet coil is welded in a spiral or semi-spiral fashion on the outer wall of the reactor, ensuring efficient surface contact for maximum heat transfer.
🔁 Types of Limpet Coil Configuration
Single Coil – Used when only heating or cooling is needed
Double Coil – Supports both heating and cooling zones, controlled independently
The choice depends on your batch cycle requirements and media properties. Our engineering team can help you decide based on process volume, viscosity, and temperature range.
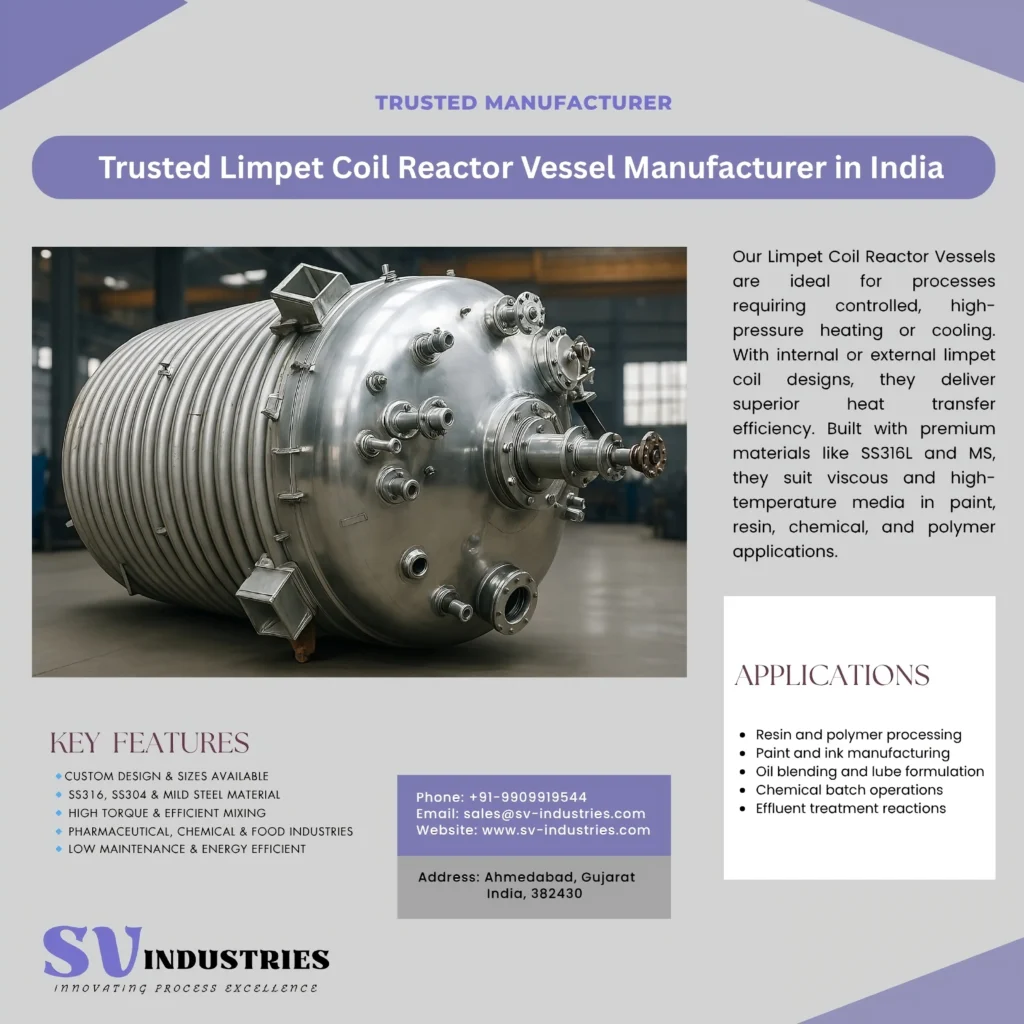
Working Principle: How Does a Limpet Coil Reactor Work?
A Limpet Coil Reactor operates on the principle of indirect heat exchange, where a heating or cooling medium flows through externally welded coils to regulate the internal temperature of the reactor without direct contact. This method ensures consistent temperature control, enhances safety, and supports energy-efficient batch operations.
This system is ideal for high-viscosity reactions, exothermic processes, and temperature-sensitive formulations used across chemical, pharmaceutical, food, and resin manufacturing industries.
🌡️ Heating Media Used in Limpet Coil Reactors
Depending on your process requirements, the limpet coil can be used for heating the reactor contents by circulating:
Steam – Ideal for rapid temperature rise and sterilization
Hot oil – Preferred for higher temperature stability in batch processes
Hot water – Used for moderate heating in food or water-based reactions
The inlet and outlet ports are precisely positioned to ensure uniform heating distribution across the coil layout.
❄️ Cooling Operation for Process Control
The same limpet coil system can also be used for cooling the reactor contents. In double coil systems, separate loops are provided for:
Chilled water or
Glycol solution
This is particularly beneficial in processes requiring quenching, end-of-reaction cooling, or post-batch stabilization. Cooling zones can be automated via control valves to optimize thermal cycling.
🔁 Flow Direction & Coil Layout Engineering
The coil layout is designed as a helical or spiral path for maximum heat transfer area. Flow can be configured as:
Counter-current (opposite direction to internal media) – offers better heat transfer efficiency
Co-current (same direction) – used when thermal gradients need to be minimized
Our engineers at SV Industries ensure that every reactor is designed with the correct coil pitch, weld quality, and pressure rating to deliver optimal process performance.
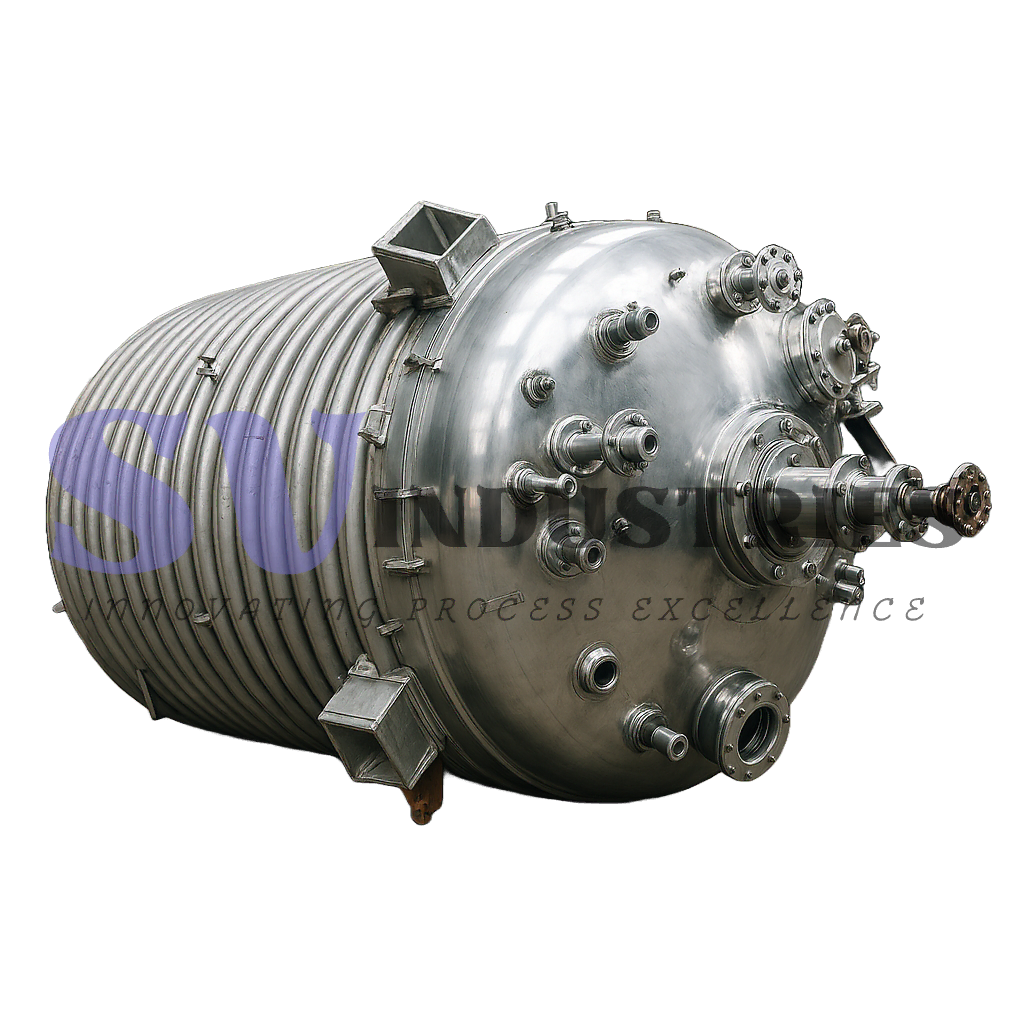
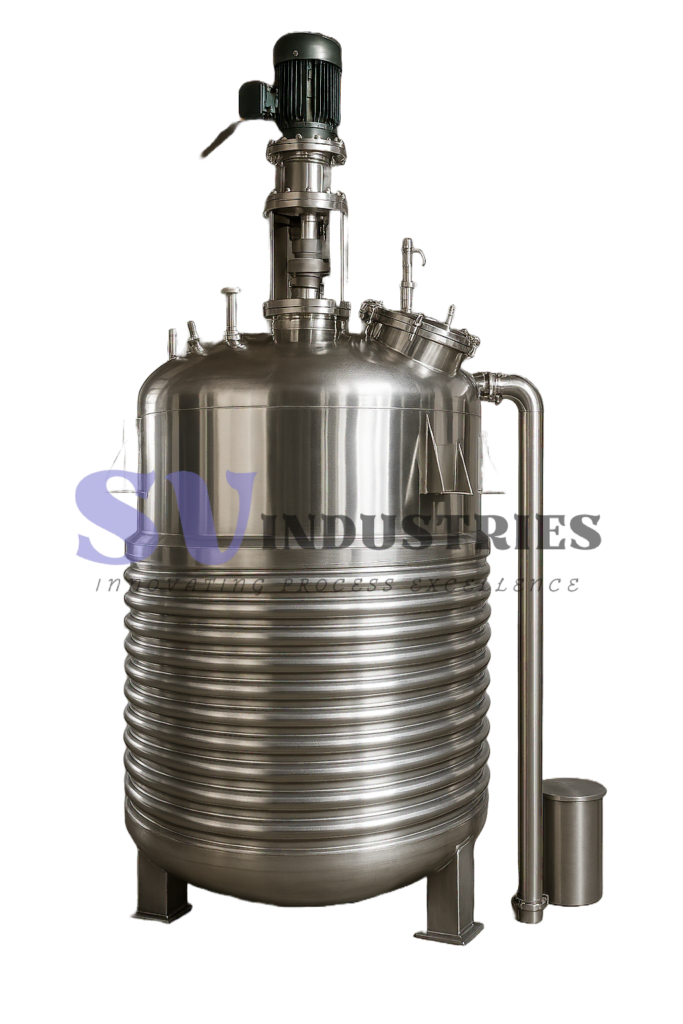
⚡ Batch Cycle Time Optimization in Limpet Coil Reactors
Optimizing batch cycle time is critical in chemical and pharmaceutical production, where every minute saved directly impacts throughput and cost. A well-designed limpet coil reactor vessel can significantly reduce cycle times by enabling faster heating/cooling, consistent temperature zones, and improved mixing dynamics.
The chart below provides a breakdown of typical batch cycle stages and how each phase can be optimized using our advanced coil designs and control systems.

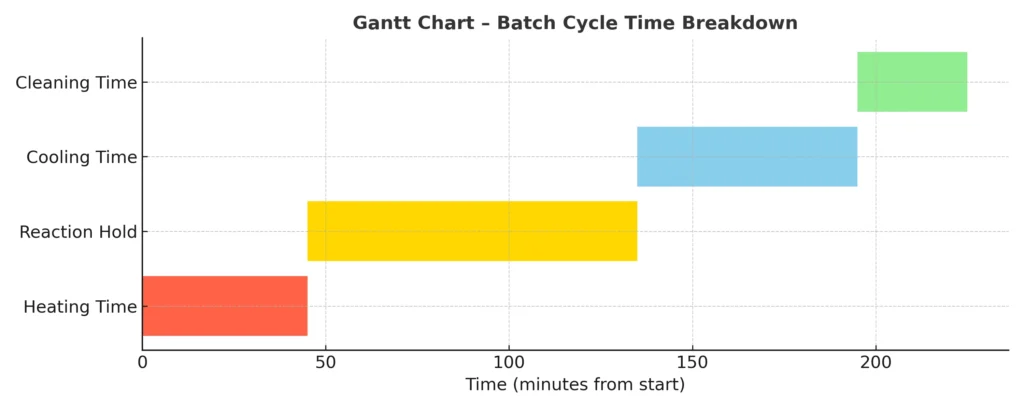
⏱️ Complete Batch Cycle Overview in Limpet Coil Reactor
Understanding the full cycle of operations is essential for plant engineers and production managers. The charts provide a breakdown of a standard batch process inside a limpet coil reactor, including all thermal and operational stages:
📊 Typical Time Allocation:
Heating: 45 mins
Reaction Hold: 90 mins
Cooling: 60 mins
Cleaning (CIP): 30 mins
➡️ Total Cycle Time: 3 hours 45 minutes
📌 These charts help:
Optimize cycle time for more batches per shift
Reduce downtime through better scheduling
Plan utility (steam/chiller) loads precisely
⚡ Start-up to Setpoint Ramp Time – Heating Curve Analysis
In batch processing, the start-up to setpoint time—also called ramp-up time—is a key indicator of reactor responsiveness. A shorter ramp-up time not only saves energy but also ensures faster batch readiness and minimizes waiting periods between operations.
This chart highlights the temperature rise curve and shows how SV Industries’ limpet coil reactors achieve quicker heat-up compared to conventional systems, thanks to superior heat transfer surface design and optimized flow layout.
Time is product—and our limpet coil reactor vessel proves it. The chart below captures the ramp-up curve from ambient (25 °C) to setpoint (90 °C), achieving steady-state in under 15 minutes. Whether your process involves pre-heating solvents, initiating exothermic reactions, or prepping high-purity intermediates, this rapid thermal response ensures maximum uptime and precise control.
The exponential shape reflects real-world heating dynamics with uniform jacket coverage and intelligent thermal mapping. Consistent with our thermal distribution charts, this graph shows you don’t just get fast heat—you get even heat. Download the dataset or embed the chart to audit your own scale-up expectations.
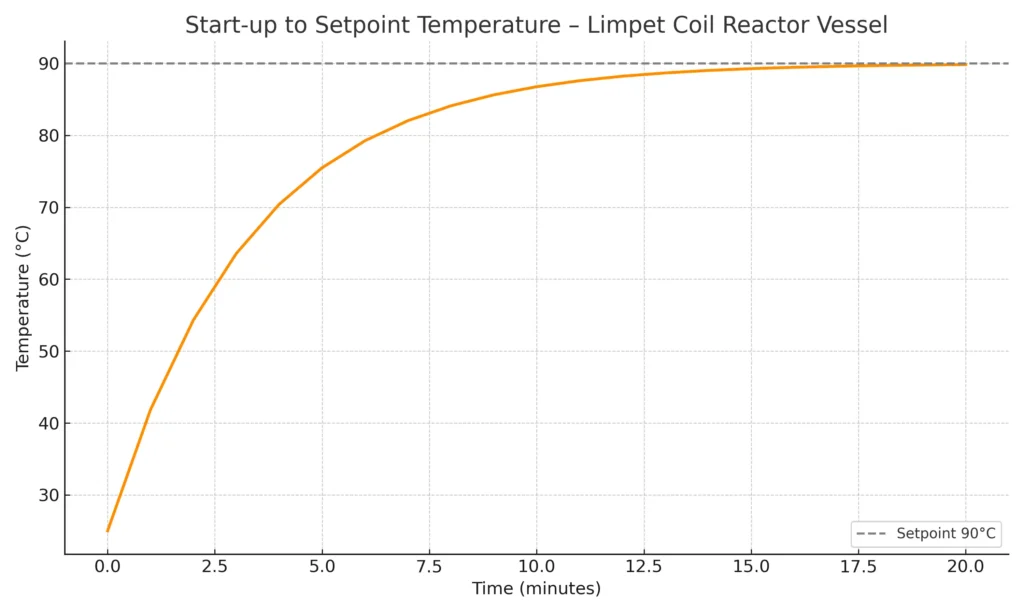
Customized Limpet Coil Reactor Vessels for Industry-Specific Needs
When it comes to process efficiency, one-size-fits-all reactors often fall short. That’s why industries across pharmaceuticals, chemicals, resins, and agrochemicals prefer custom-built limpet coil reactor vessels. At SV Industries, we specialize in delivering tailor-made reactor solutions designed to match your exact process requirements, space limitations, and material preferences.
🔧 Key Customization Options We Offer
Capacity Range | 100 Litres to 25,000 Litres |
Material of Construction | SS304, SS316L, Hastelloy, Special Alloys |
Limpet Coil Type | Inner Coil, Outer Coil, Single or Double Coil |
Agitator Type | Anchor, Hydrofoil, Helical, Turbine, Paddle, Hybrid |
Jacket Configuration | Limpet Jacket, Dimple Jacket, Combo |
Mounting Type | Skid-Mounted, Vertical, Horizontal |
Nozzle Layout | Custom Inlet/Outlet Based on P&ID |
Surface Finish | Mirror Finish, Electro-Polishing, Epoxy Coated |
Documentation Support | CAD Drawings, Validation Reports, TPI Ready |
🧪 Industry-Specific Examples
Pharmaceutical: SS316L reactor with mirror polish, GMP-compliant build & CIP-ready design.
Agrochemical: Double-coil limpet jacket for efficient heat exchange and batch cooling.
Paint & Resin: Agitator-equipped reactors with flameproof motors and quick batch turnover.
🧰 Design Validation & Documentation
We provide CAD drawings, stress validation reports, and support for third-party inspections (TPI) to ensure full transparency and quality assurance.
📞 Let’s Build Your Ideal Reactor
Need a custom-built limpet coil reactor vessel that aligns perfectly with your process?
👉 Contact SV Industries Now →
Limpet Coil vs Jacketed Reactor Vessel: Which Is Better for Your Process?
When selecting the right reactor for your process, understanding the difference between limpet coil and jacketed reactor designs can help improve heat transfer performance, reduce maintenance costs, and enhance process reliability. Here’s a detailed comparison to help you make an informed decision.
🔥 1. Heating & Cooling Efficiency
Limpet Coil Reactor:
Ideal for targeted heat transfer, especially in high-viscosity fluids or batch processes. The external coil ensures direct heat exchange with minimal thermal lag.Jacketed Reactor:
Best for uniform heating across the entire vessel surface. More suitable for low-viscosity fluids and continuous operations.
⚡ Jacketed vs Limpet Coil Reactor – Which One Delivers Better Thermal Efficiency?
When selecting a reactor for controlled heating or cooling, engineers often compare jacketed vessels and limpet coil reactors. The charts below present a performance-based comparison using five key parameters:
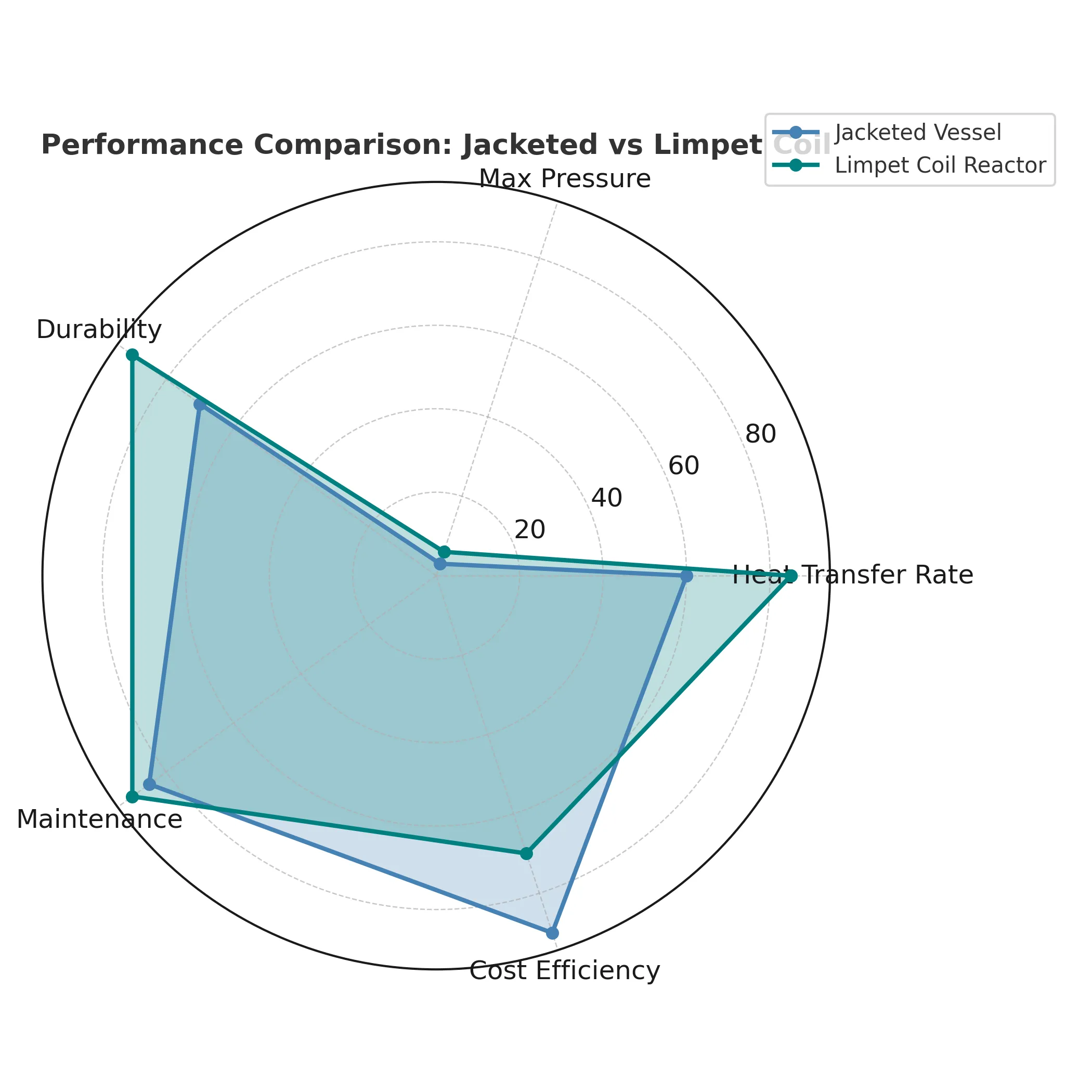

📌 Summary of Findings:
Heat Transfer Rate: Limpet coil offers up to 40% better thermal performance
Max Operating Pressure: Limpet coil design withstands double the pressure
Durability & Maintenance: Both score high, but limpet offers easier cleaning
Cost: Jacketed vessels are cheaper initially, but long-term efficiency favors limpet
🔧 2. Maintenance Requirements
Limpet Coil:
Easier to inspect and repair due to external placement. Leak detection and repair are more accessible without vessel disassembly.Jacketed Reactor:
Jacket failures may be harder to detect and repair, requiring downtime or complete removal of the jacket shell in some cases.
💨 3. Pressure Handling Capability
Limpet Coil:
Handles higher pressure media (e.g., steam or oil) better due to reinforced coil design and smaller flow channels.Jacketed Reactor:
Suited for moderate pressure ranges. Performance may degrade with high-pressure steam applications.
🧼 4. Cleaning & CIP Access
Limpet Coil:
Inner shell remains completely cleanable, as the coil is outside. Supports easy CIP (Clean-in-Place) systems and manual inspection.Jacketed Reactor:
May require extra access points or disassembly for internal cleaning verification, especially if scaling or fouling occurs.
🧠 Verdict for Engineers & Buyers
Criteria | Limpet Coil Reactor | Jacketed Reactor |
---|---|---|
Heat Transfer Efficiency | ✅ High (targeted) | ⚪ Uniform |
Pressure Handling | ✅ High-pressure suitable | ⚪ Moderate |
Maintenance Access | ✅ Easy | ⚪ Moderate |
Cleaning | ✅ CIP-friendly | ⚪ Requires care |
If your process requires high-temperature media, easy maintenance, and frequent cleaning, a limpet coil reactor is the smarter choice. For uniform heating and large-scale fluid movement, jacketed vessels may offer better results.
💧 Effect of Flow Rate on Heat Transfer in Limpet Coil Reactors
Efficient heat exchange in limpet coil reactors depends not only on the coil design but also on flow rate of the heating or cooling fluid. The scatter plot below reveals how increased coolant flow rate leads to a higher heat transfer coefficient (HTC), resulting in faster temperature control and energy savings.
✅ Key Observations:
At 20 LPM, HTC ≈ 180 W/m²K
At 60 LPM, HTC improves to over 310 W/m²K
Trendline shows diminishing returns at very high flow rates
These insights are crucial for:
Chemical engineers optimizing batch cooling
Plant designers selecting pump capacity
Clients aiming to reduce energy use
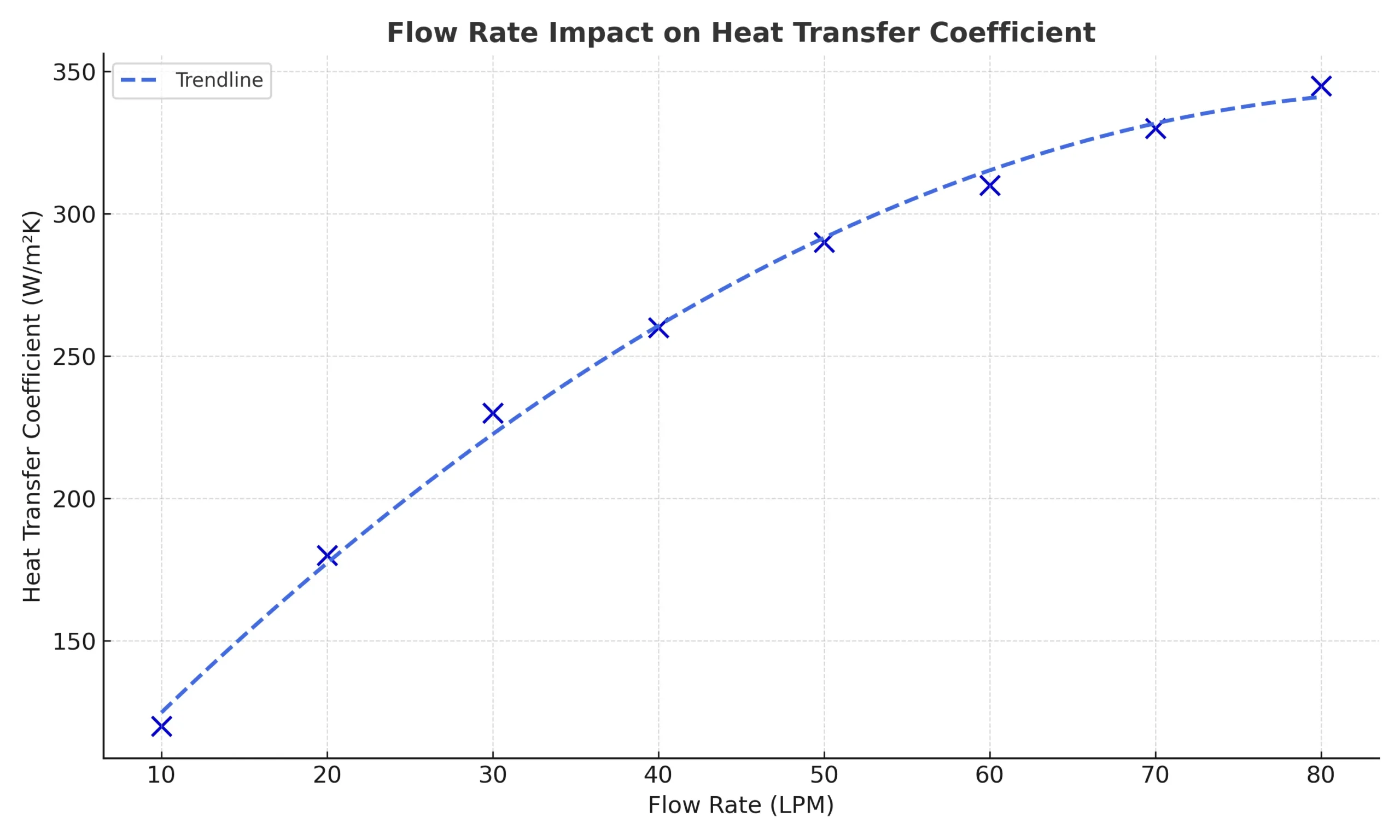
Heat Transfer & Process Efficiency Insights
In chemical and pharmaceutical manufacturing, heat transfer performance directly impacts batch time, energy cost, and product quality. At SV Industries, we engineer limpet coil reactor vessels that deliver precise thermal control and fast response times, ensuring your process runs at peak efficiency.
🔥 Why Efficient Heat Transfer Matters in Batch Processing
In batch operations, every minute saved during heating or cooling can significantly affect throughput and plant profitability. Our limpet coil designs maximize:
Surface contact area between coil and shell
Rapid temperature rise/fall with minimal lag
Even thermal distribution across the reaction mass
By reducing heating lag and overshoot, SV’s reactors can cut batch cycle times by 15–25% depending on process fluid and media used.
❄️ Cooling Time vs Product Quality: Why It Matters
Controlled and uniform cooling is critical for products sensitive to temperature drop rates — such as in:
Pharmaceutical crystallization
Food-grade emulsions
Specialty chemical reactions
Slower cooling or thermal shock can lead to:
Poor yield
Undesired by-products
Batch rejection
Our external limpet coil design offers gradual and controlled cooling, preserving product integrity while maintaining cleanability from the inside.
🔍 Why SV Industries Leads in Heat Transfer Design:
In-house CFD analysis for coil layout optimization
Coil MOC (SS304/316) selected for thermal conductivity & corrosion resistance
Customizable coil thickness for steam, oil, or glycol-based systems
❄️ Cooling Efficiency of Limpet Coil Reactor Based on Volume
The cooling performance of a limpet coil system plays a crucial role in batch time optimization and thermal control. The chart below showcases how cooling time increases with reactor volume — a key factor in high-volume chemical, pharma, and food industries.
📌 Typical observations:
500 L reactor cools from 90°C to 30°C in ~18 min
1000 L unit takes about 35 min
5000 L reactor may require over 2 hours
These values help project engineers design batch timing, chilling capacity, and CIP schedules.
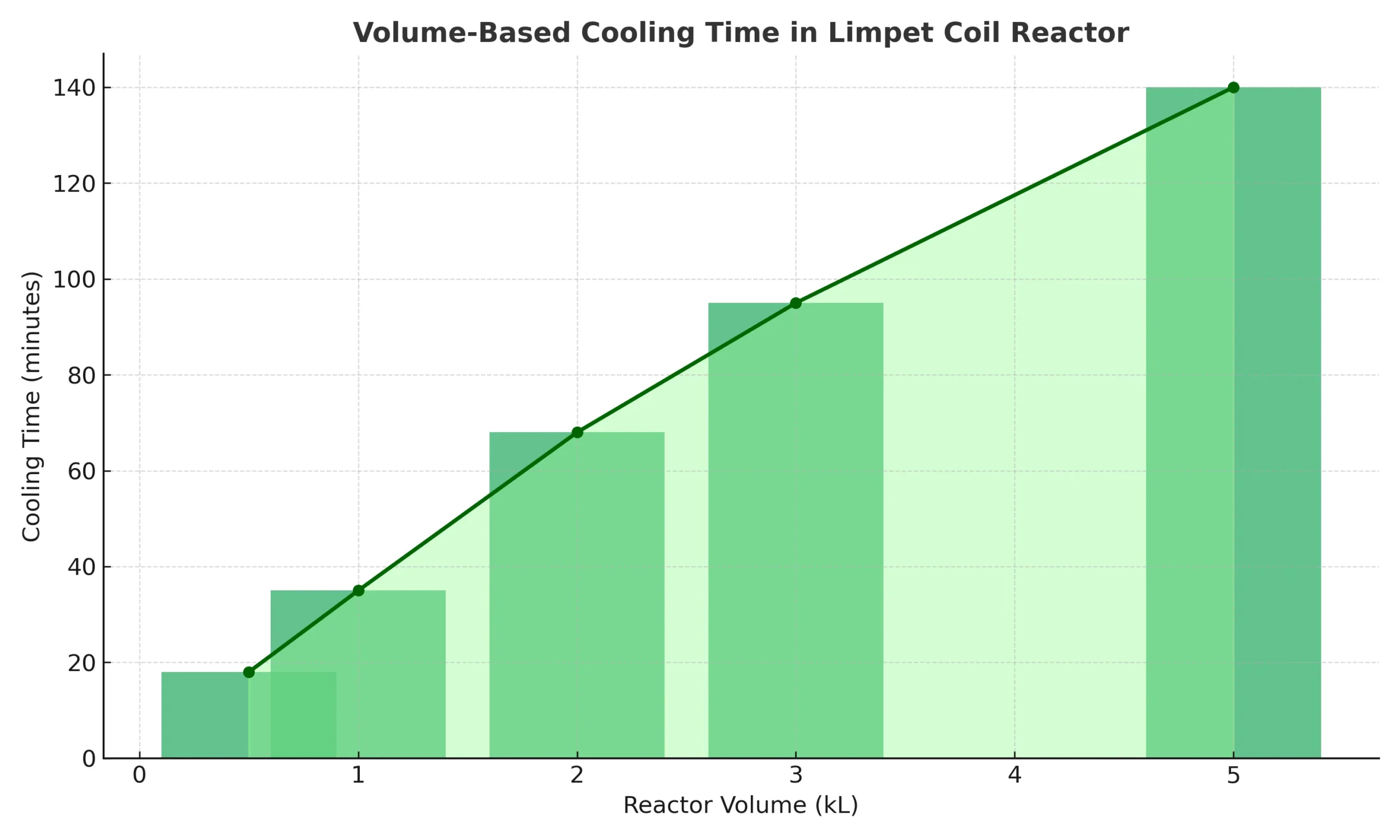
🔥 Heat Transfer Performance of Limpet Coil Reactor Vessel
Limpet coil reactor vessels are designed to deliver high thermal efficiency in demanding process environments. The chart below demonstrates the temperature rise from 30°C to 90°C over 40 minutes, showcasing the system’s ability to handle precise and consistent heating needs.
📌 This performance metric is critical for:
Pharmaceutical reactions requiring uniform heat
Chemical processes involving controlled exothermic or endothermic reactions
Heat-sensitive materials that demand gradual ramp-up
In most cases, a well-designed limpet coil can reduce heating time by up to 35% compared to conventional jacketed vessels.
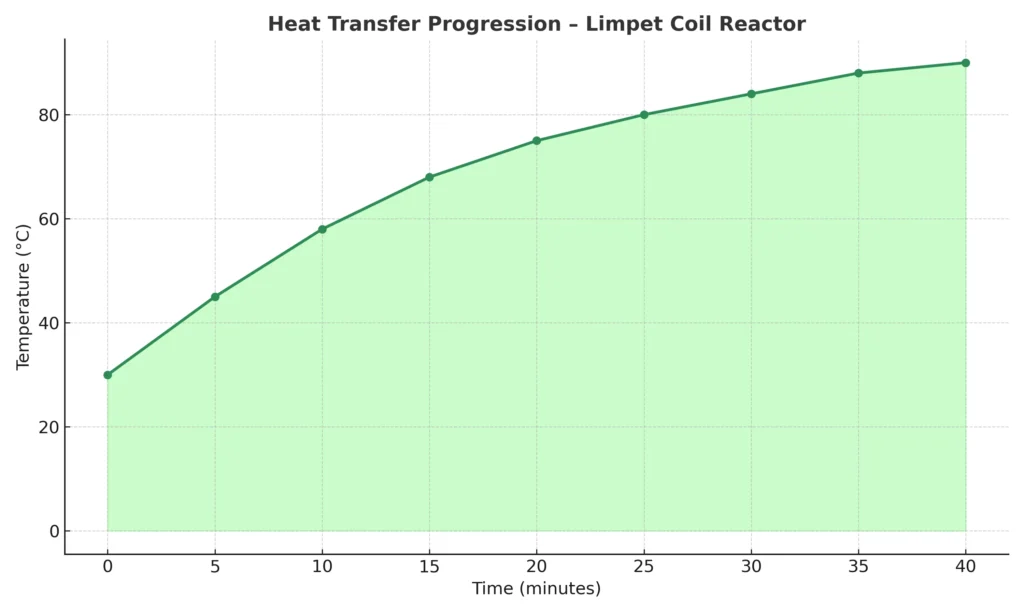
Cleaning & Maintenance Insights – CIP-Friendly Limpet Coil Reactors
Ease of cleaning is one of the most important purchase factors for industries like pharmaceuticals, food processing, and high-purity chemical applications. At SV Industries, we engineer CIP-compatible limpet coil reactor vessels that simplify cleaning and reduce downtime — without compromising on hygiene or performance.
🚿 Integrated CIP Systems: Spray Ball & External Pump Options
Our limpet coil reactors can be equipped with:
Fixed Spray Balls: Ideal for automated Clean-in-Place (CIP) cycles; ensures 360° internal surface coverage.
Rotary Spray Heads (Optional): Enhanced jet cleaning for viscous or high-residue materials.
External CIP Pump Integration: Suited for large-scale SS reactors where flow rate control is critical.
✅ All internal surfaces are mirror polished (Ra ≤ 0.4 µm), ensuring residue-free operation
✅ No dead zones — engineered with sloped bottom for complete drainability
📌 Related: See our Working Principle to understand coil placement and cleaning access.
📏 CIP Cycle Efficiency in Limpet Coil Reactors
Efficient cleaning is a major concern for pharma, biotech, and specialty chemical industries. Limpet coil reactors, when integrated with CIP spray balls or external pump loops, allow for faster solvent distribution and reduced manual intervention.
Below is a comparative breakdown of CIP cycle time, helping you choose the best reactor type based on cleaning performance.
🧼 CIP (Clean-In-Place) Cycle Efficiency of Limpet Coil Reactor
Pharma and food-grade applications demand fast, effective cleaning cycles. This CIP Efficiency chart clearly shows that Limpet Coil Reactor Vessels offer faster cleaning and use significantly less water compared to jacketed vessels.
🔹 Cleaning Time: Limpet coil = 25 min vs Jacket = 40 min
🔹 Water Usage: Limpet coil = 180 L vs Jacket = 300 L
This makes limpet coil vessels a superior choice for industries with strict hygiene protocols and limited downtime tolerance.
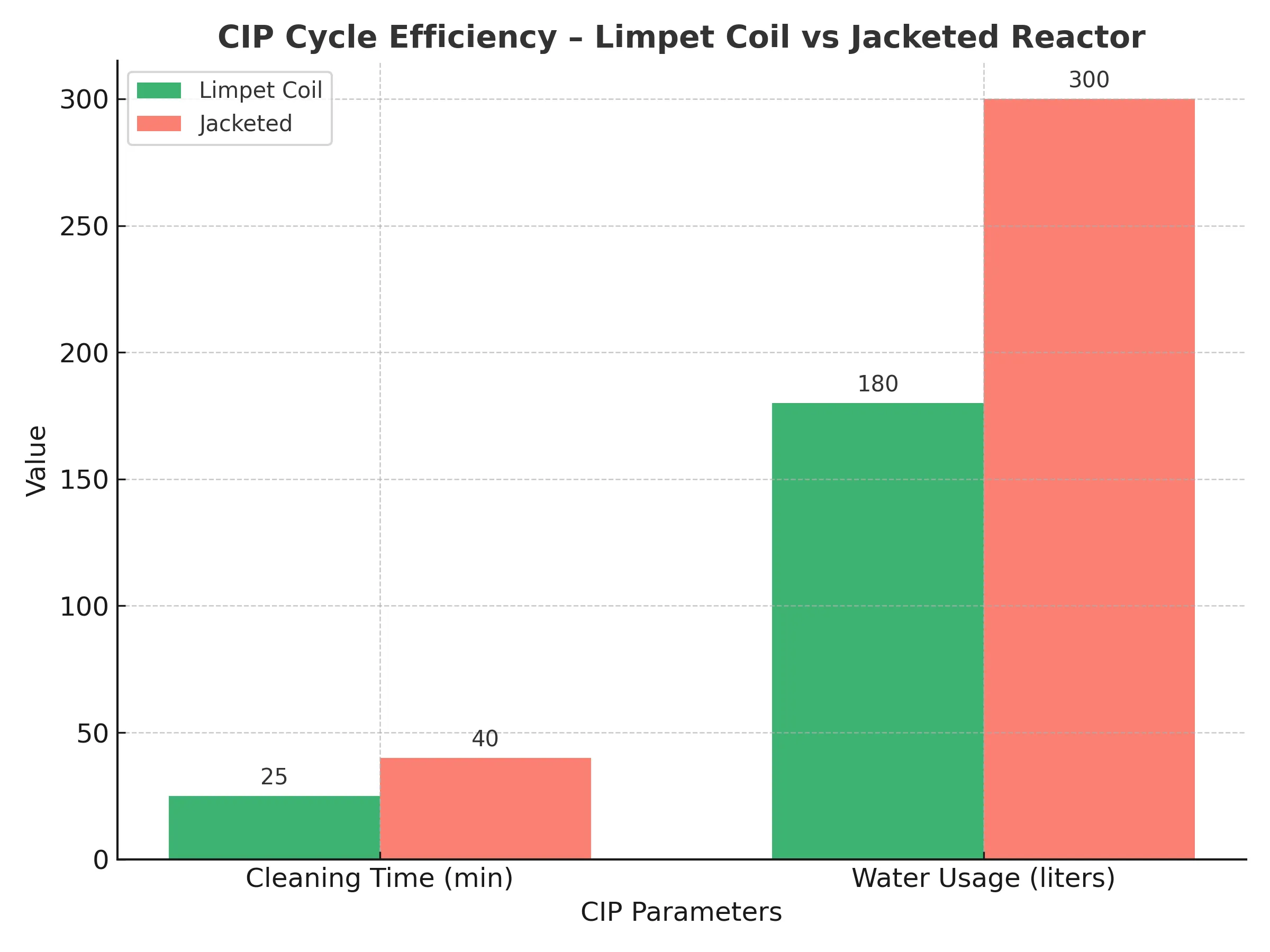
Parameter | Limpet Coil Reactor | Jacketed Reactor |
---|---|---|
CIP Cycle Time (min) | 25 | 40 |
Water Usage (liters) | 180 | 300 |
Cleaning Efficiency (%) | 98 | 92 |
🧪 Solvent Usage & Cleaning Time Estimates
Cleaning time depends on the product and solvent, but SV-designed reactors typically offer:
Batch Type | Solvent | Avg. CIP Time |
---|---|---|
API Crystallization | IPA / Ethanol | 25–35 minutes |
Emulsions | Hot water + NaOH | 15–25 minutes |
Adhesives | Acetone | 30–45 minutes |
🛠️ Low Maintenance = Longer Reactor Life
No internal coil = no internal clogging
Less chance of corrosion due to external coil system
Easy inspection ports and manholes for periodic checks
All valves and nozzles are GMP-compliant and CIP-ready
🔗 Technical Specifications & Material Grades – includes surface finish, MOC, flange details
Why Choose SV Industries for Your Limpet Coil Reactor Vessel Needs
When you’re investing in a Limpet Coil Reactor, you need more than just equipment — you need a reliable partner who understands your process, deadlines, and industry standards. That’s where SV Industries delivers unmatched value.
🔧 Engineered In-House for Performance That Lasts
We handle everything — from design to manufacturing — under one roof in Ahmedabad, Gujarat. Our expert team ensures that each reactor meets the strictest quality, safety, and process optimization standards.
📐 Custom Sizes to Match Every Application
Whether you’re a pilot plant looking for 100-liter units or a production facility requiring 20,000-liter reactors, we fabricate each vessel to fit your process needs — no compromises.
🏭 Multi-Industry Expertise You Can Count On
From pharmaceuticals and specialty chemicals to FMCG and food-grade applications, our vessels are designed to handle complex thermal cycles, corrosive media, and strict GMP compliance.
⏱️ Timely Delivery with Ongoing Technical Support
We take pride in our on-time project execution. And it doesn’t end at dispatch — our post-sales support includes installation guidance, cleaning protocols, and process troubleshooting — all handled by experienced engineers.
🔗 Explore Related Solutions:
SS Jacketed Vessels – For alternative thermal control options
Industrial Chemical Reactors – Scalable designs up to 20KL
Anchor Impeller – Compatible mixing solutions for high-viscosity applications
Frequently Asked Questions (FAQs) about Limpet Coil Reactor Vessel
What is the working pressure of limpet coil vessels?
At SV Industries, our limpet coil reactor vessels are typically designed for a working pressure range of up to 12 bar (kg/cm²). However, we offer customization up to 16 bar depending on process requirements and selected material grade. Both internal vessel pressure and limpet coil pressure can be designed independently.
Are these reactors suitable for corrosive materials?
Yes, we manufacture reactors using SS 316, SS 316L, and other corrosion-resistant alloys. These materials are ideal for handling acids, alkalis, solvents, and highly reactive chemicals. Our Heat Exchanger systems and agitators are also designed to support corrosive process conditions.
Do you offer third-party inspection for reactor vessels?
Absolutely. We support third-party inspection (TPI) from agencies like TUV, BV, SGS, or any client-nominated inspection body. Inspection includes material test certificates, hydro pressure tests, welding joint reports, and dimension verification.
What is the typical delivery time for limpet coil reactor vessels?
Standard delivery time ranges from 3 to 5 weeks, depending on capacity (100L to 20KL), material availability, and custom features. For urgent requirements, we offer priority production with pre-approved drawings and fast-tracked sourcing.
Can limpet coil reactors be used for both heating and cooling?
Yes. Limpet coils are designed for dual operation — either heating using steam/hot oil or cooling using chilled water/brine. This flexibility makes them ideal for processes requiring thermal cycling.
What agitator types are compatible with limpet coil reactors?
Our limpet coil reactors are compatible with a wide range of agitator designs, including Anchor Impeller, Helical Impeller, Pitch Blade Turbine, and Rushton Turbine. Selection depends on viscosity, mixing speed, and batch volume.
Is cleaning and maintenance easy for these vessels?
Yes. We offer CIP (Clean-In-Place) design, mirror-polished interiors, and drain valve optimization to make cleaning hassle-free. For industries like pharma and FMCG, we also offer electropolishing and FDA-grade gaskets for hygiene compliance.
Looking for a Reliable Limpet Coil Reactor Manufacturer?
We specialize in precision-engineered SS Limpet Coil Reactors, trusted by industries across India for their durability, performance, and custom design flexibility. Whether you need expert consultation or a tailored solution for your process…